The Benefits of Engine Centerless Grinders and Their Availability
In the world of manufacturing and precision engineering, the need for high-quality grinding processes cannot be overstated. One machine that stands out in this category is the centerless grinder, particularly those designed for engine components. As industries evolve and the demand for precision grows, the sale and service of engine centerless grinders have become increasingly important. This article will explore the benefits of these machines and delve into the services associated with them.
What is a Centerless Grinder?
A centerless grinder is a type of grinding machine that utilizes a centerless process for grinding metal and other materials. Unlike traditional grinders, where the workpiece is held between two centers, a centerless grinder uses a combination of rollers and a grinding wheel to secure the piece. This design allows for continuous grinding, which can significantly increase productivity and efficiency, making it ideal for mass production.
Advantages of Engine Centerless Grinders
1. Precision and Accuracy One of the primary benefits of using centerless grinders is the level of precision they offer. These machines are capable of producing components with extremely tight tolerances, often within a few microns. This precision is critical in the manufacturing of engine parts, where even the smallest variance can lead to significant performance issues.
2. Increased Production Rates The continuous operation of centerless grinders means that workpieces can be fed into the machine consistently. This allows for a higher throughput compared to conventional grinding, resulting in quicker turnaround times and increased production rates, which are crucial in meeting market demands.
3. Flexibility in Workpiece Sizes Engine centerless grinders are versatile machines capable of handling various sizes and shapes of workpieces. This flexibility allows manufacturers to produce different engine components without the need for extensive machine reconfiguration.
engine centerless grinder for sale service
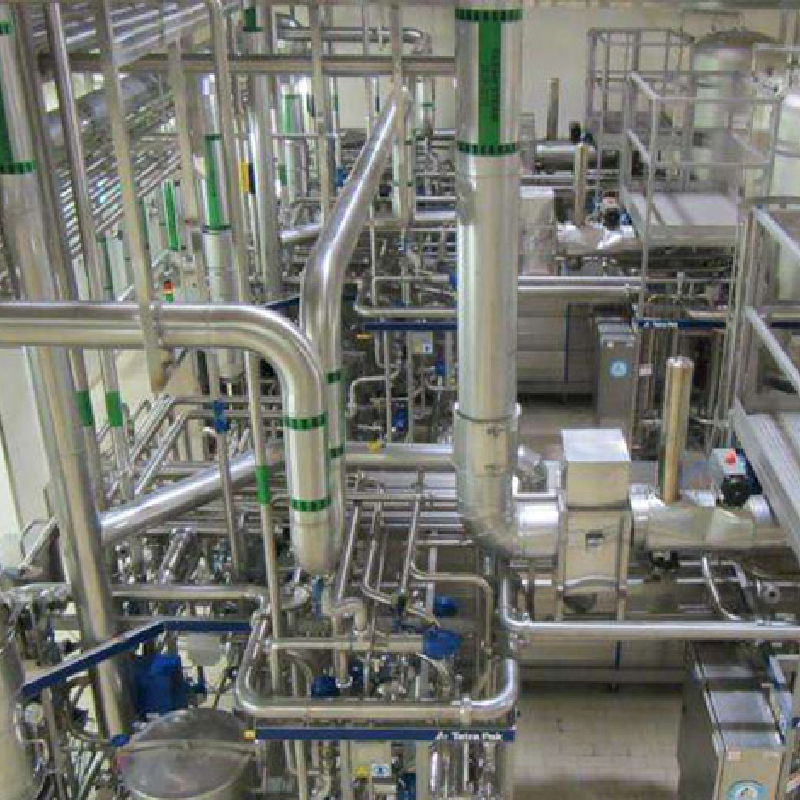
4. Reduced Setup Times Centerless grinding requires fewer adjustments than traditional grinding setups. The absence of centers and chucks speeds up setup times, enabling manufacturers to switch between projects quickly and efficiently.
5. Lower Cost of Ownership While the initial investment in a centerless grinder can be significant, the long-term benefits often outweigh the costs. The durability and reliability of these machines lead to lower maintenance requirements and operational costs, making them a cost-effective solution for many manufacturers.
Availability and Service
With the growing need for engine centerless grinders, several manufacturers and suppliers offer these machines for sale. Buyers can find a range of options, including new and refurbished models, to suit different budgetary constraints. When considering a purchase, it is essential to evaluate the specifications of the grinder to ensure it meets the required standards for your specific applications.
Moreover, the importance of ongoing service and support cannot be ignored. Reliable service providers offer maintenance packages, ensuring that the machines operate at peak performance. Regular servicing helps prevent breakdowns and extends the lifespan of the grinder, protecting your investment.
Conclusion
Engine centerless grinders have become an indispensable tool in modern manufacturing, offering precision, efficiency, and flexibility. As industries continue to require high standards of quality in their engine components, the demand for these grinders and associated services will only grow. Investing in a centerless grinder, along with securing a trusted service provider, is a strategic move for any manufacturer looking to enhance their production capabilities and maintain a competitive edge in the market.