High-Quality SMT Centerless Grinders Revolutionizing Precision Machining
In the realm of precision machining, the importance of grinder technology cannot be overstated. Among the various types of grinders available, the SMT (Small Machine Tool) centerless grinder has emerged as a pivotal player in the manufacturing landscape. These machines are renowned for their ability to deliver high-quality grinding results while ensuring efficiency and minimizing operational costs.
What is Centerless Grinding?
Centerless grinding is a manufacturing process that involves grinding the outer surface of a workpiece without the need for a centering fixture. Unlike traditional grinding methods that fix the workpiece between two centers, centerless grinders utilize a system that holds the workpiece in place while it is fed through the grinding wheel. This unique setup allows for continuous operation, increased production rates, and a reduction in setup time.
The Mechanism Behind SMT Centerless Grinders
SMT centerless grinders are designed with precision engineering in mind. They typically consist of three key components the grinding wheel, the regulating wheel, and the workpiece support. The grinding wheel is responsible for removing material from the workpiece, achieving the desired diameter and surface finish. The regulating wheel sets the speed and feeds the workpiece into the grinding area, ensuring that it is held securely and accurately during the process.
Advancements in technology have led to the incorporation of CNC (Computer Numerical Control) systems in modern SMT centerless grinders. These systems enable operators to input precise specifications for each job, allowing the machine to adjust its operations in real time. This level of control not only enhances the accuracy of the grind but also minimizes human error, resulting in products that meet the highest quality standards.
Benefits of SMT Centerless Grinders
high quality smt centerless grinder
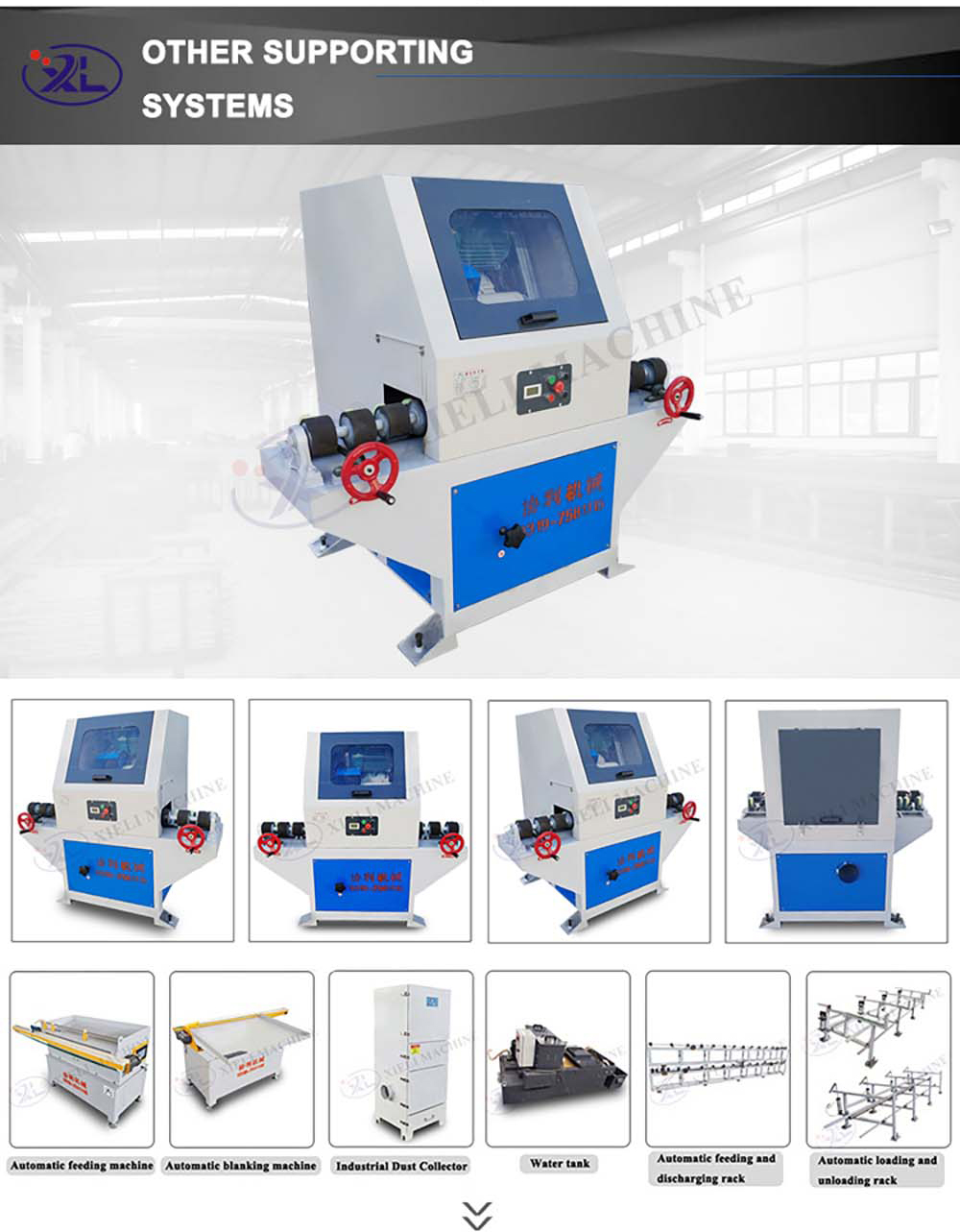
1. Precision and Consistency One of the most significant advantages of using SMT centerless grinders is the ability to achieve high precision and consistency in part production. The machines are capable of maintaining tight tolerances, which is crucial in industries such as automotive, aerospace, and medical manufacturing.
2. Efficiency in Production The continuous operation feature of centerless grinders allows for high throughput. Once set up, these machines can run for hours without interruption, making them ideal for high-volume manufacturing environments. This efficiency translates into lower production costs and quicker turnaround times.
3. Versatility SMT centerless grinders can accommodate a wide variety of materials and part sizes. Whether working with hard metals, plastics, or composites, these grinders are versatile enough to handle different applications, making them valuable assets in any manufacturing facility.
4. Reduced Setup Time Traditional grinding methods often require extensive setup and fixture changes. However, SMT centerless grinders are designed for minimal setup time, allowing operators to quickly transition between different jobs. This flexibility is essential for manufacturers looking to adapt to changing market demands.
5. Improved Surface Finish Centerless grinding produces superior surface finishes compared to other methods. This is particularly advantageous in applications where aesthetics or surface smoothness is critical, such as in the production of optical components or precision machinery.
Conclusion
As industries continue to evolve, the need for high-quality machining solutions becomes increasingly vital. SMT centerless grinders stand at the forefront of this evolution, offering manufacturers the precision, efficiency, and versatility required to succeed in competitive markets. By investing in these advanced grinding technologies, businesses can enhance their production capabilities and deliver superior products that meet the rigorous demands of today’s consumers. In a world where quality and efficiency matter, SMT centerless grinders represent a significant leap forward in the future of precision machining.