High-Quality Pipe Inside Polishing Machines An Essential Tool for Precision Engineering
In the realm of manufacturing and engineering, the quality of finished products is paramount. For industries that rely on piping systems, such as oil and gas, construction, and automotive, the internal surface finish of pipes plays a crucial role in both performance and longevity. Enter the high-quality pipe inside polishing machine – a revolutionary tool designed to enhance the internal surface of pipes, ensuring that they meet the highest standards of quality and efficiency.
The Importance of Internal Pipe Polishing
Pipes are subjected to various stresses and pressures during their operational life, making it essential for their internal surfaces to be smooth and free from defects. Rough internal surfaces can lead to inefficient fluid flow, increased friction, and ultimately, higher operational costs. Moreover, impurities and surface irregularities can cause corrosion, reducing the lifespan of pipes and leading to costly repairs and replacements.
Internal pipe polishing is a critical process that removes metal burrs, weld seams, and surface irregularities. It helps improve the flow characteristics of the fluid passing through the pipes, ensures better thermal conductivity, and reduces the risk of contamination in industries such as food and pharmaceuticals.
Features of High-Quality Pipe Inside Polishing Machines
A high-quality pipe inside polishing machine is engineered with advanced features that enhance its effectiveness and usability. Key attributes include
1. Adjustable Polishing Heads These machines often come equipped with detachable polishing heads that can be adjusted to accommodate various pipe diameters and wall thicknesses, providing versatility across different projects.
2. Automated Control Systems Many modern polishing machines are equipped with CNC (Computer Numerical Control) systems that allow for precise control over the polishing process. This automation not only improves efficiency but also increases the consistency of the finish.
high quality pipe inside polishing machine
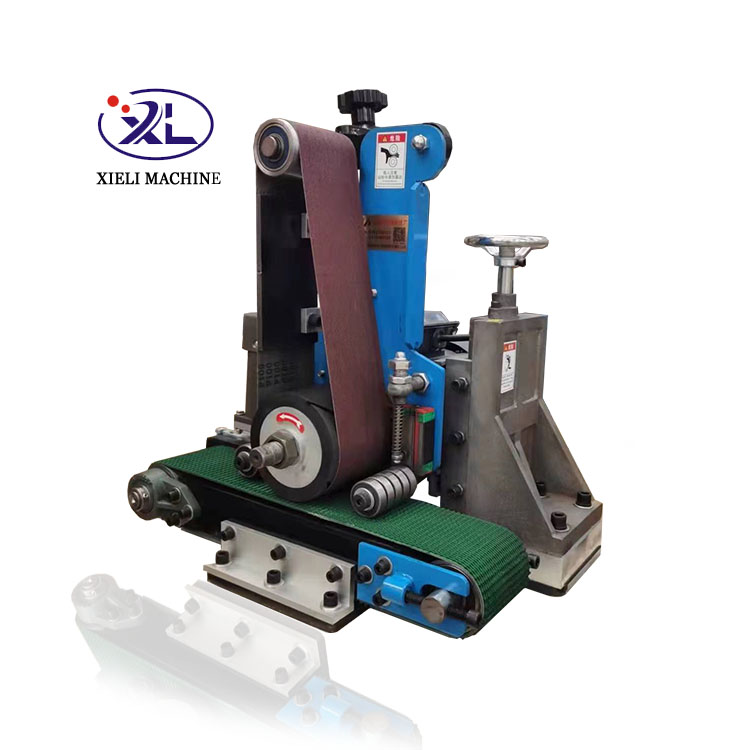
3. Multiple Polishing Stages High-quality machines typically offer multiple polishing stages, enabling operators to achieve a mirror-like finish. This is crucial for applications where fluid dynamics and cleanliness are critical.
4. Robust Construction A durable design is essential for machines operating in demanding industrial environments. High-quality polishing machines are often made from high-grade materials, ensuring longevity and reliability even under continuous use.
5. Safety Features Advanced polishing machines are designed with operator safety in mind, incorporating features such as emergency stop buttons, protective shields, and automated shut-off mechanisms in the case of malfunctions.
Applications Across Industries
The versatility of high-quality pipe inside polishing machines makes them suitable for a wide range of industries. In the oil and gas sector, these machines are essential for refining pipelines to ensure efficient fluid transport. In the construction industry, polished pipes are crucial for plumbing and HVAC systems, where optimal flow and minimal resistance are essential.
Furthermore, in the automotive sector, internal pipe polishing is vital for enhancing the performance of exhaust systems, fuel lines, and hydraulic systems, all of which require precise and smooth operation.
Conclusion
In conclusion, high-quality pipe inside polishing machines represent a significant advancement in the field of manufacturing and engineering. As industries increasingly demand better performance and efficiency, the role of internal pipe polishing becomes even more critical. By investing in advanced polishing technology, manufacturers can ensure that their products meet the stringent quality standards required in today’s competitive market.
With the continual evolution of materials and the need for enhanced performance, the importance of maintaining smooth internal pipe surfaces cannot be overstated. High-quality pipe inside polishing machines not only contribute to improved operational efficiency but also play a vital role in extending the lifespan of piping systems across various sectors. As technology progresses, these machines will undoubtedly become even more sophisticated, further driving the quality and reliability of piping solutions worldwide.