Centerless grinding on a surface grinder offers an exceptional approach for industries seeking precision, efficiency, and superior surface finishes in their manufacturing processes. In today's competitive manufacturing landscape, where accuracy and dependability play paramount roles, understanding the intricacies of centerless grinding on a surface grinder can significantly impact product outcomes.
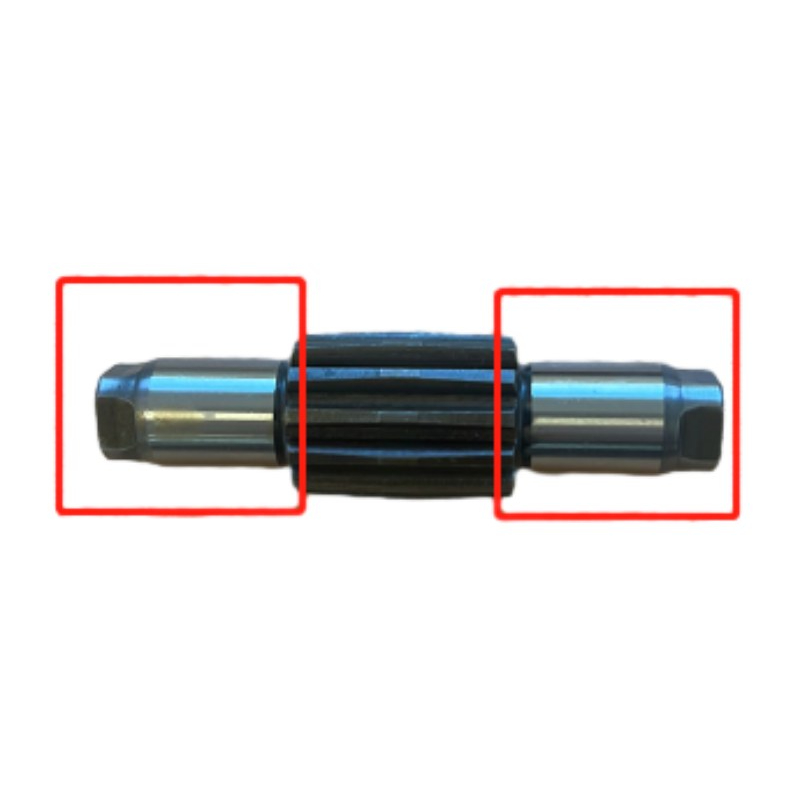
Unlike traditional grinding methods, centerless grinding involves the process of removing material from an object without the need for balancing or supporting the workpiece between centers. This technique proves indispensable in achieving high-level precision, especially for thin-walled, fragile, or extended pieces that are difficult to secure. By eliminating the necessity of mounting centers, manufacturers can produce concentric workpieces with impeccable surface quality in significantly lesser time.
Experience in utilizing centerless grinding on a surface grinder denotes the recognition of its capability in dealing with high volume production runs seamlessly. Over extensive years of application, it becomes apparent that the expertise lies in precision setup and continuous monitoring of the grinding process. Engineers and operators must ensure that the workpiece is positioned correctly between the grinding wheel and the regulating wheel. Moreover, selecting the appropriate abrasive material and grind speed based on the material composition of the workpiece can prevent thermal damages and ensure longevity of both the workpiece and equipment.
