Custom Centerless Surface Grinders Precision Engineering for Modern Manufacturing
In the ever-evolving landscape of manufacturing, precision and efficiency play crucial roles in maintaining competitiveness. Among the various tools that enhance productivity, custom centerless surface grinders stand out as essential equipment in the machining process. These machines are designed to grind workpieces without the need for a central axis, offering significant advantages in terms of speed, accuracy, and versatility.
Understanding Centerless Grinding
Centerless grinding is a process that allows for the grinding of cylindrical parts without the need for a spindle to hold them in place. Instead, parts are placed between two wheels a grinding wheel and a regulating wheel. The regulating wheel controls the feed rate and the rotational speed of the workpiece, while the grinding wheel performs the actual material removal. This design enables the grinder to work efficiently on multiple parts simultaneously, making it ideal for high-volume production settings.
Customization in Design
One of the most significant advantages of custom centerless surface grinders is their adaptability to meet specific production needs. Manufacturers often require tailored solutions to accommodate unique workpiece geometries, materials, and surface finish requirements. Custom grinders can be engineered to handle a variety of sizes and shapes, including long bars, small tubes, or complex profiles. This level of customization ensures that manufacturers can produce parts that meet precise specifications, enhancing quality and reducing waste.
Precision and Efficiency
custom centerless surface grinder
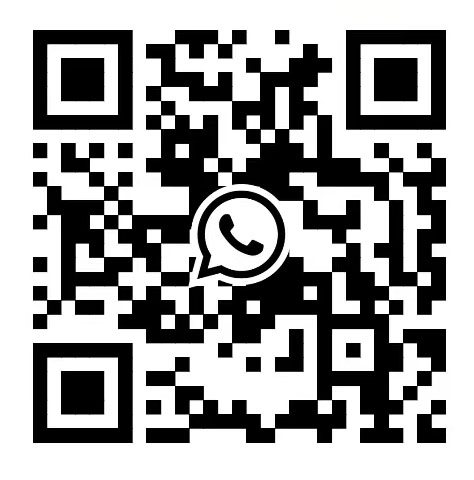
The primary benefits of using custom centerless surface grinders include increased precision and operational efficiency. With advancements in technology, modern centerless grinders are equipped with high-precision components and sophisticated control systems. These features allow for tighter tolerances and consistent surface finishes, which are critical in industries such as automotive, aerospace, and medical device manufacturing. The ability to achieve such precision contributes to the overall quality of the final product, ensuring that it meets both regulatory standards and customer expectations.
Furthermore, the design of centerless grinders facilitates a continuous feeding operation, significantly reducing cycle times. This efficiency is particularly important in large-scale production environments where time is of the essence. By minimizing the downtime associated with part loading and unloading, manufacturers can optimize their workflow and increase overall productivity.
Integration with Advanced Technologies
The integration of advanced technologies such as automation and Industry 4.0 principles further enhances the capabilities of custom centerless surface grinders. Manufacturers can implement automated loading and unloading systems, allowing for unattended operation and further reducing labor costs. Additionally, with the advent of smart manufacturing, grinders can be equipped with sensors and IoT connectivity to monitor performance in real-time, enabling predictive maintenance and reducing the likelihood of unexpected downtime.
Conclusion
Custom centerless surface grinders represent a critical investment for manufacturers looking to improve their machining capabilities. By providing tailored solutions that enhance precision and efficiency, these machines enable businesses to remain competitive in a rapidly changing market. As manufacturing continues to advance technologically, the importance of high-quality, customizable equipment will only increase. Companies that leverage the advantages of custom centerless surface grinders will undoubtedly benefit from improved production processes, leading to higher-quality products and greater customer satisfaction. Embracing this technology is not just a matter of operational efficiency; it is a vital step toward achieving long-term success in the manufacturing sector.