The Custom Centerless Finish Grinder Elevating Precision in Manufacturing
In the world of manufacturing, precision is paramount. Industries that rely on high-quality finishes for components — such as automotive, aerospace, and medical device manufacturing — require machines that can deliver unparalleled accuracy and consistency. Among the various grinding technologies available, centerless grinding stands out as a critical process when it comes to achieving exceptional surface finishes while maintaining tight tolerances. The custom centerless finish grinder is a solution that addresses the specific demands of each application, pushing the boundaries of what is possible in machining.
Understanding Centerless Grinding
Centerless grinding is a method where the workpiece is not held between centers; instead, it rests on a work rest and is supported by a regulating wheel. This design allows for the continuous feeding of material, making it ideal for mass production. The precision provided by centerless grinding makes it suitable for various types of materials, including metals, plastics, and composites.
The process operates with two main wheels the grinding wheel, which removes material from the workpiece, and the regulating wheel, which controls the speed and direction of the workpiece. The relationship between these wheels ensures that the component is ground uniformly while retaining its position. The absence of centering allows for more efficient processing, as multiple components can be ground continuously from the same feed.
The Need for Customization
While standard centerless grinders may work for many applications, the demand for specific features and capabilities has led to the development of custom centerless finish grinders. Customization is crucial for businesses that require tailored solutions to meet unique challenges. Factors such as the size and shape of the workpieces, the material properties, and the desired finish all influence the design and functionality of these machines.
A custom centerless finish grinder can be engineered to accommodate larger or smaller parts, to achieve varying levels of surface roughness, or to integrate additional features such as automated feeding systems or advanced monitoring technologies
. By adapting the grinder to meet specific operational requirements, manufacturers can enhance efficiency and reduce production times, leading to significant cost savings and improved competitiveness.custom centerless finish grinder
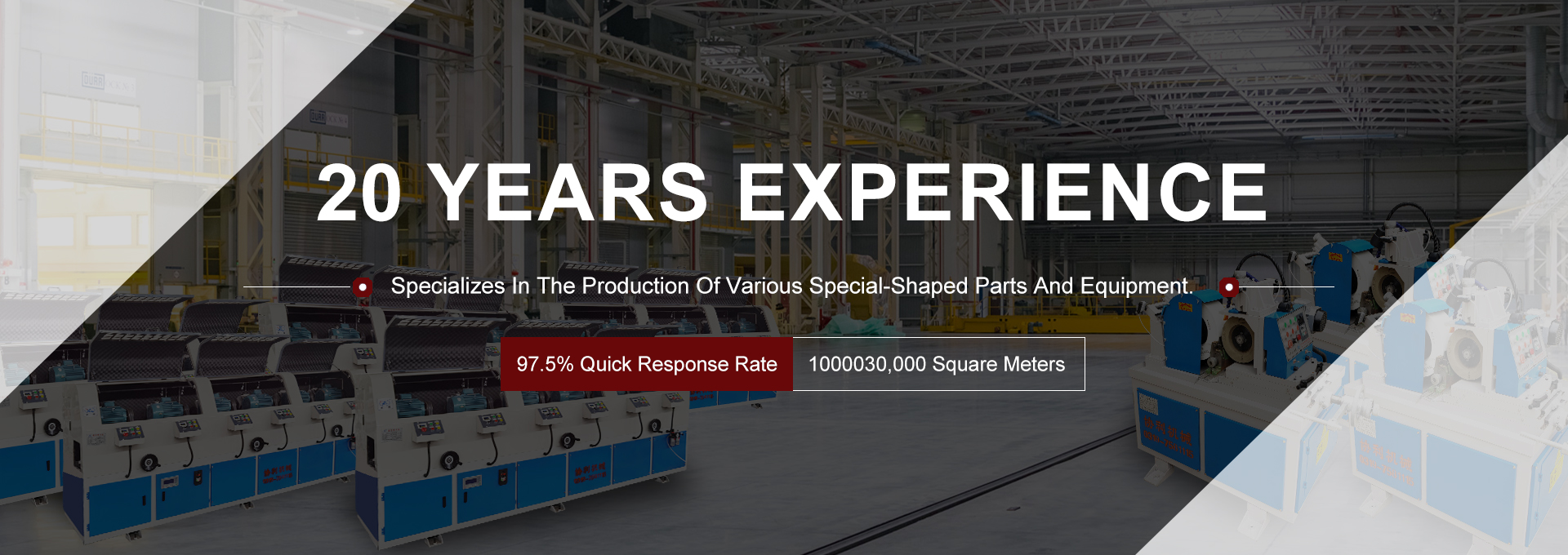
Benefits of Custom Centerless Finish Grinders
1. Enhanced Precision Custom grinders can be designed to provide the exact tolerances and surface finishes required by different industries. This precision directly impacts the performance and reliability of the end products, essential in high-stakes fields like aerospace and medicine.
2. Increased Efficiency Customization can incorporate automation and other cutting-edge technologies, such as predictive maintenance and real-time monitoring. By minimizing human intervention, these advancements significantly reduce operation time and increase throughput.
3. Flexibility and Adaptability As market demands change, manufacturers need machines that can adapt to new materials and processes. Custom centerless finish grinders can be tailored to adapt to varied production needs, ensuring longevity and relevance.
4. Cost-Effectiveness While the initial investment in a custom grinder may be higher compared to off-the-shelf models, the return on investment can be substantial. The efficiency gains, increased production capacity, and reduced waste generated by optimized grinding processes can lead to significant savings over time.
Conclusion
The custom centerless finish grinder is a vital asset for manufacturers seeking to leverage precision and efficiency in their production processes. By understanding the intricate dynamics of centerless grinding and investing in tailored solutions, companies can significantly enhance their operational capabilities. As the manufacturing landscape continues to advance, the role of custom machinery, such as centerless grinders, will become increasingly important, allowing industries to meet the rigorous demands of quality and performance. Embracing innovation in grinding technology is not just an option; it is a necessity for businesses that wish to thrive and maintain a competitive edge in the global market.