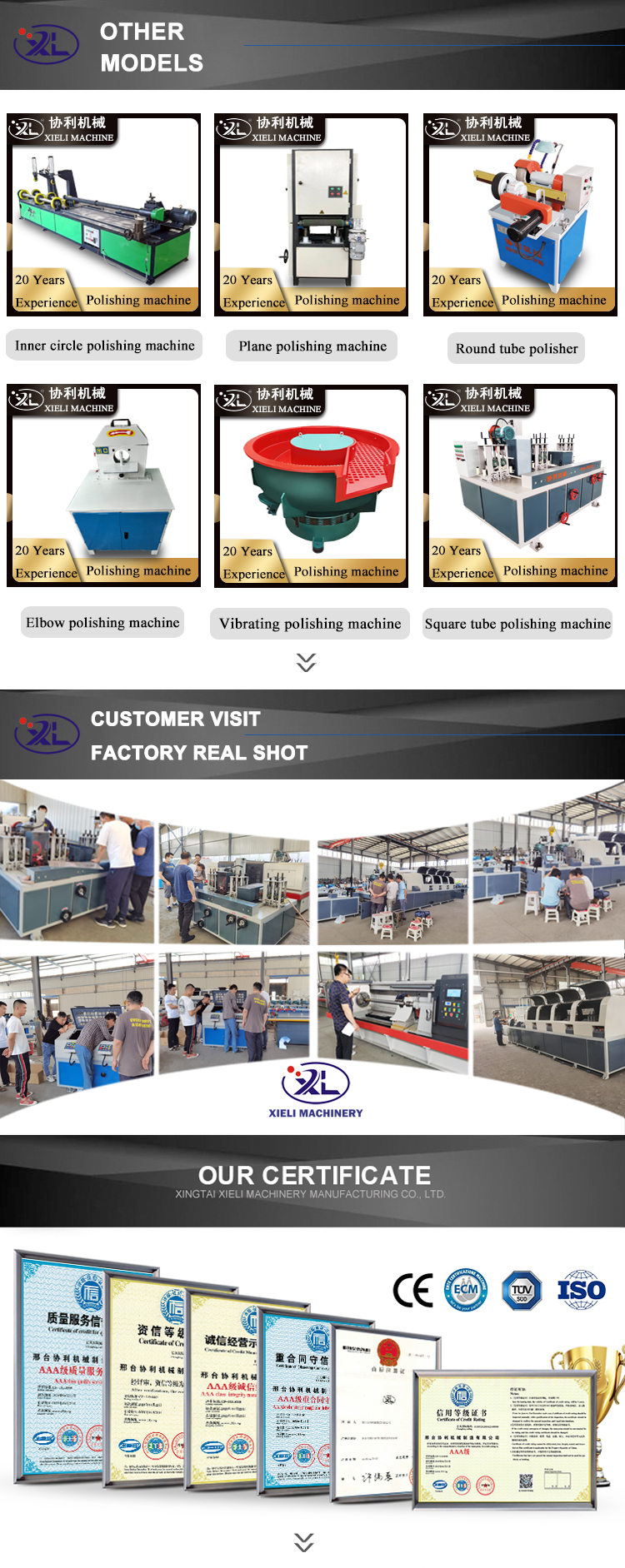
Professionalism in the domain is demonstrated by a thorough understanding of aspects such as wheel dressing dynamics, workpiece displacement, and potential vibration impacts during the grinding process.
Each parameter plays a crucial role in defining the surface finish and tolerances achievable. Customizing the feed rate, regulating wheel angle, and workpiece rotational speed can lead to optimum grinding conditions, resulting in products that consistently meet stringent specifications.
centerless grinding on surface grinder service
Employing centerless grinding techniques on surface grinders is recognized by industry experts for its ability to deliver unparalleled accuracy and repeatability, qualities essential in high-precision sectors such as aerospace, automotive, and medical device manufacturing. The absence of a spindle in centerless grinding eliminates any potential for imbalance issues, ensuring consistent, high-quality outputs even in mass production settings.
Trustworthiness in implementing centerless grinding services lies in an adherence to stringent quality control protocols. Reliable service providers deploy advanced technology, such as real-time monitoring systems and automated feedback loops, to maintain process integrity. Continuous training of operators, coupled with adherence to regulatory standards, fortifies the credibility of these services, assuring clients of the rigorous quality standards maintained at every step.
In conclusion, integrating centerless grinding techniques with surface grinders propels manufacturing capabilities by enhancing productivity and reducing operational complexities. The leverage provided by this method allows for the production of components with superior quality and precision, ensuring they meet specific engineering requirements. Collaborating with seasoned professionals who have a profound understanding of the process intricacies fortifies a company’s manufacturing efficiency and fosters trust and reliability in their output. Such expertise and experience ensure the successful implementation of these grinding processes, solidifying their place as indispensable tools in precision manufacturing.
For More Details Pls Contact Us
Fiberglass Reinforced Plastic (FRP), also known as fiber-reinforced plastic, is a composite material widely used across various industries.