Centerless Grinding Machine Parts Service Ensuring Precision and Efficiency
In the world of manufacturing, precision is paramount. For industries that demand high tolerance and superior surface finish, centerless grinding machines play a crucial role. These machines are designed to grind cylindrical parts with exceptional accuracy and consistency, but like any sophisticated machinery, they require regular maintenance and service to perform optimally. This article explores the importance of centerless grinding machine parts service and how it contributes to operational efficiency.
Understanding Centerless Grinding Machines
Centerless grinding is a machining process that uses abrasive cutting to remove material from a workpiece. Unlike traditional grinding processes, centerless grinding does not require a central axis to hold the workpiece in place. Instead, it utilizes a combination of wheels and guides to stabilize and control the workpiece during the grinding operation. This design enables the machining of long shafts and cylindrical parts without the risk of distortion.
The core components of a centerless grinding machine include the grinding wheel, regulating wheel, work rest blade, and the support structure. Each component plays a vital role in the grinding process, and any wear or malfunction can adversely affect the quality of the finished product.
The Importance of Regular Parts Service
Regular service of centerless grinding machine parts is essential for several reasons
1. Maintaining Precision Over time, the grinding and regulating wheels can wear down, leading to imprecise cuts and surface finishes. By routinely assessing and replacing these parts, manufacturers can maintain tight tolerances and ensure their products meet strict quality standards.
2. Preventing Downtime Machine breakdowns can lead to costly downtime in production. A proactive approach to parts service—including timely replacements and repairs—can significantly reduce the risk of unexpected failures. This preventive maintenance strategy keeps production running smoothly and enhances overall efficiency.
3. Extending Equipment Life Well-maintained machines have a longer operational lifespan. Regular service helps identify potential issues before they escalate, thereby protecting the investment made in the machinery. This can lead to substantial cost savings over time.
centerless grinding machine parts service
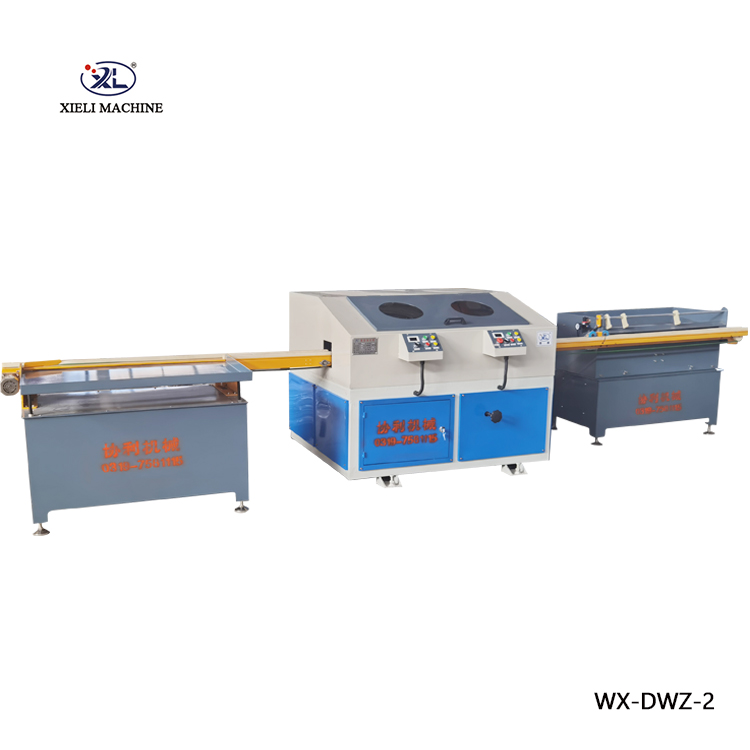
4. Improving Safety Worn or damaged parts can pose safety risks to operators. By ensuring that all components are in good condition, companies can create a safer working environment and reduce the likelihood of accidents.
Components That Require Regular Service
Some key components of centerless grinding machines that should be regularly serviced include
- Grinding and Regulating Wheels These wheels need to be dressed and balanced periodically. Proper dressing ensures that the wheels retain their cutting efficiency and produce desired finishes.
- Work Rest Blades The work rest blade must be adjusted to support the workpiece correctly. Over time, these blades can wear down or become misaligned, compromising the grinding process.
- Hydraulic Systems If the machine uses hydraulic systems for operations, regular checks on hydraulic fluid levels and filters are crucial to maintain pressure and prevent leaks.
- Bearings and Drives Monitoring bearings and drive systems for wear and tear can prevent significant issues that could halt production.
Conclusion
The seamless operation of centerless grinding machines largely depends on the condition of their parts. Regular service and maintenance are foundational to achieving precision and efficiency in the grinding process. Manufacturers should prioritize a structured maintenance schedule that includes inspections, replacements, and adjustments of critical components. By investing in service for centerless grinding machine parts, companies can ensure consistent output quality while minimizing costly disruptions. Ultimately, a well-serviced machine translates into greater productivity and profitability in the competitive manufacturing landscape.