Understanding Cincinnati Centerless Grinder Parts A Comprehensive Overview
Cincinnati centerless grinders are renowned for their precision and efficiency in the manufacturing industry, particularly in the production of bar stock and precision components. The efficacy of these machines largely hinges on their various parts, which need to be maintained and occasionally replaced to ensure optimal performance. This article delves into the essential components of Cincinnati centerless grinders, shedding light on their functions and importance.
1. The Grinding Wheel
At the heart of any centerless grinder is the grinding wheel. This component is responsible for the actual grinding process, creating the desired surface finish and dimensional accuracy on the workpiece. Typically made from abrasive materials like aluminum oxide or silicon carbide, grinding wheels come in various sizes and grits depending on the application. Regular inspection and replacement are crucial, as a worn or improperly sized wheel can lead to diminished performance and poor quality results.
2. The Regulating Wheel
In a centerless grinding setup, the regulating wheel plays a pivotal role in controlling the speed and rotation of the workpiece. Positioned opposite the grinding wheel, it helps to keep the workpiece in place and ensures a consistent feed rate. The regulating wheel may also wear down over time, and its condition can significantly affect the overall grinding process. Proper alignment and tensioning of this wheel are essential for maintaining optimal grinding conditions.
The work rest support is another essential component, providing stability to the workpiece as it moves through the grinding process. Positioned between the grinding wheel and the regulating wheel, it helps to maintain consistent workpiece height and alignment. The work rest support must be adjustable to accommodate different diameters of workpieces, ensuring versatility in various applications. Regular checks for wear and tear are necessary to prevent any unwanted movement that could affect the grinding accuracy.
cincinnati centerless grinder parts
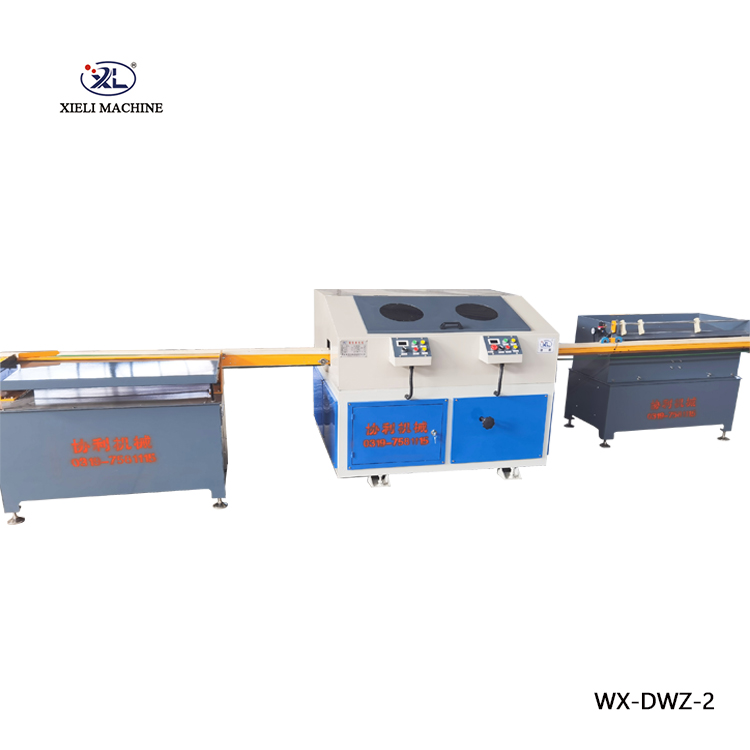
4. Hydraulic and Electrical Systems
Cincinnati centerless grinders frequently utilize hydraulic systems to control the feed rate and other parameters. The hydraulic components, including pumps and cylinders, should be regularly maintained to avoid any leaks or malfunctions that could disrupt the grinding process. Moreover, the electrical system, which powers various functionalities of the grinder, requires routine inspections to ensure all sensors, switches, and motors operate correctly and efficiently.
5. Frame and Structural Components
The structural integrity of the centerless grinder is maintained by its frame and chassis. These components are designed to absorb vibrations during the grinding process, which is crucial for maintaining precision and prolonging the machine's lifespan. Any signs of wear or damage to the frame can adversely affect the machine's performance and should be addressed immediately.
6. Dust and Chip Collection System
To ensure a clean working environment and enhance the machine's performance, an effective dust and chip collection system is vital. This system helps to remove abrasive particles and metal chips generated during the grinding process, preventing them from contaminating the workpiece or causing damage to the machine. Regular maintenance of this system is essential to maintain efficient operation.
Conclusion
In conclusion, the various parts of Cincinnati centerless grinders play critical roles in ensuring the machine operates efficiently and produces high-quality results. Regular maintenance and timely replacement of these components are essential for optimal performance. Understanding each part's function will not only provide insights into the machine's workings but also help operators and technicians to troubleshoot issues and enhance productivity in their manufacturing processes. By taking proper care of these components, businesses can ensure that their centerless grinders remain a valuable asset to their production capabilities.