The Evolution and Significance of Famous Pipe End Grinding Machines
In the world of metalworking and fabrication, precision holds paramount importance. Among the various processes involved, pipe end grinding plays a crucial role, particularly when it comes to finalizing the quality of cylindrical pipes used across industries ranging from construction to automotive. As technology has evolved, so have the machines designed to deliver accurate and efficient pipe end grinding. This article delves into the significance and advancement of famous pipe end grinding machines.
Understanding Pipe End Grinding
Pipe end grinding is the process of refining the ends of pipes to achieve a smooth and level surface. This operation ensures that pipes can be easily joined with other sections through welding or bolting without compromising structural integrity. Properly ground pipe ends not only enhance the aesthetic appeal but also contribute to the longevity and performance of the welded joints. The demand for uniformity and quality necessitates the use of specialized machines.
The Rise of Pipe End Grinding Machines
Historically, pipe grinding was a tedious and labor-intensive task that required manual intervention. Workers used rudimentary tools to grind and smoothen the edges, a process that could be inconsistent and time-consuming. However, as industries expanded and the need for precision increased, manufacturers sought mechanical solutions to improve efficiency and accuracy. This led to the development of pipe end grinding machines.
Famous manufacturers have since emerged in this niche, consistently pushing technological boundaries. These machines vary in complexity from basic portable grinders to advanced fully automated systems. Their designs incorporate innovative features such as adjustable speed controls, multiple grinding heads, and computer numeric control (CNC) programming, which allows for greater precision and repeatability.
Key Features of Leading Pipe End Grinding Machines
1. Versatility and Adaptability Modern machines can grind pipes of various materials, including steel, stainless steel, and even alloys. They are also designed to handle different diameter sizes, making them suitable for various applications.
famous pipe end grinding machine
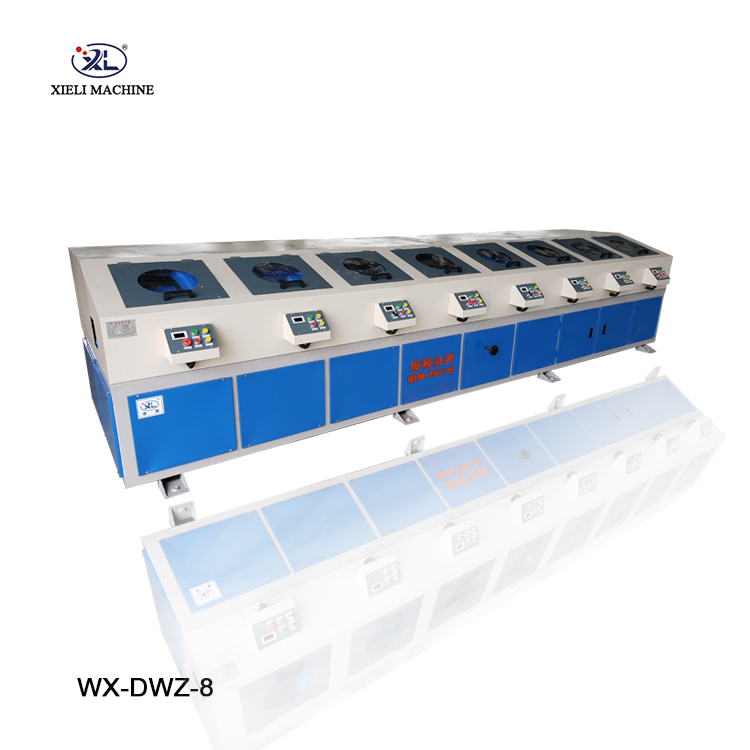
2. Efficiency Automated pipe end grinding machines significantly reduce the time taken to finish a batch of pipes compared to manual labor. This efficiency not only speeds up production but also minimizes labor costs.
3. Enhance Surface Quality High-end machines often come equipped with advanced grinding wheels and techniques that can polish the pipe ends to achieve a mirror-like finish. This enhances not just the aesthetics but also minimizes corrosion and wear over time.
4. Safety Features Safety is a vital concern in any manufacturing process. Contemporary machines are designed with safety features that protect operators from accidents, such as automatic shut-off systems and protective enclosures.
The Future of Pipe End Grinding Technology
As we move further into the era of Industry 4.0, the future of pipe end grinding technology looks promising. The integration of Artificial Intelligence (AI) and IoT (Internet of Things) into machinery is expected to revolutionize the way pipe end grinding is performed. Predictive maintenance powered by AI can foresee potential machine failures, making operations smoother and reducing downtime.
Moreover, industries are leaning towards eco-friendly production methods. Future pipe end grinding machines are expected to incorporate energy-efficient systems and dust collection technologies that minimize environmental impact.
Conclusion
The importance of famous pipe end grinding machines in the manufacturing sector cannot be overstated. They play a critical role in ensuring the quality and durability of pipes, ultimately affecting the performance of countless structures and systems. As technology advances, these machines will continue to evolve, offering greater efficiency, precision, and sustainability. The ongoing innovation in pipe end grinding technology not only signifies the progress in the manufacturing domain but also underlines the commitment to quality in every finished product. As industries continue to expand and demand rises, the significance of these machines will only grow, shaping the future of metal fabrication.