The Importance of Tooling in China Centerless Grinders
Centerless grinding is a crucial manufacturing process that allows for precision roundness and surface finish on various cylindrical workpieces. In China, the evolution of centerless grinding technology has paved the way for increased efficiency and productivity in manufacturing industries. However, the success of centerless grinding operations largely hinges on the quality and design of tooling. This article explores the significance of tooling in China centerless grinders, its types, and advancements in technology.
Understanding Centerless Grinding
Centerless grinding differs from traditional grinding methods where the workpiece is held between two centers. In centerless grinding, one wheel is stationary, while another wheel is spinning and positioned at an angle to the workpiece. This setup allows for the continuous feeding of material, which enhances productivity. The absence of a center means that complex geometries can be produced without the need for extensive setups or fixtures.
Types of Tooling in Centerless Grinders
Tooling is critical to achieving optimal grinding results. In the context of centerless grinders, tooling generally refers to the grinding wheels, regulating wheels, and workpieces. Each component plays a vital role in determining the outcome of the grinding process.
1. Grinding Wheels These are the primary cutting tools that remove material from the workpiece. The specification of grinding wheels—size, grit, and bond type—affects the surface finish, dimensional accuracy, and production rate. In China, manufacturers often focus on developing specialized grinding wheels tailored for specific materials and applications to enhance grinding efficiency.
2. Regulating Wheels These wheels serve to control the speed of the workpiece during the grinding process. The balance between the speeds of the grinding and regulating wheels is crucial for achieving effective material removal rates. Regulating wheels can also be customized to suit different workpiece sizes and shapes, ensuring consistent performance.
3. Workpieces The characteristics of the workpieces being processed will influence the tooling requirements. Materials like stainless steel, aluminum, and exotic alloys each have unique behaviors during grinding. Tooling must be designed to accommodate these properties, ensuring optimal results.
Advancements in Tooling Technology
china centerless grinder tooling
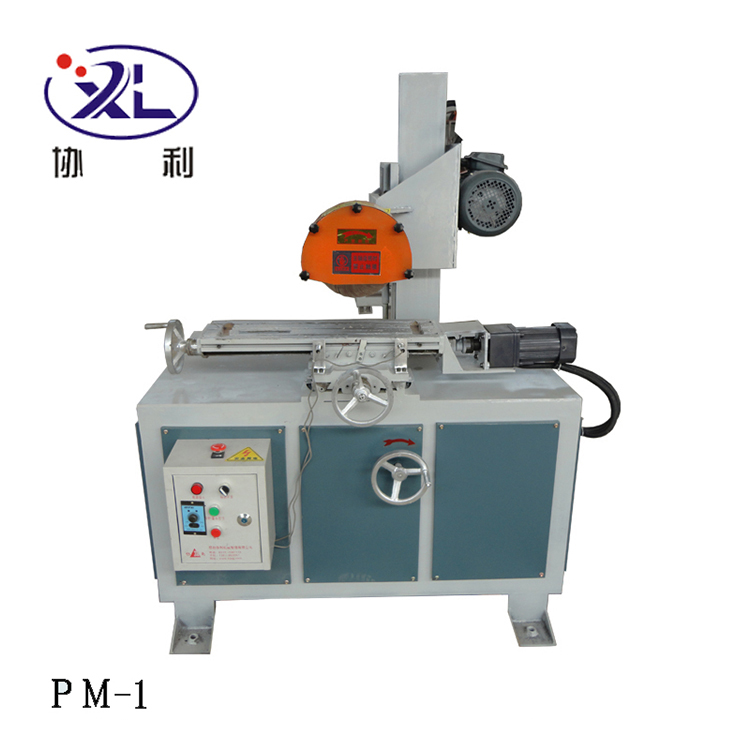
The tooling landscape in China's centerless grinding operations has evolved significantly. Manufacturers are increasingly utilizing advanced materials and technology to enhance the capabilities of their grinding equipment. Some notable advancements include
- CNC Technology The integration of Computer Numerical Control (CNC) systems in centerless grinders has revolutionized the industry by enabling precise adjustments to tooling parameters. CNC systems improve the repeatability of operations and allow for easy modifications, which is especially beneficial for small batch production.
- Diamond and CBN Wheels Superabrasive wheels made from diamond and Cubic Boron Nitride (CBN) have gained popularity due to their high wear resistance and thermal stability. These materials allow for faster grinding speeds and longer tool life, ultimately reducing operational costs in the long run.
- Custom Tooling Solutions Many manufacturers are offering custom tooling solutions that are tailored to meet specific customer requirements. This flexibility is particularly important in a market where diverse applications and materials demand unique tooling configurations. Tailored tooling can significantly improve grinding performance and efficiency.
The Future of Tooling in Centerless Grinding
Looking ahead, the future of tooling in China’s centerless grinding industry appears promising. As manufacturers continue to invest in research and development, we can expect further innovations in grinding wheel formulations, automated tooling systems, and smart technology integration.
Furthermore, the push for sustainability is likely to influence tooling design, leading to the development of eco-friendly materials and processes that minimize waste and energy consumption. Embracing such advancements will not only enhance productivity but also contribute to greener manufacturing practices.
Conclusion
In conclusion, tooling is a fundamental aspect of centerless grinding operations that dictates efficiency and precision. In China, the focus on advanced tooling technologies and customization continues to improve manufacturing capabilities across various sectors. By investing in high-quality tooling and embracing technological advancements, businesses can achieve superior productivity and maintain a competitive edge in the global market. As the industry evolves, the importance of tooling in centerless grinding will remain a critical factor in shaping the future of manufacturing.