Centerless OD Grinder A Precision Tool for Modern Manufacturing
In the world of manufacturing, the pursuit of precision and efficiency is never-ending. Among the array of tools and machines that facilitate this quest, the centerless OD (outer diameter) grinder stands out as a pivotal piece of equipment. This advanced machinery plays a critical role in shaping and finishing parts with utmost accuracy and minimal human intervention, making it an indispensable tool in various industries.
The Basics of Centerless Grinding
Centerless grinding is a machining process that involves removing material from a workpiece without the need for a centered fixture. Unlike traditional methods where the workpiece is held between two centers, centerless grinding utilizes a unique system of rollers and blades that maintains the position of the workpiece throughout the grinding process. This innovation allows for continuous operation, significantly increasing productivity and throughput.
In a centerless grinder, the workpiece is supported by a lower wheel and a regulating wheel placed above it. The grinding wheel rotates at a high speed, providing the necessary abrasiveness to shape the outer diameter of the workpiece. The regulating wheel is essential as it controls the speed and position, ensuring that the workpiece stays aligned and rotates evenly. This setup not only enhances efficiency but also ensures consistency, resulting in precision-engineered products.
Advantages of Centerless OD Grinding
One of the most significant advantages of centerless OD grinding is its ability to handle large quantities of parts with minimal setup time. Because the workpiece does not need to be individually centered, multiple items can be fed through the machine continuously. This is especially beneficial in high-volume manufacturing environments, where maintaining productivity while ensuring quality is paramount.
centerless od grinder product
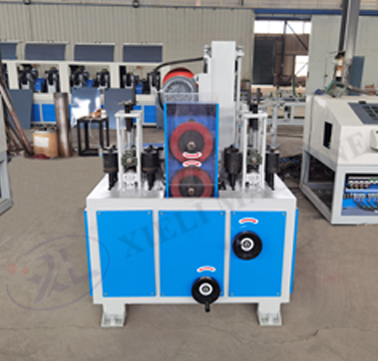
Furthermore, centerless grinding is highly versatile. It can accommodate a wide range of materials, including metals, plastics, and ceramics. Whether working with hard or soft materials, the centerless OD grinder can be adjusted to achieve the desired finish and tolerances, making it suitable for various applications in industries such as automotive, aerospace, medical devices, and more.
Another noteworthy advantage is the machine's capability to produce parts with tight tolerances. Centerless grinding can achieve tolerances as low as ±0.0001 inches, which is vital for components that require a high degree of precision. This level of accuracy is essential in critical applications, such as those found in the aerospace or medical industries, where any deviation could have significant repercussions.
Innovations and Challenges
As manufacturing technology continues to evolve, so too do centerless OD grinders. Modern machines are equipped with sophisticated controls and automation features, providing operators with real-time feedback and data analysis. This not only helps in maintaining the quality of the finished products but also in predicting maintenance needs, thus reducing downtime.
However, centerless OD grinding is not without its challenges. The setup and maintenance of the machine require skilled operators who understand the nuances of the grinding process. Misalignment, incorrect wheel selection, or improper adjustment of the regulating wheel can lead to defects and productivity losses. Therefore, investing in operator training and machine maintenance is equally important to harness the potential of this advanced machining technology fully.
Conclusion
In conclusion, centerless OD grinders are crucial in the realm of precision manufacturing. Their ability to produce high-quality parts efficiently and consistently makes them invaluable in today’s competitive market. As advancements continue in machine technology, the role of centerless grinding will only become more significant, enabling manufacturers to meet the rising demands for quality and efficiency in a rapidly changing industrial landscape. Embracing these machines and their capabilities is not just an option; it is essential for any manufacturing entity aiming for success in the modern age.