The Inner Wall Polishing Machine Revolutionizing the Finish of Cylindrical Surfaces
In today's manufacturing landscape, precision and quality are paramount, particularly in the production of cylindrical components used in various industries, including automotive, aerospace, and construction. The inner wall polishing machine stands out as a game-changer in this domain, providing manufacturers with the ability to achieve flawless finishes on the inner surfaces of pipes, tubes, and other round components.
Understanding Inner Wall Polishing Machines
An inner wall polishing machine is specially designed to process the internal surfaces of cylindrical objects. These machines use advanced polishing techniques to remove imperfections, burrs, and surface roughness while enhancing the overall aesthetic quality of the product. The innovative technology harnessed in these machines includes both mechanical and automated processes, which contribute to a more efficient and consistent output.
The polishing process typically involves several steps. First, workpieces are secured in the machine, ensuring that they remain stable during the polishing operation. Next, polishing tools, often made from materials like silicone, cloth, or specialized compounds, are employed to smooth out the inner walls through a combination of rotation and oscillation. The process generates fine dust, which is usually extracted via a dust collection system, keeping the work environment clean and safe.
Key Benefits of Using an Inner Wall Polishing Machine
1. Enhanced Surface Finish The primary advantage of using an inner wall polishing machine is the refined surface finish it provides. By eliminating surface irregularities, manufacturers can produce components that not only look appealing but also meet strict industry standards for performance.
2. Increased Durability Polished surfaces have a lower likelihood of corrosion and wear. By refining the inner walls of components, these machines contribute to the longevity of the products, reducing maintenance costs and increasing customer satisfaction.
famous inner wall polishing machine
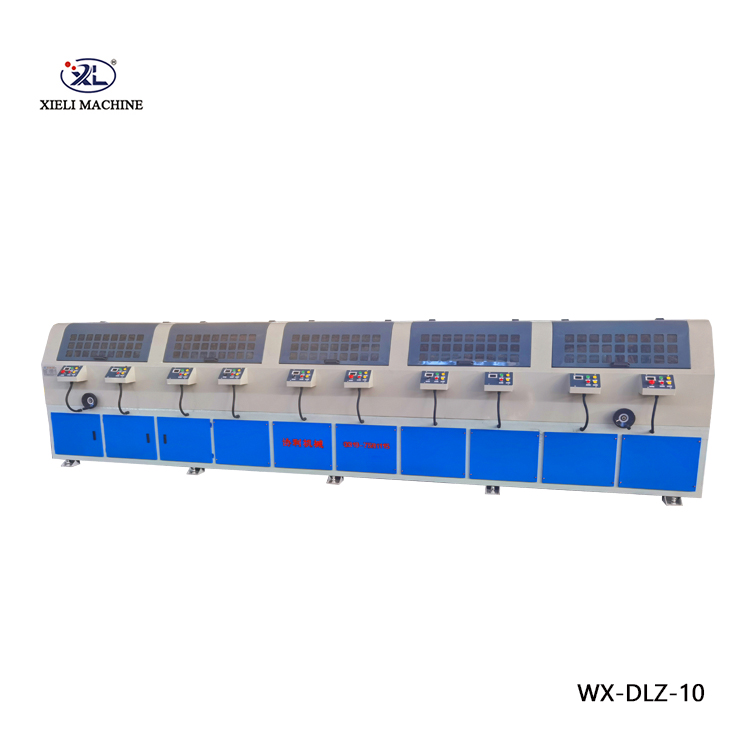
3. Improved Performance In industries where fluid dynamics play a crucial role (such as in piping systems), a smoother surface can greatly impact flow rates and pressure drops. By utilizing an inner wall polishing machine, manufacturers can enhance the operational efficiency of their products.
4. Versatility Modern inner wall polishing machines are capable of accommodating a wide range of materials and dimensions. Whether dealing with stainless steel, aluminum, or other alloys, these machines can be adjusted to meet varying specifications, making them a valuable asset across different manufacturing sectors.
Technological Advancements
Recent advancements in technology have further enhanced the efficiency and effectiveness of inner wall polishing machines. The integration of computer numerical control (CNC) allows for precise control over the polishing process, minimizing human error and ensuring consistent quality. Additionally, programmable automation enables manufacturers to handle multiple batches of differing dimensions without significant downtime, optimizing production workflows.
Moreover, the implementation of smart technology, such as IoT connectivity, allows for real-time monitoring of machine performance. Operators can receive immediate feedback on the polishing process, making adjustments as necessary to achieve desired results. This not only improves product quality but also contributes to more sustainable manufacturing practices by reducing waste and energy consumption.
Conclusion
The inner wall polishing machine represents a vital element in modern manufacturing, significantly improving the quality and functionality of cylindrical components. As industries continue to push for higher standards and better efficiencies, the demand for such advanced machinery will only grow. By investing in innovative polishing solutions, manufacturers can stay competitive, produce superior products, and ultimately meet the evolving needs of their customers. Embracing this technology is not just a step towards improved quality, but a leap towards the future of manufacturing excellence.