Centerless Grinder with Surface Grinder Factories Innovating Precision Machining
In the realm of modern manufacturing, precision machining plays a crucial role in ensuring product quality and efficiency. Among the various tools employed in this domain, centerless grinders and surface grinders stand out for their ability to produce highly accurate and finely finished components. In factories dedicated to these technologies, significant advancements have been made to enhance performance, reduce production times, and improve overall productivity.
Understanding Centerless and Surface Grinding
Centerless grinding is a method that enables the grinding of cylindrical workpieces without the need for fixture supports. The process relies on the positioning of the workpiece between two wheels—one for grinding and another for regulating the rotation of the workpiece. This configuration allows for continuous feeding of workpieces, improving throughput while maintaining precision.
On the other hand, surface grinding focuses on producing flat surfaces on a workpiece through a grinding wheel. It is essential for applications requiring specific flatness tolerances and surface finishes. Surface grinders can handle various materials, including metals and plastics, and are widely used in automotive, aerospace, and tool-making industries.
The Synergy of Centerless and Surface Grinding
While both centerless grinders and surface grinders serve distinct functions, their integration in manufacturing plants presents several advantages. Factories equipped with both machines can leverage their strengths to achieve enhanced productivity. For instance, a component may initially undergo centerless grinding to achieve the desired diameter and tolerance before being transferred to a surface grinder for final finishing. This two-step process maximizes efficiency and minimizes the risk of errors, ensuring superior quality in the final product.
Innovations in Grinding Technology
Advancements in technology have significantly transformed how centerless and surface grinders are operated. Modern factories employ CNC (Computer Numerical Control) systems that automate the grinding processes, ensuring consistent precision and significantly reducing labor costs. These systems can be programmed to perform multiple operations, further streamlining workflows.
centerless grinder with a surface grinder factories
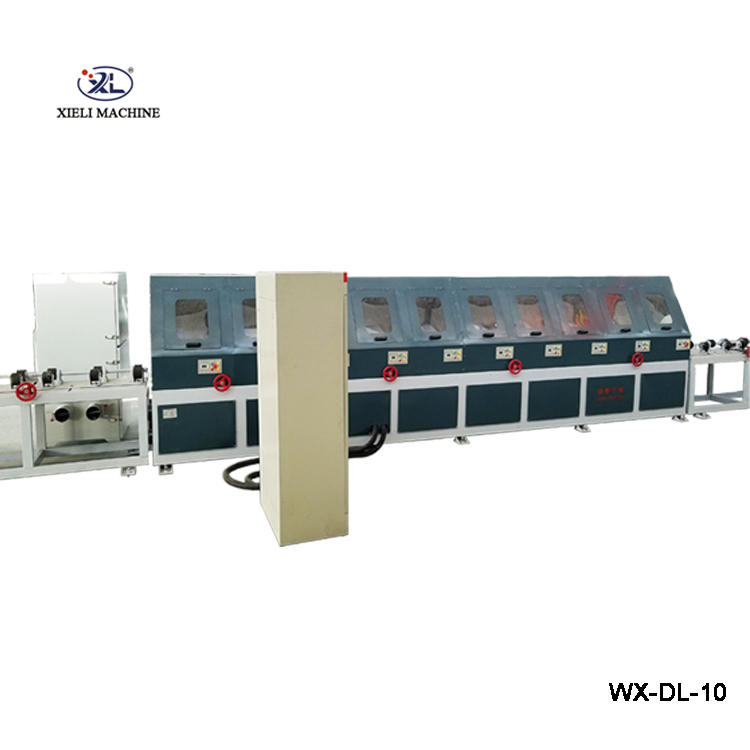
Additionally, manufacturers are continually researching new grinding wheel materials and technologies. Innovations such as diamond and CBN (Cubic Boron Nitride) wheels offer enhanced durability and better cutting performance, enabling factories to grind harder materials with ease. This evolution not only improves the efficiency of the grinding process but also extends the lifespan of grinding tools, ultimately reducing production costs.
Quality Control and Precision Engineering
In today's industrial environment, quality control is of paramount importance. Factory setups that house both centerless and surface grinding machines incorporate sophisticated measurement and inspection technologies. This often includes the use of laser measurement systems and coordinate measuring machines (CMM) to ensure that every component meets stringent specifications.
By implementing rigorous quality control measures, manufacturers can guarantee that their products not only comply with regulatory standards but also exceed customer expectations. This commitment to quality positions factories as leaders in the competitive market of precision machining.
The Future of Grinding Operations
As industries evolve, the demand for precision machined components continues to rise. The integration of centerless grinders and surface grinders in manufacturing processes is poised to grow, driven by advancements in automation, machine learning, and data analysis. Factories that embrace these technologies will likely gain a competitive edge, optimizing their operations and fulfilling the diverse needs of their clients.
Moreover, sustainability is becoming an essential consideration. Modern grinding technology aims to reduce waste and energy consumption, contributing to environmentally friendly manufacturing practices. Factories are investing in equipment that not only increases efficiency but also uses resources more responsibly.
Conclusion
In summary, the collaboration of centerless and surface grinders within manufacturing facilities heralds a new era of precision machining. By embracing technological advancements and fostering innovation, these factories can meet the evolving demands of various industries while ensuring top-quality products. As we look to the future, the synergy between these two vital machines will continue to shape the landscape of precision engineering, driving progress and excellence in manufacturing practices.