The Importance of Internal Polishing Machines for Tubes in China
In recent years, the manufacturing sector in China has seen significant advancements, particularly in the production of high-quality tubular products. As industries ranging from aerospace to automotive require materials with superior surface finishes, the role of internal polishing machines for tubes has become increasingly vital. This article explores the importance, functionality, and benefits of internal polishing machines, shedding light on their contribution to enhancing product quality and operational efficiency.
Understanding Internal Polishing Machines
Internal polishing machines are specialized tools designed to improve the surface finish of the inner walls of tubes. They utilize various polishing methods, including abrasive mechanisms, to remove surface imperfections, such as rust, dust, and other contaminants. These machines can effectively smooth rough surfaces, ensuring that the interior of the tubes is polished to a high standard. The outcome is a significant reduction in surface roughness, which directly influences the flow dynamics of fluids within the tubes, ultimately enhancing performance and longevity.
Applications Across Industries
The significance of internal polishing machines spans several industries. In the aerospace sector, tubes must meet strict quality and safety standards. Polished interiors reduce friction, which improves efficiency and reliability in high-pressure environments. In the automotive industry, the performance of fuel and hydraulic lines is directly affected by the smoothness of the inner surfaces. The need for precise manufacturing processes makes internal polishing machines invaluable in ensuring high-quality components.
Moreover, the food and beverage industry also benefits from these machines. Tubes used in food processing must be sanitized and free of contaminants to comply with health regulations. Internal polishing not only enhances the aesthetic appeal but also ensures a hygienic environment, preventing the buildup of bacteria.
Technical Features and Advancements
china tube internal polishing machine
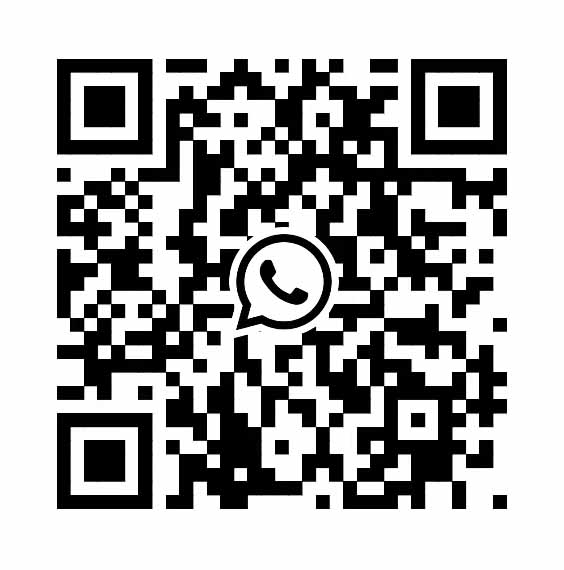
Modern internal polishing machines come equipped with advanced technologies that increase their efficiency and effectiveness. Many of these machines are automated, allowing for precise control over polishing parameters such as pressure, speed, and duration. Automation reduces human error and ensures consistent results across batches.
Additionally, manufacturers are continuously investing in research and development to create machines that can accommodate a wide range of tube sizes and materials. This flexibility is essential for companies that specialize in custom parts. Furthermore, advancements in polishing techniques, such as the use of ceramic or diamond compounds, enable superior finishes without compromising the structural integrity of the tubes.
Economic Benefits
Investing in internal polishing machines can lead to significant economic advantages for manufacturers in China. Enhanced surface finishes can reduce the amount of downtime required for maintenance and improve the lifespan of tubes in various applications, thus lowering long-term costs. A smoother interior means decreased turbulence, which can lead to reduced energy consumption in applications involving fluid transport.
Moreover, products that meet higher quality standards tend to have better market competitiveness. Companies can command higher prices for polished tubes, increasing overall profitability. As globalization intensifies competition, establishing a reputation for quality becomes crucial, and internal polishing is a key factor that can help achieve this goal.
Conclusion
The role of internal polishing machines for tubes in China cannot be overstated. They are critical in ensuring that industries can meet demanding standards for surface finish and performance. As manufacturing processes evolve, the adoption of these machines will continue to grow, leading to improved product quality, operational efficiency, and economic benefits. In a world where precision and quality are paramount, internal polishing machines have firmly established themselves as indispensable tools for manufacturers aiming for excellence in their output. As technology advances, we can only expect these machines to become even more sophisticated, further driving the standards of quality in the manufacturing sector.