The Evolution of Centerless Grinder Wheels A Look into the Factory Manufacturing Process
Centerless grinding is an essential process used in various industries, including automotive, aerospace, and manufacturing, to produce precision components with tight tolerances. At the heart of this process lies the centerless grinder wheels, which are critical in shaping and finishing metal and other materials. This article explores the manufacturing process of centerless grinder wheels in a factory setting, highlighting the technology, materials, and quality control methods used to ensure optimal performance.
Understanding Centerless Grinding
Before delving into the manufacturing of centerless grinder wheels, it’s important to understand what centerless grinding is. Unlike traditional grinding techniques, where the workpiece is held between two centers, centerless grinding involves supporting the workpiece on a work rest while being grinded by grinding wheels. This method allows for continuous operation, enabling faster production rates and greater efficiency.
The Manufacturing Process of Centerless Grinder Wheels
The production of centerless grinder wheels begins with selecting high-quality raw materials. The most commonly used materials are aluminum oxide, silicon carbide, and diamond, each chosen based on the specific application and required grinding performance. The quality of these raw materials is paramount, as it directly affects the durability and efficiency of the grinding wheels.
1. Material Preparation The raw materials are mixed and processed to achieve the desired consistency and characteristics. This usually involves grinding the materials to a fine powder, which ensures uniformity. Additives are sometimes included to enhance the bonding process and improve the wheel's overall performance.
2. Bonding Process The powdered materials are then combined with a bonding agent. The bonding agents can be resin, vitrified, or rubber, depending on the intended application and the desired properties of the grinding wheel. This step is crucial, as the bond influences how the grains adhere to each other and to the wheel.
centerless grinder wheels factory
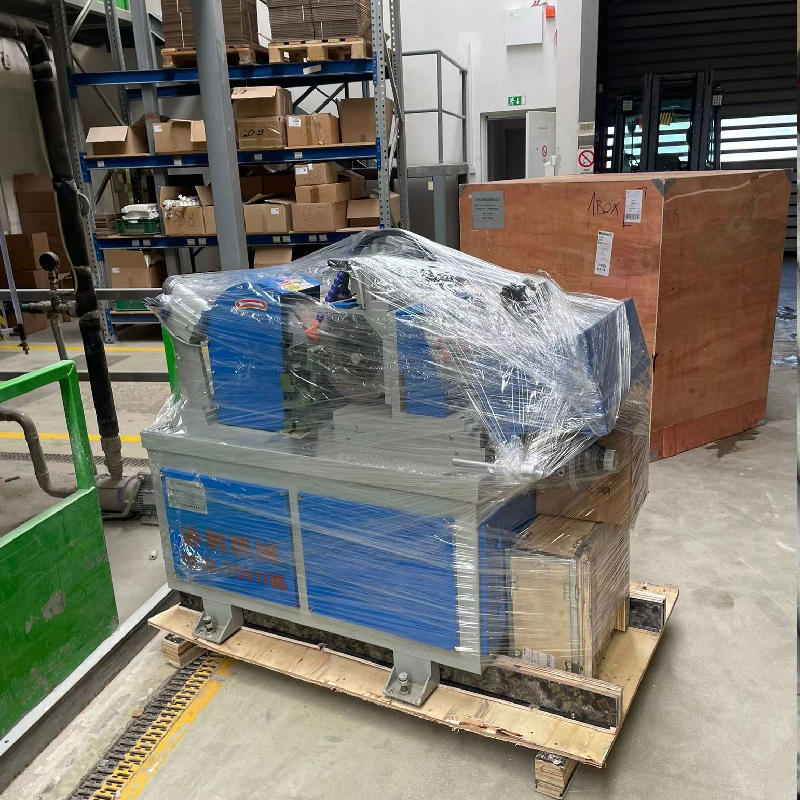
3. Shaping the Wheels Once the mixture is prepared, it is pressed into molds to form the shape of the grinding wheels. This process typically involves either cold pressing or hot pressing, depending on the materials used. The wheels are then cured in an oven, which hardens the bond and ensures structural integrity.
4. Truing and Balancing After curing, the wheels undergo a truing process, where they are shaped and balanced to achieve a precise diameter and surface finish. This step is vital because an unbalanced wheel can lead to vibrations during operation, negatively impacting the grinding process.
5. Quality Control Quality assurance is a critical aspect of manufacturing centerless grinder wheels. Each batch of wheels is subjected to rigorous testing, including dimensional checks, hardness tests, and performance evaluations. This ensures that each wheel meets the industry standards and customer specifications.
The Role of Technology
Modern factories utilize advanced technology to enhance the production of centerless grinder wheels. Computer numerical control (CNC) machines are increasingly used for precision shaping and grinding of the wheels. Automation in the manufacturing process reduces human error and improves efficiency, allowing factories to scale production while maintaining consistent quality.
Conclusion
The manufacturing of centerless grinder wheels involves a meticulous process that combines technology, quality materials, and strict quality control measures. As industries continue to evolve, the demand for high-performance grinding wheels will grow, prompting factories to innovate and adopt new technologies. By understanding this manufacturing process, stakeholders can appreciate the complexity and importance of centerless grinder wheels in precision engineering.