High-Quality Cylindrical Polishing Machines Enhancing Surface Finish with Precision
In the world of manufacturing and finishing, achieving a superior surface finish is a critical aspect that significantly influences product performance and aesthetics
. High-quality cylindrical polishing machines have emerged as essential tools in various industries, including automotive, aerospace, medical, and electronics, where the level of precision and smoothness of metal surfaces is paramount.Cylindrical polishing is a process that enhances the surface quality of cylindrical workpieces, such as shafts, tubes, and rods. The primary goal is to eliminate imperfections and create a polished finish that not only improves the appearance but also provides better corrosion resistance and reduces friction. This is particularly important in applications where components must work together seamlessly, as even minor surface irregularities can lead to increased wear and failure over time.
One of the key features of high-quality cylindrical polishing machines is their ability to deliver consistent results with minimal operator intervention. These machines are typically equipped with advanced controls and automation systems that ensure precise adjustments in polishing parameters, such as speed, pressure, and feed rate. This level of automation not only increases efficiency but also reduces the likelihood of human error, leading to improved quality and repeatability in the polishing process.
The construction of a high-quality cylindrical polishing machine is crucial to its performance. Machines designed with rigid frames and high-grade components can withstand the stresses of heavy-duty operations while maintaining stability and alignment. This rigidity minimizes vibrations during the polishing process, which is essential for achieving a smooth finish. Furthermore, high-quality machines often feature advanced abrasive systems that utilize various polishing bars, wheels, or belts made from durable materials that optimize the material removal rate and surface finish quality.
high quality cylindrical polishing machine
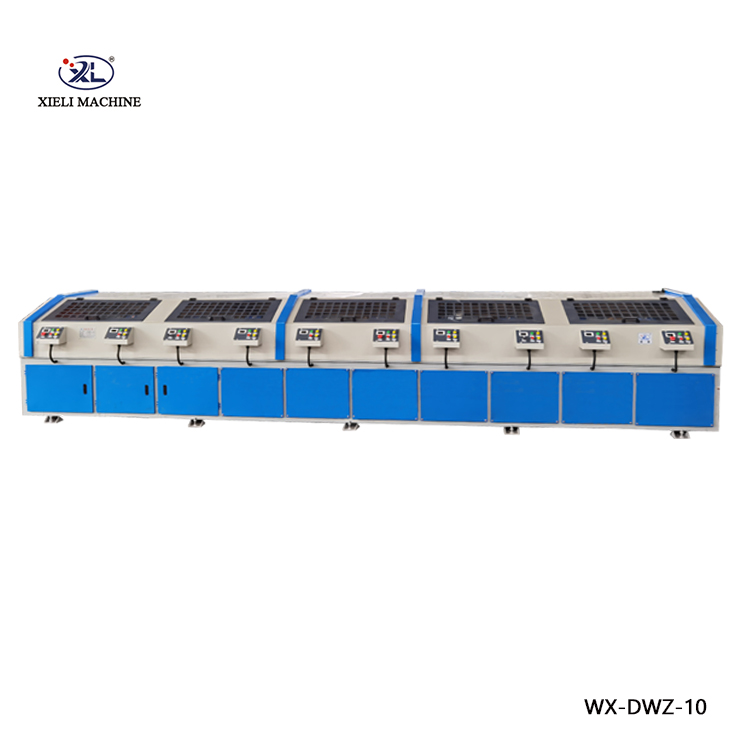
Another important aspect of cylindrical polishing machines is their versatility. Many modern machines are designed for both wet and dry polishing applications, allowing users to select the appropriate technique based on their specific needs. Wet polishing involves using a lubricant or coolant that not only helps in cooling the workpiece but also aids in reducing dust and debris. This is especially beneficial in maintaining a cleaner working environment and prolonging the life of both the polishing abrasives and the machine itself.
Moreover, manufacturers have begun to incorporate ergonomic designs into cylindrical polishing machines, ensuring ease of use and operator comfort. Features such as adjustable work heights, intuitive control panels, and safety mechanisms contribute to a more user-friendly experience, which is essential in high-volume production settings.
As industries continue to evolve and demand higher precision and quality, the importance of selecting the right cylindrical polishing machine cannot be overstated. Investing in high-quality equipment often translates into longer-lasting tools, reduced operational costs, and improved overall productivity. As a result, many businesses are turning to advanced cylindrical polishing machines that not only meet their current needs but also have the capability to adapt to future requirements.
In conclusion, high-quality cylindrical polishing machines are critical to maintaining the standards of surface finish demanded in today's manufacturing landscape. By providing consistent, efficient, and precise polishing capabilities, these machines are indispensable in ensuring that products meet the rigorous quality requirements of various industries. As technology continues to advance, the evolution of cylindrical polishing machines will undoubtedly play a significant role in shaping the future of surface finishing processes, offering even greater capabilities and efficiencies.