Understanding the Purchase of Filmatic for Centerless Grinder Machines
In the world of precision machining, centerless grinding is known for its efficiency and ability to produce high-quality cylindrical components. However, to maximize the potential of a centerless grinder machine, accessories and attachments play a crucial role. One such accessory that has gained attention in recent years is Filmatic, a system designed to enhance the grinding process. This article explores the importance of Filmatic for centerless grinder machines and why investing in it can be beneficial for manufacturers.
The Role of Filmatic in Centerless Grinding
Flimatic refers to a specialized film or coating technology designed to improve the grinding wheels used in centerless grinding machines. This coating can significantly reduce friction during the grinding process, leading to a finer finish and longer tool life. The application of Filmatic minimizes the heat generated during grinding, which is a common issue that can lead to material distortion and affect the dimensional accuracy of the workpiece.
Centerless grinding is characterized by its ability to process multiple parts at high speeds with consistent results. However, the choice of grinding wheel and its maintenance are critical to the success of this machining process. By utilizing Filmatic, manufacturers can achieve better performance from their machines, ultimately translating to enhanced productivity and profitability.
Economic Benefits of Filmatic
Investing in Filmatic for centerless grinder machines can deliver significant economic advantages. The reduction in friction not only prolongs the life of the grinding wheel but also requires less frequent replacements. This leads to lower operational costs over time, as manufacturers can avoid frequent downtime for wheel changes and associated maintenance.
buy filmatic for centerless grinder machine
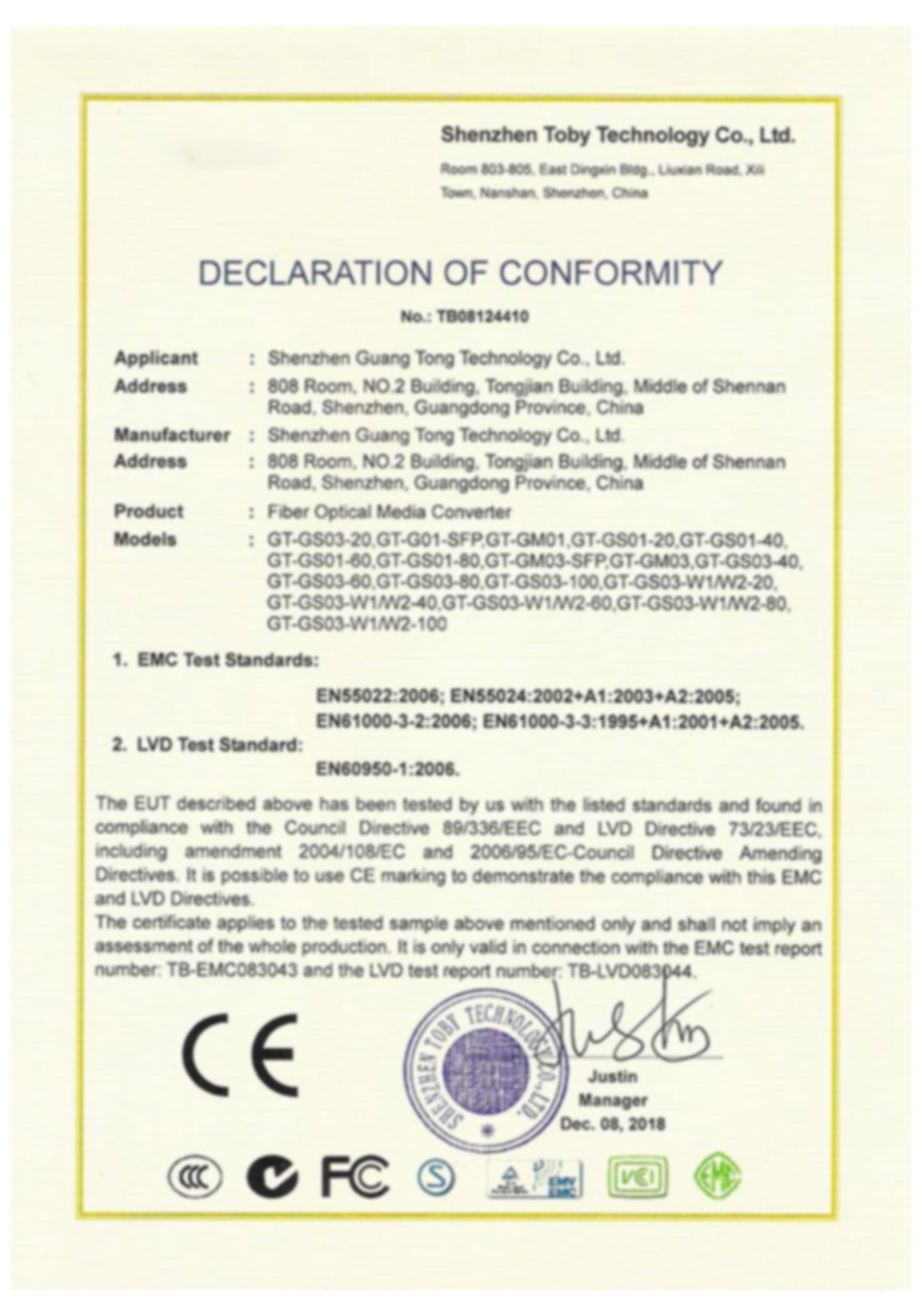
Moreover, the enhanced surface finish provided by Filmatic means that components may require less post-grinding processing, such as polishing or additional machining. This reduction in secondary operations can further decrease production times and labor costs, allowing for a more streamlined manufacturing process.
Environmental Considerations
In today's manufacturing environment, sustainability and environmental responsibility are becoming increasingly important. Filmatic technology can contribute to these goals by reducing the amount of waste generated from frequent tool changes and minimizing the need for excessive coolant usage due to lower heat generation. Consequently, this aligns with corporate initiatives focused on reducing their ecological footprint.
Conclusion
As industries evolve, so do the tools and technologies that aid in manufacturing processes. Filmatic represents an advancement in grinding technology that can significantly benefit manufacturers utilizing centerless grinder machines. Its ability to enhance performance, reduce operational costs, and contribute to sustainable practices makes it a wise investment for businesses aiming to remain competitive in a demanding market.
Whether you are a manufacturer seeking consistent quality in your products or looking to optimize your grinding processes, considering the purchase of Filmatic for your centerless grinding machines is a strategic move. By implementing this innovative technology, businesses can ensure they are equipped to meet the challenges of modern machining while benefiting from improved efficiency and reduced costs. In summary, Filmatic is not just an accessory; it is a valuable investment in the future of precision machining.