The Versatility and Importance of Centerless Grinders in Modern Manufacturing
In the vast world of manufacturing and precision engineering, centerless grinders have emerged as essential tools that contribute significantly to producing high-quality components. Whether it's automotive parts, medical devices, or industrial machinery, the role of a centerless grinder is indispensable. This article will explore the functionality, advantages, and applications of centerless grinders, with insights that anyone in the manufacturing realm might find beneficial.
Understanding Centerless Grinding
At its core, centerless grinding is a highly precise machining process used to create cylindrical parts. Unlike traditional grinding, where the workpiece is supported by centers, centerless grinding utilizes two wheels – a grinding wheel and a regulating wheel. The workpiece is placed between these wheels, allowing it to be ground to exact dimensions without needing any internal or external supports. This unique design not only enhances efficiency but also boosts productivity by enabling continuous operation.
How Centerless Grinders Work
The process begins by feeding the raw material into the grinding area, where it is held in place by the regulating wheel. As the grinding wheel spins, it removes material from the surface of the workpiece. One of the main reasons for the popularity of centerless grinders is their capacity to produce parts with precise diameters and finishes while maintaining tight tolerances.
Furthermore, the setup allows for multiple parts to be processed simultaneously without the need for fixturing, making centerless grinding particularly advantageous for large production runs. This automation and structure drastically reduce setup times, leading to increased efficiency and lower costs for manufacturers.
Advantages of Centerless Grinding
1. High Efficiency The continuous nature of the centerless grinding process means that manufacturers can achieve high output rates. This is particularly useful in situations where large volumes of identical parts are required.
2. Precision and Consistency Centerless grinders can achieve extremely tight tolerances, making them ideal for applications where precision is critical. This capability ensures that components fit seamlessly into larger assemblies without extensive rework.
craigslist.org dedtru centerless grinder product
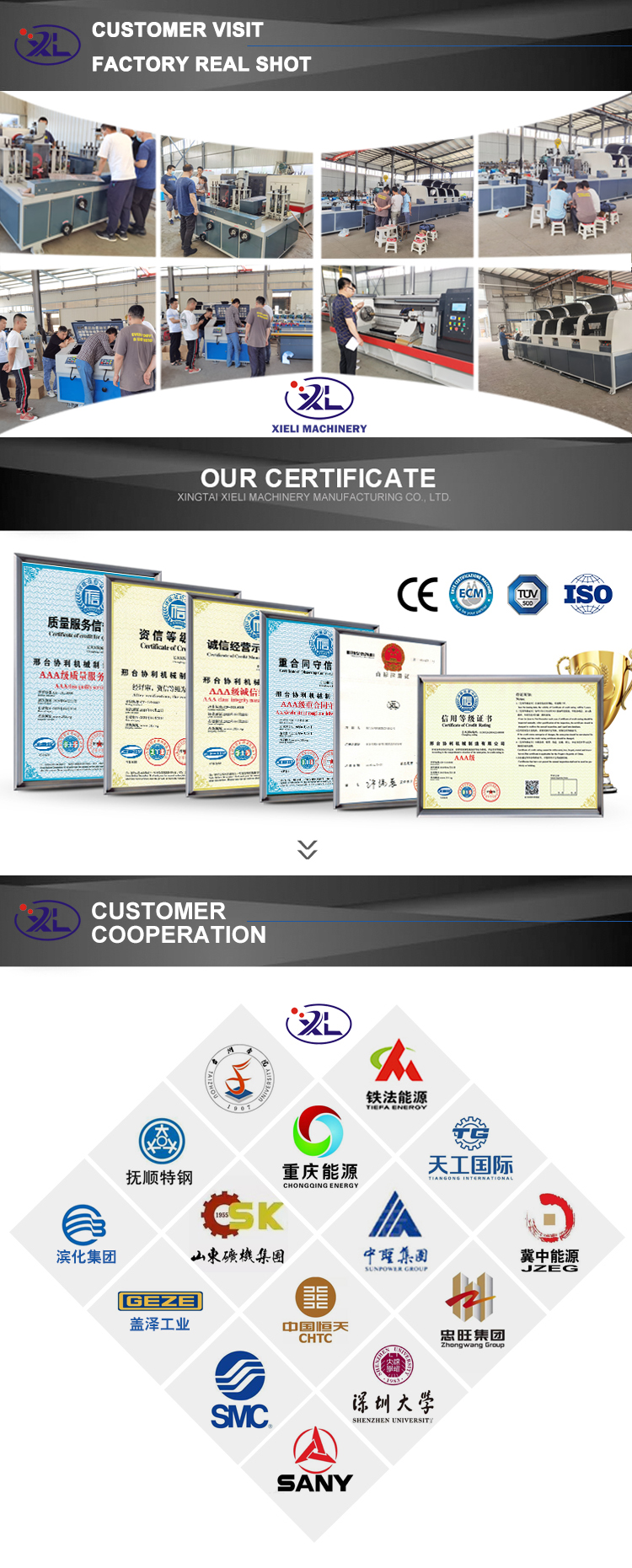
3. Lower Setup Times Since the workpieces do not require elaborate fixturing, setup times are minimized. This factor gives manufacturers the flexibility to switch between products quickly.
4. Versatile Applications Centerless grinders can work on various materials, including metals, plastics, and composites. This versatility makes them valuable in various industries, from aerospace to consumer goods.
5. Reduced Waste By minimizing the amount of material removed during the grinding process, manufacturers can operate more sustainably and reduce waste.
Applications Across Industries
The applications of centerless grinders are vast and varied. In the automotive industry, they are used to produce critical components such as axles, sleeves, and bearing races. The medical industry benefits from centerless grinding when manufacturing devices that demand extreme precision, like surgical instruments and implants.
Furthermore, the aerospace sector relies on the high-speed capabilities of centerless grinders for producing intricate components that must adhere to stringent regulatory standards. The consistent performance and accuracy of these machines are what often separate a reliable supplier from the competition.
Conclusion
In conclusion, centerless grinders play a pivotal role in modern manufacturing processes. Their unique design and operating principles offer substantial advantages, including efficiency, precision, and versatility. As industries continue to evolve and demand greater quality and speed, the importance of centerless grinders will only increase.
For manufacturers looking to enhance their production capabilities while maintaining high standards, investing in quality centerless grinding equipment is a strategic move. As technology continues to advance, these machines will likely incorporate even greater automation and capability, further solidifying their position in the manufacturing industry. Embracing the power of centerless grinding may well be the key to staying competitive in today’s fast-paced market.