Integrating Centerless and Surface Grinding A New Era of Precision Manufacturing
In the realm of manufacturing, precision and efficiency are paramount. With the incessant drive for improved productivity and quality, many industries are turning towards advanced grinding technologies. Among these, centerless grinders and surface grinders are two essential tools that have earned their place in modern machining operations. The integration of these two grinding methods not only enhances the capabilities of manufacturing processes but also brings about innovative solutions for various engineering challenges.
Understanding Centerless and Surface Grinding
Centerless grinding is a technique used to grind cylindrical parts without the need for supporting the workpiece on centers. This method employs a unique setup where the workpiece is positioned between two rotating wheels—the grinding wheel and the regulating wheel. This configuration allows for continuous feeding of parts, enabling high-volume production with excellent accuracy. It is particularly effective for producing long, slender components such as rods, tubes, and shafts, making it indispensable in industries like automotive and aerospace.
On the other hand, surface grinding is a method used for producing a smooth finish on flat surfaces. In this process, a rotating grinding wheel is used with coolant to grind the surface of a workpiece. Surface grinders can achieve tight tolerances and a high degree of flatness, making them ideal for producing precision mechanical components. Industries often use surface grinders for applications requiring fine finishes, flat surfaces, and specific geometric profiles.
The Benefits of Combining Centerless and Surface Grinders
The combination of centerless grinding and surface grinding technologies offers substantial benefits to manufacturers. One of the primary advantages is the ability to produce complex geometries and surfaces with extreme precision. For instance, during the production of a component that requires both cylindrical and flat surfaces, utilizing both types of grinders can significantly reduce production time and improve overall quality.
centerless grinder with a surface grinder products
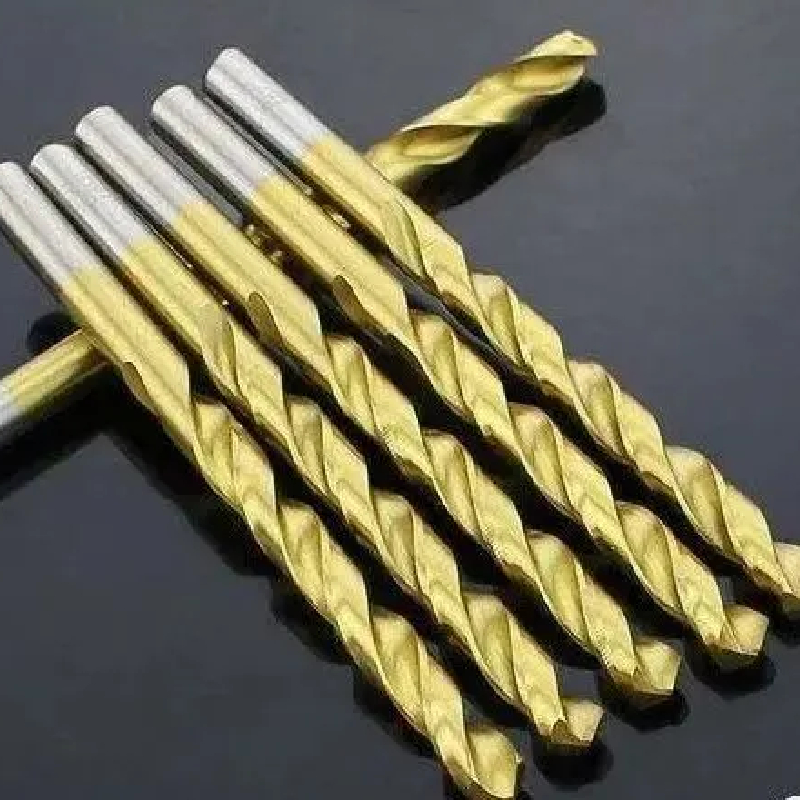
Additionally, employing this integrated approach allows for enhanced throughput. By processing parts through both grinding methods consecutively, manufacturers can achieve leaner operations, reducing work-in-progress inventory and cutting lead times. This is particularly beneficial in industries that demand high productivity paired with stringent quality controls.
Moreover, the combined process enables manufacturers to address part-specific requirements more effectively. For example, a centerless grinding operation might achieve the desired diameter and roundness for a cylindrical part, while a subsequent surface grinding process can be employed to ensure that specific surface finishes meet regulatory standards or performance criteria. This complementary approach reduces the need for secondary operations, such as polishing or additional machining, thus streamlining workflows.
Applications Across Industries
The integration of centerless and surface grinding is especially applicable in sectors where precision and efficiency are crucial. In the automotive industry, components such as valve stems, crankshafts, and camshafts often require both cylindrical and flat grinding operations. The ability to achieve tight tolerances across these different surfaces ensures that parts fit correctly and operate smoothly, directly impacting vehicle performance and reliability.
Similarly, in the aerospace sector, the demand for lightweight and durable components necessitates the use of advanced grinding techniques to meet strict safety and performance standards. The combination of centerless and surface grinding can help manufacturers produce components such as landing gear, turbine blades, and fuel injectors that are not only precise but also meet the rigorous testing protocols of the industry.
Conclusion
The synergy between centerless and surface grinding technologies represents a significant advancement in manufacturing capabilities. This combination not only enhances precision and efficiency but also allows manufacturers to meet the diverse demands of modern industries. As technology continues to evolve, integrating different grinding methods will undoubtedly lead to improved production techniques, allowing for the creation of complex parts with high levels of accuracy and reduced lead times. In a rapidly changing economic landscape, businesses that adopt such integrated approaches will be well-positioned for success, driving innovation and maintaining a competitive edge in their respective markets.