Centerless Grinders and Surface Grinders Key Insights from Leading Manufacturers
In the realm of precision machining, both centerless grinders and surface grinders are essential machines that contribute significantly to the manufacturing of high-quality components. Their versatility and precision make them indispensable in various industries, including automotive, aerospace, and manufacturing. Understanding the functionality and applications of these machines, particularly from renowned manufacturers, can help businesses make informed decisions when investing in grinding technology.
Centerless Grinders Understanding the Technology
Centerless grinders are designed to grind cylindrical workpieces without the need for centering the workpiece on a spindle. Unlike traditional cylindrical grinders, which require the workpiece to be centered between two points, centerless grinders utilize a system of wheels, which are configured in a unique manner to hold the workpiece in place. This design allows for continuous production and efficient processing of parts, making it ideal for high-volume applications.
Leading manufacturers have developed advanced centerless grinding machines that feature enhanced automation, precision, and ease of operation. The key advantages of these machines include their ability to grind multiple pieces simultaneously, reduced cycle times, and improved surface finishes. In addition, modern centerless grinders are equipped with computer numerical control (CNC) technology, providing operators with the ability to program complex grinding operations and achieve remarkable repeatability.
Surface Grinders Precision and Versatility
Surface grinders, on the other hand, are designed primarily for producing a flat surface on a workpiece. The grinding process involves a rotating abrasive wheel that removes material from the surface of the part, allowing for tight tolerances and superior flatness. Surface grinders are widely used in toolmaking, metalworking, and repair applications, making them invaluable to a multitude of sectors.
centerless grinder with a surface grinder manufacturer
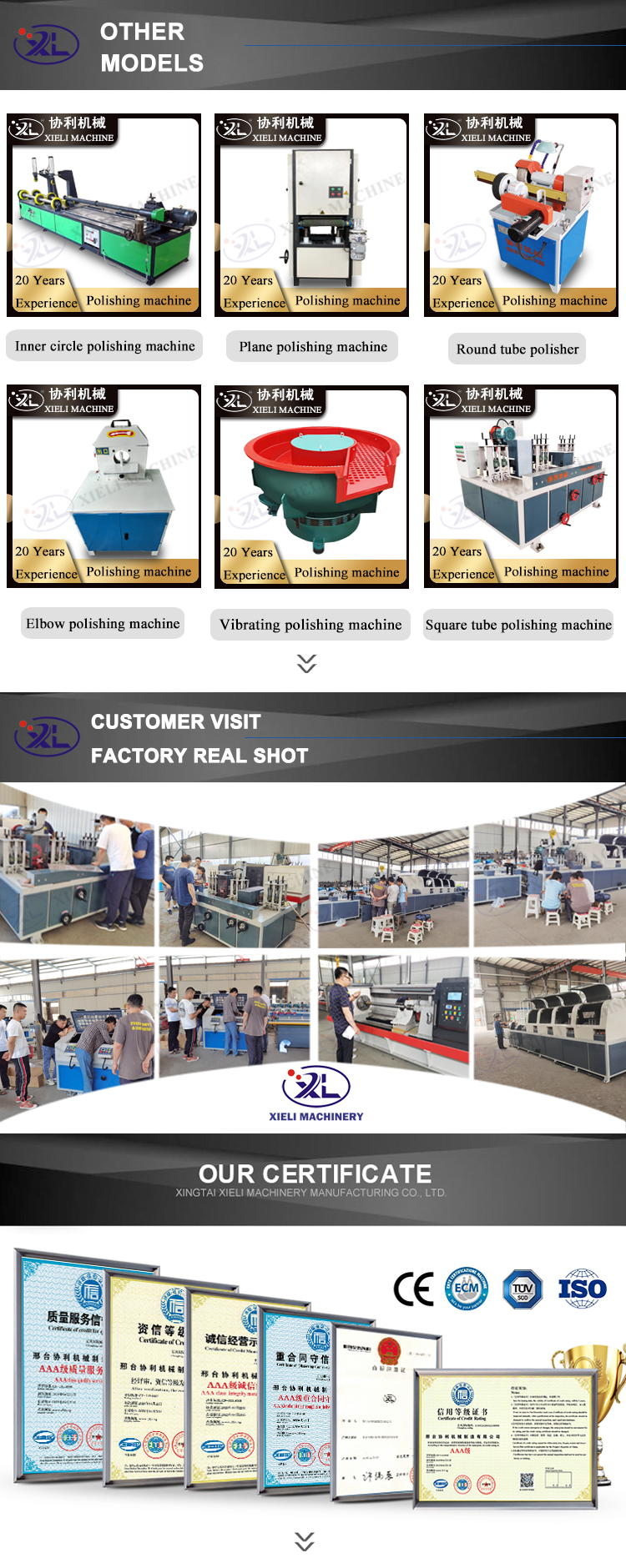
Renowned surface grinder manufacturers have consistently innovated their machines, introducing features such as automatic feeds, programmable grinding cycles, and sophisticated cooling systems. These enhancements not only improve the efficiency of the grinding process but also ensure that operators can achieve exceptional surface finishes with minimal user intervention.
Complementary Roles in Manufacturing
While centerless grinders and surface grinders serve distinct purposes, they often complement each other in a manufacturing environment. For instance, a company may use a centerless grinder to achieve the desired diameter on cylindrical components and then follow up with a surface grinder to enhance the surface finish or meet specification requirements. This two-step approach ensures that the final products meet both dimensional accuracy and surface quality standards.
The interplay between these machines highlights the importance of investing in high-quality grinding technology. Leading manufacturers provide comprehensive solutions that include both centerless and surface grinding equipment, often packaged with support services such as installation, training, and maintenance. This holistic approach not only streamlines operations for businesses but also enhances productivity and reduces downtime.
Conclusion
In summary, the significance of centerless grinders and surface grinders in modern manufacturing cannot be overstated. As technology continues to evolve, leading manufacturers are committed to enhancing the capabilities of these machines, ensuring they meet the diverse needs of their customers. For businesses seeking to improve their grinding processes, understanding the functionalities of these machines and investing in reliable equipment from reputable manufacturers will ultimately lead to greater production efficiency and product quality. This, in turn, translates to a competitive edge in an increasingly demanding market.