The CNC centerless grinding machine stands as a testament to modern engineering, offering unparalleled precision and efficiency for manufacturers across various industries. This sophisticated machinery eliminates the need for centers, bars, or jigs, making it a preferred choice for projects demanding intricate grind work with minimal material waste.

Understanding the fundamentals of CNC centerless grinding is crucial. Unlike traditional grinding methods, centerless grinding places the workpiece between two rotary wheels. The faster-moving grinding wheel removes material from the workpiece, while the slower-moving regulating wheel directs the material through the grinding machine. This method ensures consistent quality, tight tolerance, and exceptional surface finishes, making it indispensable for high-volume production runs.
The precision of CNC centerless grinding machines is unmatched. With advancements in technology, these machines now boast computerized controls that allow for micrometer-level adjustments, ensuring each component meets the exact specifications required. This capability is particularly vital in industries such as aerospace, automotive, and medical devices, where even the smallest deviation can result in significant functional issues.
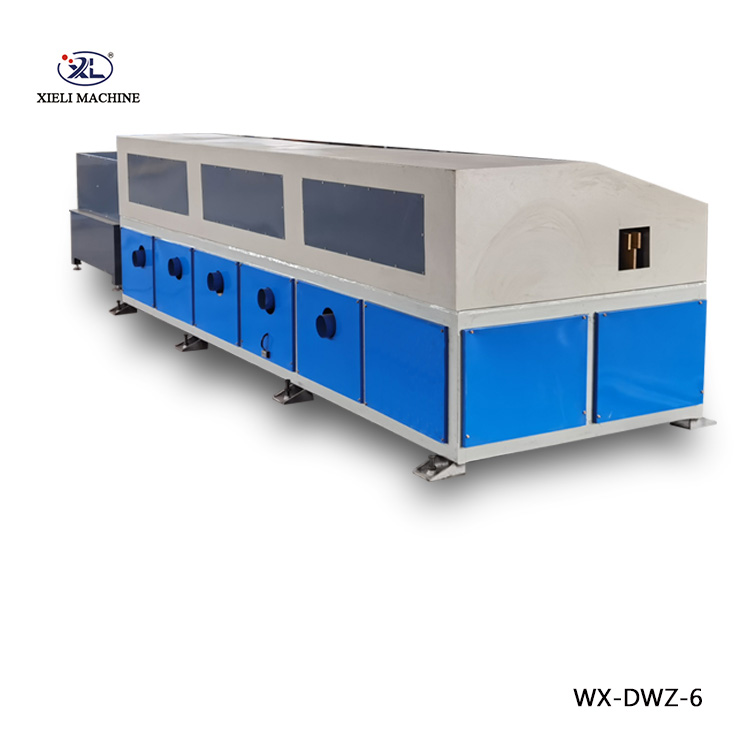
Operators of CNC centerless grinding machines often discuss the reduced setup time as a primary advantage. Unlike conventional grinding methods, these machines do not need fixtures or clamps, which simplifies the preparation process. Improved efficiency is also noted, with many experienced technicians highlighting the machine's ability to perform multiple, simultaneous operations. This multi-functionality not only saves time but also enhances overall productivity.
In terms of expertise, the interface of modern CNC centerless grinding machines has become more user-friendly. While these machines are highly complex, manufacturers have designed the control systems to be intuitive, allowing operators to easily program and adjust machine settings. This ease of use has opened the doors for technicians with different levels of experience to achieve expert-level results, broadening the scope of skilled labor in manufacturing facilities.
cnc centerless grinding machine
When it comes to authoritativeness, CNC centerless grinding machines have set a benchmark for reliability in the manufacturing sector. Leading manufacturers develop their machines with robust materials and incorporate state-of-the-art technologies to ensure longevity and consistent performance. This reputation for durability has made these machines a staple in production environments where continuous and long-term operation is critical.
Trustworthiness is also a key aspect of CNC centerless grinding machines. These machines are designed to operate with minimal manual intervention, reducing the potential for human error and ensuring a higher level of quality assurance. As a result, they are often used to manufacture high-stakes components in sectors such as defense and aviation, where trust in machinery translates directly to safety and performance.
Investing in a CNC centerless grinding machine can transform manufacturing workflows. Businesses experience improvements in precision and efficiency while also enjoying cost savings due to reduced labor and material waste. Manufacturers who have transitioned to this technology often report enhanced competitive advantage, due primarily to faster turnaround times and higher quality outputs.
To ensure optimal performance, regular maintenance of CNC centerless grinding machines is essential. Routine checks and updates to software and hardware components can prevent unplanned downtimes and extend the life of the equipment. This practice underscores the commitment to maintaining trust with clients by continually delivering exceptional products.
In conclusion, the CNC centerless grinding machine exemplifies the pinnacle of manufacturing technology with its experience-driven design, expert-level precision, authoritative reliability, and trustworthy operation. These machines not only revolutionize traditional grinding processes but also establish a new standard for quality and efficiency in modern manufacturing environments.
For More Details Pls Contact Us
Fiberglass Reinforced Plastic (FRP), also known as fiber-reinforced plastic, is a composite material widely used across various industries.