High-Quality Tube Internal Polishing Machine A Game Changer for Metal Fabrication
In the realm of metal fabrication, precision and quality are paramount to ensuring the longevity and performance of products. Among the various processes involved, tube internal polishing has emerged as a critical component, particularly in industries such as automotive, aerospace, and pharmaceuticals, where cleanliness and surface quality are non-negotiable. The advent of high-quality tube internal polishing machines has revolutionized this process, offering unparalleled efficiency and superior results.
The Importance of Internal Polishing
The internal surfaces of tubes and pipes often harbor imperfections, such as weld seams, burrs, and surface roughness, which can negatively impact fluid flow and increase the likelihood of corrosion. This is particularly critical in applications involving high-pressure fluids or sensitive substances that require sterility, such as in pharmaceutical manufacturing. A well-polished interior ensures not only aesthetic appeal but also functional integrity, making it essential to invest in advanced polishing technology.
Overview of Tube Internal Polishing Machines
High-quality tube internal polishing machines are designed to automate and enhance the polishing process. These machines utilize various techniques, including mechanical, chemical, and electrolytic polishing, to achieve a smooth and even surface finish. The selection of the right machine depends on several factors, including the material of the tube, the required finish quality, and the specific application.
1. Mechanical Polishing This method involves the use of abrasive materials and tools that grind down imperfections and achieve a desired surface smoothness. Mechanical polishing is effective for a wide range of materials, including stainless steel and aluminum. Machines may be equipped with various tools such as brushes, belts, or rotary heads tailored to the specific material and finish requirements.
2. Chemical Polishing Also known as passivation, this method employs chemical agents to remove surface impurities and achieve a smooth finish without the need for mechanical abrasion. Chemical polishing is particularly beneficial for achieving mirror-like finishes on stainless steel tubes, which is crucial in applications where hygiene is vital.
3. Electrolytic Polishing This advanced technique involves submerging the tube in an electrolyte solution and applying an electrical current. The process removes material from the surface at a molecular level, resulting in a highly polished finish and enhanced corrosion resistance. Although initially more costly, electrolytic polishing delivers superior results, making it the preferred choice for high-end applications.
high quality tube internal polishing machine
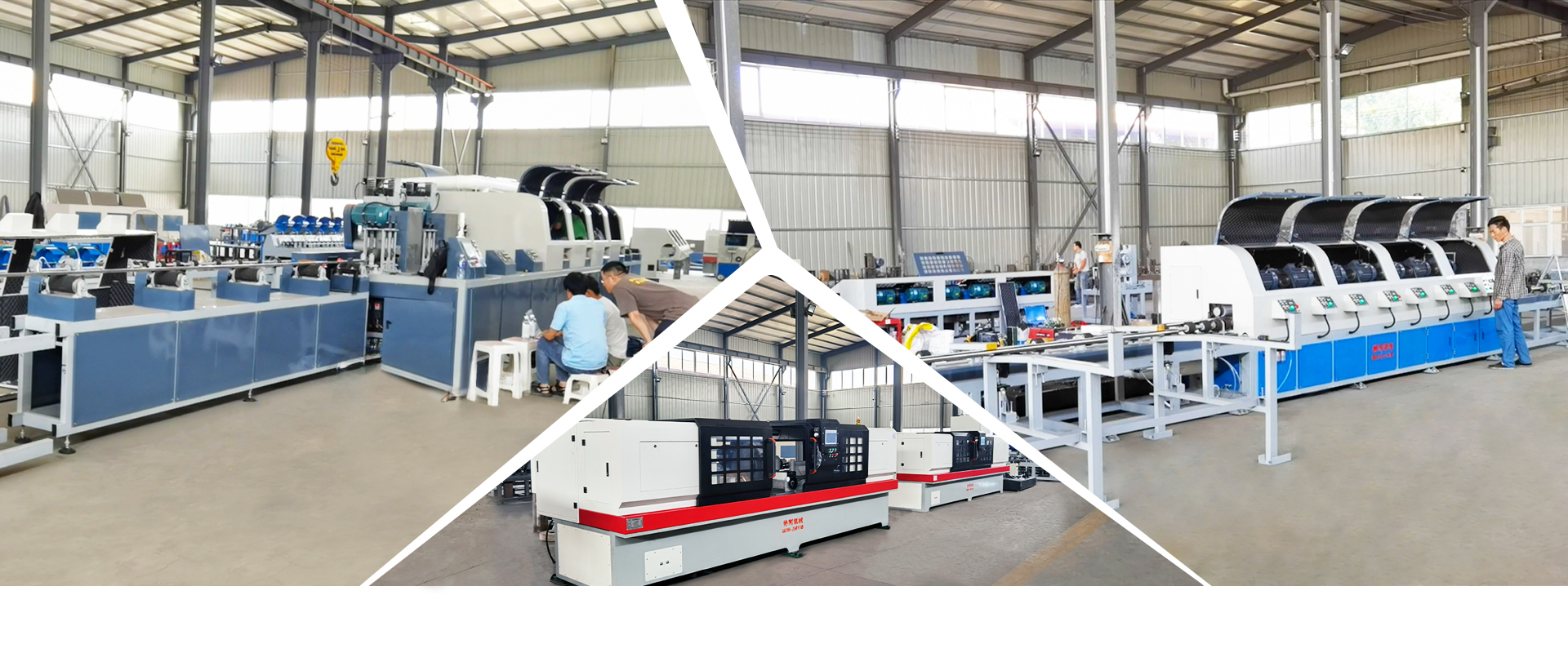
Benefits of High-Quality Tube Internal Polishing Machines
1. Enhanced Surface Quality The primary benefit of employing high-quality polishing machines is the significant improvement in tube surface quality. A smooth internal surface minimizes turbulence in fluid flow, reduces drag and pressure losses, and enhances overall system efficiency.
2. Increased Durability and Longevity Regular polishing can protect against corrosion and wear, thereby extending the lifespan of tubes and pipes. This is especially crucial in harsh environments or when dealing with corrosive fluids.
3. Time and Cost Efficiency Automation provided by modern polishing machines drastically reduces labor costs and processing time. High-speed operations and consistent quality ensure that manufacturers can meet tight production timelines without compromising on standards.
4. Versatility High-quality polishing machines can accommodate a wide range of tube sizes and materials, making them suitable for various industries. This versatility allows manufacturers to serve diverse markets while maintaining a focus on quality.
5. Eco-Friendly Options Many newer models of polishing machines incorporate environmentally friendly practices, using biodegradable chemicals and reducing waste generated during the polishing process.
Conclusion
The advancement in high-quality tube internal polishing machines represents a significant leap forward in metal fabrication technology. By improving surface quality, enhancing durability, and increasing operational efficiency, these machines have become indispensable tools for manufacturers aiming to meet the stringent demands of modern industries. Investing in a state-of-the-art tube internal polishing machine is not just an upgrade—it's a commitment to excellence that can lead to better performance, higher customer satisfaction, and a stronger competitive edge. As industries continue to evolve, the importance of precision fabrication will only grow, making high-quality polishing solutions more essential than ever.