Custom Paragon RC-12 Centerless Grinder Precision in Every Detail
In the realm of precision manufacturing, the demand for advanced machinery has never been higher. Among the notable solutions that stand out is the custom Paragon RC-12 Centerless Grinder. Renowned for its exceptional performance and versatility, this machine has become a staple for industries that require consistent and accurate grinding of cylindrical parts. In this article, we will delve into the features, benefits, and applications of the Paragon RC-12, demonstrating why it is a preferred choice for manufacturers around the globe.
Overview of the Paragon RC-12 Centerless Grinder
The Paragon RC-12 Centerless Grinder is engineered to deliver superior grinding processes while maintaining dimensional accuracy and optimal surface finish. Its design integrates cutting-edge technology and robust construction, making it suitable for a wide range of materials, from steel and aluminum to plastic and composite materials. The grinder’s flexibility allows it to handle parts of various sizes and shapes, making it an indispensable tool for job shops and large-scale manufacturing operations alike.
Key Features
One of the standout features of the Paragon RC-12 is its user-friendly interface. Operators can easily set up parameters, adjust grinding speeds, and monitor machine performance with minimal effort. This ease of use minimizes downtime and facilitates efficient production processes. Additionally, the grinder features an adjustable infeed system that allows for precise control over the material removal rate, further enhancing its adaptability to different applications.
Furthermore, the RC-12 utilizes a high-precision grinding wheel that is specifically designed to achieve superior surface finishes. This grinding wheel is complemented by a powerful spindle motor, which ensures consistent performance even during prolonged use. The result is a machine that not only meets but exceeds the stringent standards set by various industries.
Another significant aspect of the RC-12 is its built-in coolant system. By providing effective cooling during the grinding process, it helps to prolong the lifespan of both the grinding wheel and the workpiece. The system also aids in reducing the thermal deformation of materials, ensuring that the integrity of the workpiece is maintained throughout the grinding process.
custom paragon rc-12 centerless grinder
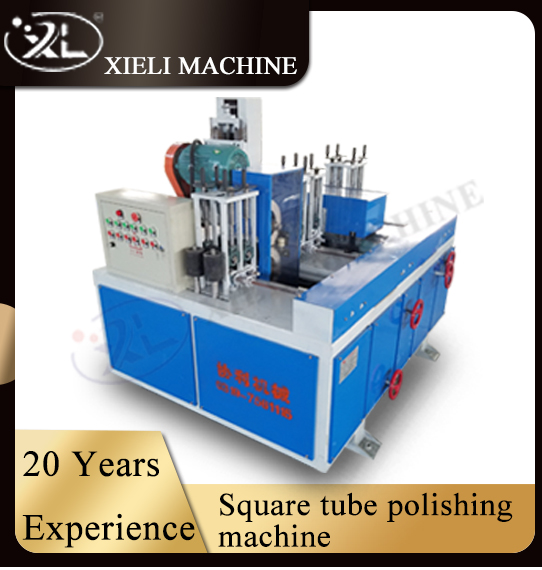
Benefits of Using the RC-12
The advantages of using the Paragon RC-12 Centerless Grinder are numerous. First and foremost, it enhances productivity. The machine's high-speed capabilities allow for rapid processing of parts, which is crucial in industries that operate under tight deadlines. Additionally, the precision achieved by the RC-12 significantly reduces the likelihood of material wastage, leading to cost savings over time.
Moreover, the grinder’s adaptability to accommodate various materials and sizes makes it a valuable asset for manufacturers looking to diversify their production offerings. Whether grinding rods, tubes, or intricate components, the RC-12 provides the versatility needed to meet customer specifications effectively.
Applications Across Industries
The Paragon RC-12 Centerless Grinder finds applications in a wide range of industries, including automotive, aerospace, medical devices, and consumer goods. In the automotive sector, for instance, it is utilized for producing components such as valve stems, crankshafts, and camshafts, where precision and durability are paramount. In the aerospace industry, the RC-12 is employed to grind parts that require exact dimensions and exceptional surface finishes, ensuring the safety and performance of aircraft.
On the medical front, the reliability of the RC-12 is crucial for manufacturing surgical instruments and implants that must adhere to stringent regulatory standards. Its ability to handle intricate designs and maintain tight tolerances makes it an invaluable resource in medical manufacturing.
Conclusion
In conclusion, the custom Paragon RC-12 Centerless Grinder represents a perfect fusion of precision, performance, and versatility. Its advanced features and user-friendly operation not only enhance productivity but also ensure a high level of accuracy and quality in the grinding process. As industries continue to evolve and demand higher standards, machines like the RC-12 will undoubtedly play a critical role in the future of manufacturing, providing the essential capabilities needed to thrive in a competitive market.