The Importance of Centerless Surface Grinders in Precision Manufacturing
In the world of precision manufacturing, achieving the highest levels of accuracy and efficiency is paramount. Among the various tools and machinery that facilitate this goal, centerless surface grinders play a vital role. These machines are designed to grind the outside diameters of objects, delivering excellent surface finish and dimensional accuracy. This article explores the significance of centerless surface grinders, their working principle, and their various applications in modern manufacturing.
Understanding Centerless Surface Grinders
A centerless surface grinder is a type of grinding machine that operates without the need for a workpiece center. Unlike traditional cylindrical grinders, which require the workpiece to be mounted between two centers, centerless grinders hold the workpiece between two rotating wheels the grinding wheel and the regulating wheel. The unique arrangement allows for continuous feeding of the workpiece, making centerless grinding ideal for high-volume production.
The grinding wheel is responsible for removing material from the workpiece, while the regulating wheel controls the speed and position, ensuring that the workpiece is gripped securely. This setup enables the machine to work on multiple parts simultaneously, boosting productivity and minimizing downtime.
Precision and Versatility
One of the key advantages of centerless surface grinders is their ability to achieve exceptional dimensional accuracy. The machine's design eliminates common issues associated with traditional grinding methods, such as variability in support and alignment. This leads to tighter tolerances and improved surface finishes.
Centerless grinders are incredibly versatile and can handle a wide range of materials, including metals, plastics, and ceramics. They are frequently used for grinding cylindrical parts, such as shafts, rods, and pins, making them indispensable in industries like automotive, aerospace, and medical device manufacturing.
centerless surface grinder products
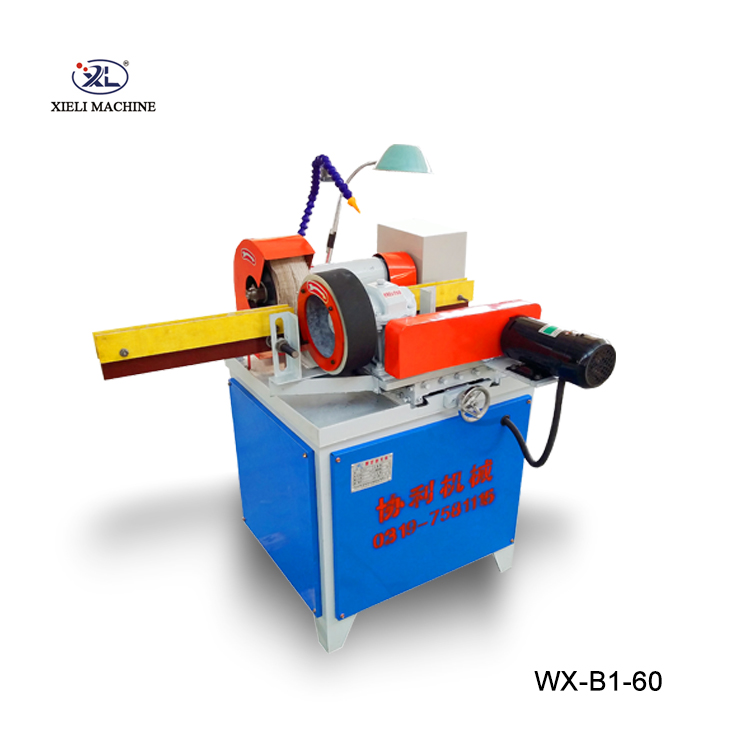
Efficiency in Production
The efficiency of centerless surface grinders is one of their standout features. These machines can operate at high speeds, allowing for rapid material removal while maintaining precision. Additionally, the continuous feed mechanism reduces the time spent on setup and changeover. As a result, manufacturers can produce large quantities of parts with minimal interruption, which is crucial for meeting market demands and maintaining competitiveness.
Furthermore, the automation capability of modern centerless grinders enhances efficiency even further. Programmable logic controllers (PLCs) and other advanced technologies allow manufacturers to set specific parameters and optimize grinding processes, significantly reducing labor costs and human error.
Applications Across Industries
Centerless surface grinders are employed across various industries due to their adaptability and efficiency. In the automotive sector, for instance, they are used to produce precision components such as camshafts, crankshafts, and valve stems. The aerospace industry utilizes these machines for grinding critical engine components that require a high degree of accuracy and surface finish.
Additionally, in the medical field, centerless grinding plays a crucial role in manufacturing surgical instruments and implants, which must adhere to stringent standards for quality and reliability. Beyond these, the technology finds applications in manufacturing tooling, hydraulic components, and electronic parts, among many others.
Conclusion
In conclusion, centerless surface grinders are essential tools in the realm of precision manufacturing. Their unique design, operational efficiency, and versatility make them indispensable in producing high-quality components across various industries. As manufacturing continues to evolve, the importance of such advanced machinery will only increase, ensuring that industries can meet the demands for precision and quality in a competitive marketplace. Investing in centerless surface grinding technology not only boosts productivity but also lays the foundation for continued innovation and excellence in manufacturing practices.