High-Quality Centerless Grinding on Surface Grinders
Centerless grinding is an essential machining process widely used in manufacturing to produce highly precise parts. When integrated with surface grinders, it offers a multitude of benefits that enhance productivity, efficiency, and the overall quality of finished products. This article explores the dynamics of high-quality centerless grinding on surface grinders, the benefits it offers, and key considerations for achieving optimal results.
Understanding Centerless Grinding
Centerless grinding is a cylindrical grinding process where the workpiece is not supported by centers. Instead, it relies on the contact made between the workpiece, the grinding wheel, and a regulating wheel. This unique setup allows for continuous rotation of the workpiece, which can be fed through the grinding zone at high speeds while maintaining tight tolerances. The ability to grind multiple parts simulataneously makes centerless grinding an economical choice for mass production.
Integration with Surface Grinders
When used together, centerless grinding and surface grinding can significantly improve the machining process. Surface grinders are typically employed to achieve flat surface finishes on components, while centerless grinding focuses on roundness and outer diameter precision. By incorporating centerless grinding techniques into surface grinder operations, manufacturers can streamline their workflows, reduce part handling, and improve accuracy.
Benefits of High-Quality Centerless Grinding
1. Precision and Tolerance Centerless grinding is renowned for its ability to achieve exceptionally tight tolerances. With high-quality machines and proper setup, manufacturers can produce components with tolerances as tight as ±0.0001 inches. This precision is crucial in industries such as aerospace, automotive, and medical devices, where even minor discrepancies can lead to significant performance issues.
2. Efficiency and Speed The process allows for high-speed grinding without sacrificing quality. Parts can be fed into the machine quickly, reducing cycle times. Additionally, multiple parts can be processed simultaneously, maximizing productivity in high-volume manufacturing environments.
3. Cost-Effectiveness With decreased cycle times and the ability to produce high volumes of parts, centerless grinding on surface grinders can lower production costs. The savings generated from reduced labor and faster output can be significant, particularly for manufacturers faced with competitive pricing pressures.
high quality centerless grinding on surface grinder
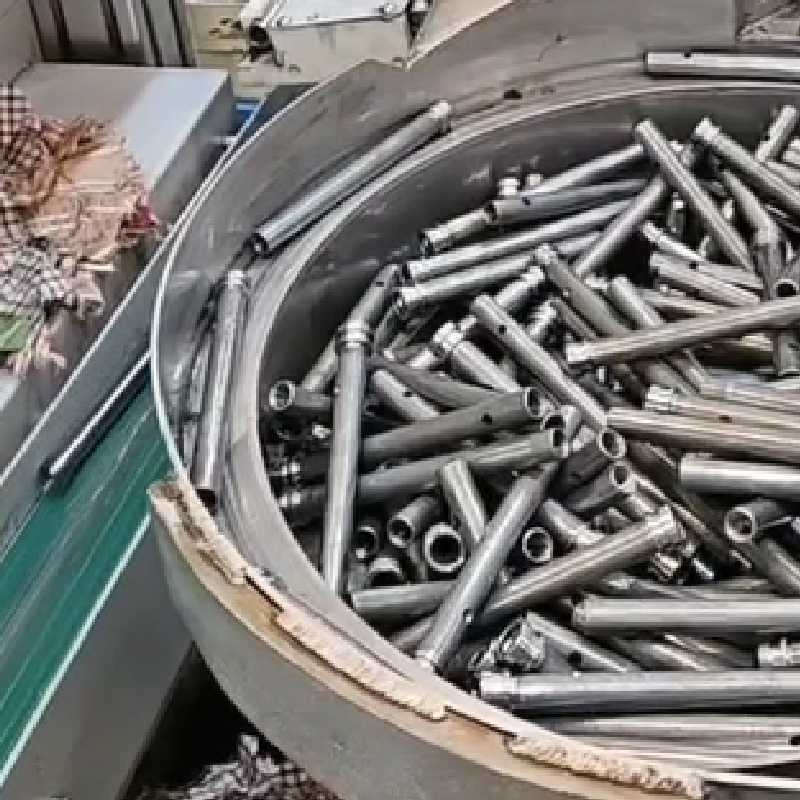
4. Versatility Centerless grinding can be performed on a variety of materials, including metals, plastics, and composites. This versatility makes it suitable for diverse applications across different industries.
5. Improved Surface Finish High-quality centerless grinding enhances the surface finish of components. When combined with the surface grinding process, manufacturers can achieve superior finishes that meet stringent quality standards.
Key Considerations for High-Quality Centerless Grinding
To achieve optimal results through centerless grinding on surface grinders, several factors must be considered
1. Machine Calibration Regular inspections and calibrations are necessary to ensure that both the centerless and surface grinders are operating correctly. This includes checking alignment, wheel dressing, and ensuring proper speeds.
2. Wheel Selection The choice of grinding wheels plays a vital role in the outcome of the grinding process. Selecting the correct abrasive material and wheel hardness based on the workpiece and desired finish is essential.
3. Coolant Usage Proper coolant application is critical to managing heat and minimizing wear on both the grinding wheel and the workpiece. This helps maintain surface integrity and prolongs wheel life.
4. Operator Skill Skilled operators are essential for successful centerless grinding operations. Training personnel to understand the nuances of setup, operation, and troubleshooting can dramatically impact the quality of the output.
Conclusion
High-quality centerless grinding, particularly when integrated with surface grinding technologies, is a powerful tool for manufacturers seeking precision and efficiency. The precision, speed, versatility, and cost-effectiveness of this process make it an attractive option in today’s competitive manufacturing landscape. By focusing on proper machine calibration, wheel selection, and operator training, businesses can harness the full potential of centerless grinding to enhance product quality and streamline production processes.