In today's industrial landscape, the role of flat surface polishing machines is indispensable for industries ranging from metalworking to electronics manufacturing. These machines streamline the finishing processes, ensuring components meet rigorous standards of smoothness and reflectivity. Maintaining these machines necessitates a robust service strategy that elevates their performance and prolongs their lifespan. This article delves into the comprehensive service requirements for flat surface polishing machines, discussing experience-based insights, expertise-driven techniques, and authoritative recommendations to establish trustworthiness.
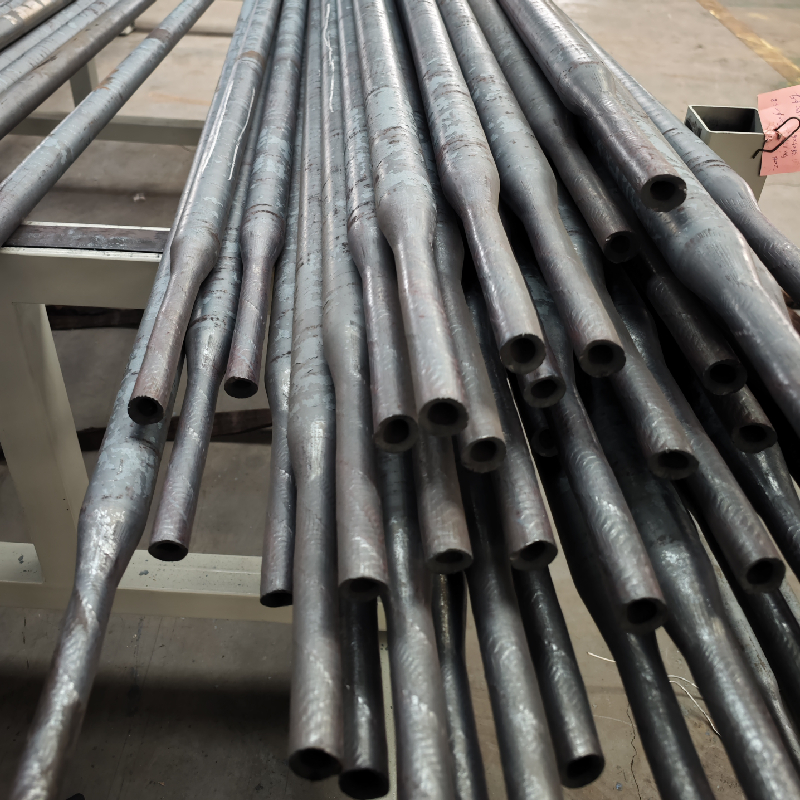
The first aspect to consider is understanding the intricacies of flat surface polishing machines. Unlike general honing devices, these precision tools are engineered for specific tasks, such as mirror-finishing or achieving ultra-low surface roughness. As a professional servicing these machines, it’s crucial to have an in-depth knowledge of their components, such as polishing heads, abrasive belts or wheels, coolant systems, and automation controls. Expertise in these elements allows for accurate diagnostics and tailored solutions that enhance machine performance.
Routine maintenance is a key component of any service strategy. This involves scheduled inspections of all moving parts and consumables. Worn-out components like bearings, seals, and abrasive materials should be replaced proactively. An experienced technician knows that neglecting even minor wear can lead to significant inefficiencies and costly downtimes. Implementing a preventative maintenance plan not only reduces breakdowns but also extends operational longevity. This expertise, when shared with machine operators and maintenance staff through training, can empower the workforce to identify potential issues before they escalate.
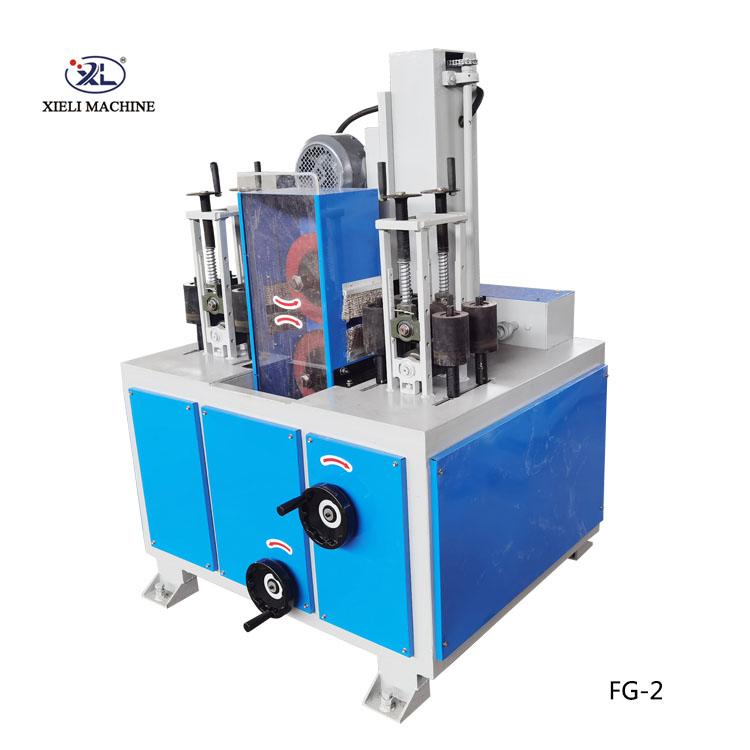
The coolant system, often overlooked in routine checks, plays a vital role in preventing overheating and ensuring the quality of the polish. It’s critical to use manufacturer-recommended coolants and regularly clean the system to avoid clogs and contamination. A service professional with authoritative knowledge recognizes the balance necessary between coolant concentration and water, adjusting it according to the materials being processed to achieve optimal cooling performance.
Furthermore, upgrading software and control systems can be beneficial. Machines may come with integrated software that requires periodic updates to improve functionality and security. Expert service providers should stay abreast of technological advancements and advise clients on software upgrades or retrofits that can amplify productivity and precision.
flat surface polishing machine service
Trustworthiness in the servicing of flat surface polishing machines is built on transparency and certification. Technicians and service companies should hold relevant certifications that attest to their capability and adherence to industry standards. Providing clear and detailed service reports also instills confidence in the client. These reports should cover all aspects of the service, from diagnostic findings and corrective actions to future maintenance recommendations.
Establishing a collaborative relationship with machine manufacturers can greatly enhance service effectiveness. Engaging in ongoing training sessions, attending manufacturer workshops, and participating in industry forums positions a service provider as a trusted leader. This collaborative expertise ensures that even the most challenging issues are resolved quickly and efficiently, reinforcing the service provider’s reputation.
Finally, user feedback should be an integral component of a service plan. Encouraging clients to share their experiences and suggestions after service not only fosters trust but also provides invaluable insights for continuous improvement. A service-oriented approach that actively listens to clients and incorporates their feedback can significantly elevate the service quality of flat surface polishing machines.
In conclusion, providing exemplary service for flat surface polishing machines requires a holistic approach that encompasses technical expertise, routine maintenance, coolant management, software upgrades, transparency, and industry collaboration. By prioritizing these components, service providers not only ensure a higher level of machine performance but also strengthen their reputation as reliable, expert partners in the field. Embracing a strategy built on experience, expertise, authoritativeness, and trustworthiness will inevitably lead to long-term success and client satisfaction.
For More Details Pls Contact Us
Fiberglass Reinforced Plastic (FRP), also known as fiber-reinforced plastic, is a composite material widely used across various industries.