Understanding the Costs of Famous Centerless Grinders
When it comes to precision machining, centerless grinders stand out for their efficiency and capability in producing high-quality rounded components. Whether you are a small machine shop looking to expand your capabilities or a large manufacturing facility aiming for mass production, investing in a centerless grinder can be a significant decision. One of the primary factors that influence this decision is the cost associated with these machines.
Types of Centerless Grinders and Their Costs
The cost of centerless grinders varies widely based on several factors, including the type of machine, its features, and brand reputation. Generally, there are two main types of centerless grinders in-feed and through-feed.
1. In-Feed Centerless Grinders These are suited for parts with complex shapes or features. They typically have a higher price point due to their specialized design and advanced features. Prices for these machines can range from $50,000 to over $100,000, depending on the manufacturer and the customization options available.
2. Through-Feed Centerless Grinders Ideal for simpler, cylindrical parts that can be fed through the machine continuously. These are generally more affordable, with prices starting around $30,000 and going up to $70,000. The simplicity of their operation and design makes them a popular choice for high-volume production runs.
Factors Impacting Costs
Several factors can influence the cost of centerless grinders beyond just the type of machine. Here are a few key considerations
famous centerless grinder cost
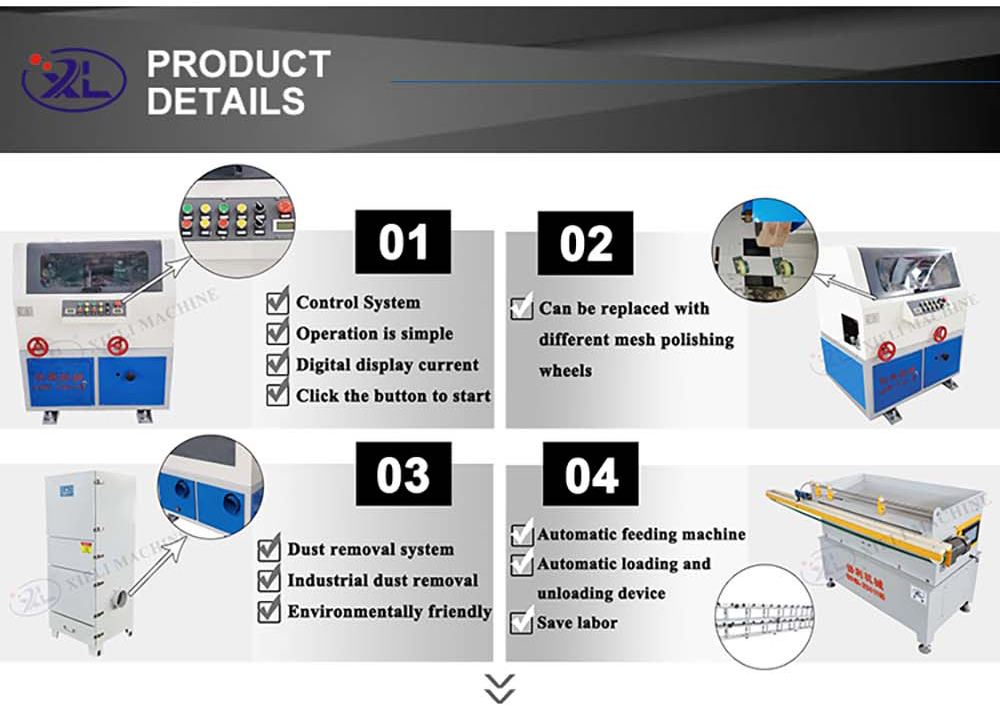
- Brand Reputation Renowned brands known for their reliability and advanced technology, such as Cincinnati, Royal Master, and Glebar, often come with a premium price tag. However, investing in a reputable brand can mean better support, longevity, and machine precision.
- Specifications and Features High precision, automation capability, and additional features such as computer numerical control (CNC) integration can significantly drive up costs. CNC centerless grinders can range from $100,000 to $300,000, or even higher, based on their capabilities.
- Condition of the Machine New machines will always come at a higher cost. However, used or refurbished machines can offer significant savings, ranging from $10,000 to $50,000 depending on age, condition, and previous application.
- Maintenance and Operational Costs While the initial investment is an essential aspect, understanding the operating costs, including maintenance, labor, and tooling, is equally important. Regular maintenance ensures longevity and efficiency, while training staff can also incur additional costs.
Conclusion
In summary, the investment in centerless grinders is substantial but can lead to improved production efficiency and part quality. With prices ranging widely from $10,000 for used models to over $300,000 for advanced CNC options, it’s crucial for businesses to assess their specific needs and applications.
Before making a purchase, it’s advisable to conduct thorough research, seek consultations from manufacturers, and evaluate the total lifecycle cost of ownership. By carefully weighing the benefits against the investment, businesses can make informed decisions that align with their financial and operational goals. Whether for precision hone tooling, automotive parts, or any other application, understanding the cost dimensions of centerless grinders is vital for strategic planning and growth in the manufacturing sector.