The Advancements of CNC Centerless Grinding Machines
In the realm of precision machining, CNC centerless grinding machines have emerged as a pivotal technology, revolutionizing the way components are manufactured and processed
. These remarkable machines utilize computer numerical control (CNC) to automate the grinding process, which enhances efficiency, accuracy, and consistency in producing cylindrical parts that meet stringent tolerances.Centerless grinding is distinct from traditional grinding methods due to its ability to grind without holding the workpiece in a fixed position. Instead, the workpiece is supported by a combination of a grinding wheel and a regulating wheel. This unique setup allows for continuous feeding of materials, making it an ideal process for high-volume production. The CNC integration further enhances the machining capabilities, allowing for intricate designs and precise measurements with minimal human intervention.
One of the primary advantages of CNC centerless grinding machines is their ability to handle various materials and dimensions. Whether it’s steel, aluminum, or composites, these machines can accommodate a wide range of workpiece sizes and shapes. This versatility is particularly beneficial in industries such as automotive, aerospace, and medical device manufacturing, where precision and reliability are paramount. The machines can easily grind parts such as shafts, pins, and tubing to exact specifications, significantly reducing lead times and production costs.
cnc centerless grinding machine product
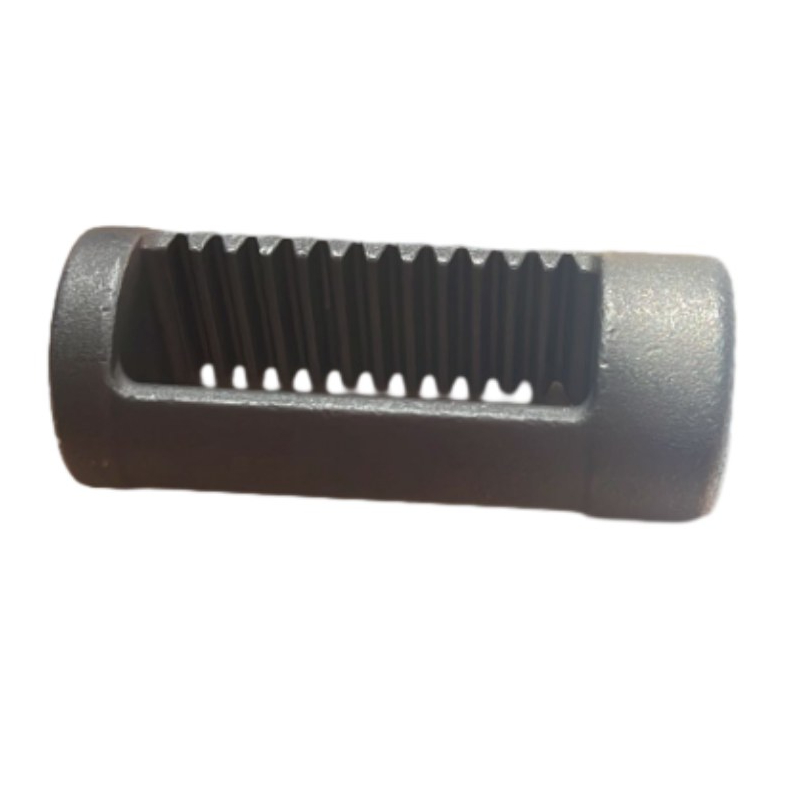
Moreover, the incorporation of CNC technology ensures that the grinding processes can be programmed for repetitive tasks, leading to enhanced productivity. Operators can set up complex grinding cycles and achieve precise results repeatedly with minimal error. The ability to store and recall programs allows manufacturers to shift between different production runs seamlessly, optimizing workflow and reducing downtime.
Safety and operational efficiency are also critical benefits of CNC centerless grinding machines. Advanced features such as automatic tool change, in-process gauging, and real-time monitoring systems enhance the overall safety of the machining process. By reducing manual handling and automating various stages of production, these machines minimize the risk of injuries and ensure a safer working environment for operators.
Furthermore, the precision offered by CNC centerless grinding machines contributes to reduced material waste. By achieving tighter tolerances and superior surface finishes, manufacturers can optimize their material usage and decrease scrap rates. This not only conserves resources but also contributes to more sustainable manufacturing practices.
In conclusion, CNC centerless grinding machines represent a significant leap forward in precision machining technology. Their ability to combine efficiency, versatility, and safety positions them as indispensable tools in modern manufacturing. As industries continue to evolve, the adoption of CNC centerless grinding will likely increase, paving the way for innovations and advancements in component design and production. For manufacturers seeking to enhance their capabilities and maintain competitiveness in the market, investing in these advanced machines is a forward-thinking strategy that promises substantial returns.