Centerless Grinding on Surface Grinder An Overview of Benefits and Suppliers
Centerless grinding is a manufacturing process that can be used effectively in conjunction with surface grinders to achieve precision finishes on cylindrical workpieces. Unlike traditional grinding, where the workpiece is held between two grinding wheels, centerless grinding allows for continuous and efficient processing without the need for fixtures. This approach can significantly enhance productivity, especially for small to medium-sized production runs.
What is Centerless Grinding?
Centerless grinding is a method of removing material from the outside diameter of a workpiece. The workpiece is positioned between a grinding wheel and a regulating wheel, which enables it to spin and advance through the grinding zone. This unique setup allows for high-speed processing and reduces the risk of the workpiece becoming misaligned or deformed during grinding. This method proves advantageous in achieving tighter tolerances and superior finishes, making it a preferred technique in many manufacturing industries.
The Role of Surface Grinders
Surface grinders are machines used specifically for finishing flat surfaces. However, they can also accommodate various attachments and modifications that allow for centerless grinding operations. By utilizing a surface grinder for centerless tasks, manufacturers can benefit from the versatility of the machine while still ensuring high-precision results. Adaptability is one of the key reasons surface grinders remain popular in machine shops.
Benefits of Centerless Grinding on Surface Grinders
1. Increased Efficiency Centerless grinding significantly speeds up production times compared to traditional methods. As workpieces can be fed continuously into the grinder, manufacturers can process large quantities faster, ultimately improving turnaround times for clients.
2. Enhanced Precision With the ability to achieve tight tolerances, centerless grinding provides superior precision for components such as shafts, rods, and pins. This precision is critical in industries like aerospace, automotive, and medical equipment manufacturing.
3. Cost-Effectiveness Utilizing surface grinders for centerless grinding can save on equipment costs. Instead of investing in separate machines for different processes, manufacturers can leverage existing machinery to perform multiple tasks, optimizing resource allocation.
4. Minimal Setup Time Centerless grinding setups require less time than traditional grinding fixtures. The simplicity of the arrangement allows for quick adjustments, letting operators switch seamlessly between different workpieces.
centerless grinding on surface grinder supplier
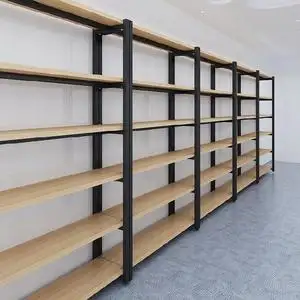
5. Better Surface Finish The continuous nature of the centerless grind minimizes the risk of marks or discontinuities on the workpiece surface. This leads to better finishes that often require less post-processing.
Choosing the Right Supplier
When considering centerless grinding on surface grinders, selecting the right supplier is crucial. An ideal supplier not only provides high-quality machines but also offers technical support and maintenance. Look for suppliers with a solid reputation and experience in the industry. Recommendations and reviews from other manufacturers can also guide your decision.
Some factors to consider while choosing a supplier include
- Quality of Machines Ensure that the surface grinders and peripherals are made using high-quality materials for durability and performance.
- Customization Options Different manufacturing processes may require specific grinding attachments and configurations. A supplier that offers customization options can help you meet unique production needs.
- After-Sales Support Reliable customer service and technical assistance can make a significant difference in machine uptime and productivity.
- Training and Resources Training programs for your operators can enhance their efficiency and ensure the proper usage of the equipment.
Conclusion
Centerless grinding, especially when integrated with surface grinders, presents an array of benefits for manufacturers looking to improve efficiency, precision, and cost-effectiveness. The right supplier is essential for maximizing these benefits, ensuring that businesses not only invest in quality equipment but also gain a robust support system to enhance their grinding operations. With advancements in technology and the growing demand for high-precision components, centerless grinding on surface grinders is set to remain a critical component of many production processes.