Remanufacturing of Cincinnati Centerless Grinders A Path to Precision and Efficiency
The manufacturing industry has always been at the forefront of technological advancements, constantly evolving to meet the demands of an ever-changing market. Among the various processes that have gained attention, centerless grinding has emerged as a crucial operation in achieving precision and efficiency in manufacturing. When discussing centerless grinders, the name Cincinnati stands out prominently, particularly concerning remanufacturing. This article explores the significance of remanufacturing Cincinnati centerless grinders, highlighting its benefits, processes involved, and its impact on the manufacturing sector.
Understanding Centerless Grinding
Centerless grinding is a modern manufacturing technique that allows for the efficient and precise machining of cylindrical parts without the need for supporting fixtures. This process involves the use of two wheels a grinding wheel and a regulating wheel. The workpiece is fed through the machine, where it is held in place by the regulating wheel while the grinding wheel removes material. This method is particularly advantageous for producing long, slender components with tight tolerances, making it indispensable in several industries, including automotive, aerospace, and general manufacturing.
The Importance of Remanufacturing
Over time, even the most reliable machines can experience wear and tear, leading to decreased performance, precision issues, and increased operational costs. This is where remanufacturing comes into play. Remanufacturing involves restoring machinery to a like-new condition through comprehensive refurbishment processes. The primary aim is to extend the machine's lifecycle while enhancing its performance and reliability.
Benefits of Remanufacturing Cincinnati Centerless Grinders
1. Cost-Effectiveness Remanufactured equipment typically costs significantly less than new machinery. For small to medium-sized enterprises, purchasing new Cincinnati centerless grinders may not be financially feasible. Remanufacturing offers a more affordable solution without sacrificing quality.
2. Enhanced Performance During the remanufacturing process, older machines undergo thorough inspections and upgrades. Components that are no longer efficient are replaced with modern equivalents, resulting in improved performance and precision. This upgrade can also lead to increased production speeds.
3. Sustainability In an era where environmental consciousness is paramount, remanufacturing is a sustainable practice. By reusing existing machinery, manufacturers reduce waste and decrease the demand for new materials. This aligns with global efforts towards sustainability and reducing carbon footprints.
4. Reduced Downtime Remanufacturing often requires less lead time than acquiring new machinery. Companies can quickly restore their existing centerless grinders, minimizing downtime in production and keeping operations running smoothly.
cincinnati centerless grinder remanufacturing supplier
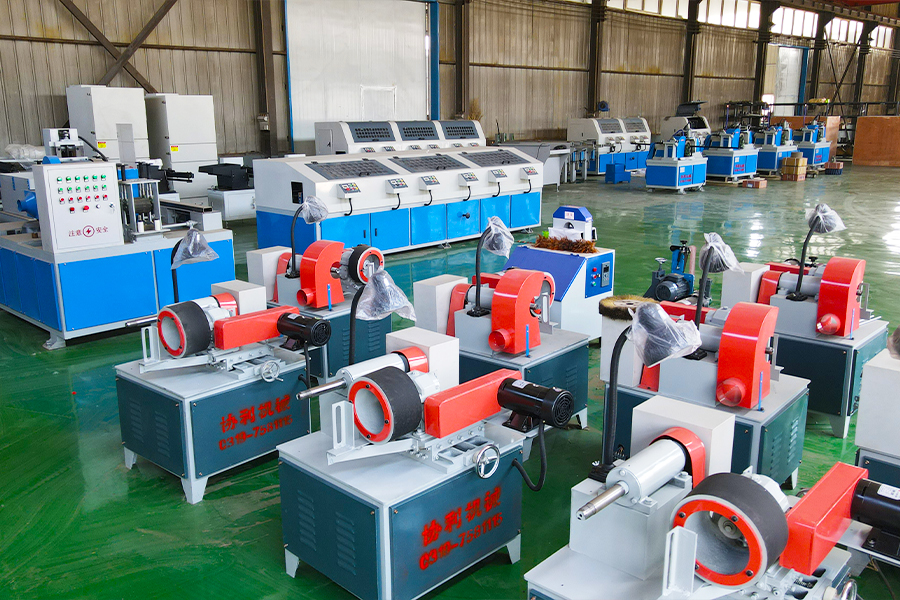
5. Expertise and Customization Specialized remanufacturing suppliers possess extensive knowledge of Cincinnati centerless grinders, ensuring that each machine is restored to meet specific operational requirements. Customization options are often available, allowing businesses to tailor their equipment to their particular needs.
The Remanufacturing Process
The remanufacturing process generally involves several crucial steps
1. Assessment The machine undergoes a thorough inspection to identify worn or damaged components.
2. Disassembly The equipment is carefully disassembled to allow access to internal parts for inspection and replacement.
3. Cleaning All components are cleaned to remove debris, coolants, and other contaminants that may have accumulated over time.
4. Replacement and Repair Worn components are replaced, and repairs are made to any damaged parts. This step may include upgrading certain features to enhance performance.
5. Reassembly and Calibration After all repairs and replacements, the machine is reassembled, calibrated, and tested to ensure it meets original specifications.
6. Final Testing Before returning the equipment to the customer, rigorous testing ensures that the machine operates to the highest standards.
Conclusion
Remanufacturing Cincinnati centerless grinders presents an excellent opportunity for manufacturing businesses to optimize their operations while being cost-effective and sustainable. By opting for remanufactured machinery, companies can enjoy enhanced performance, reduced downtime, and a positive environmental impact. As the manufacturing landscape continues to evolve, embracing remanufacturing practices will undoubtedly play a pivotal role in shaping a more efficient and sustainable future. Investing in remanufactured centerless grinders not only reinforces a company's commitment to quality and precision but also ensures that they remain competitive in an increasingly demanding marketplace.