An Overview of Centerless Grinder Wheels
Centerless grinding is a machining process that utilizes a grinding wheel, regulating wheel, and a workpiece, which is held in place by the grinding and regulating wheels. This innovative method offers significant advantages in terms of efficiency and precision, making it indispensable in various manufacturing sectors.
Types of Centerless Grinder Wheels
There are two main types of centerless grinder wheels the grinding wheel and the regulating wheel. The grinding wheel is responsible for removing material from the workpiece, while the regulating wheel controls the speed and feed of the workpiece into the grind zone. Both wheels can be made from various materials, including aluminum oxide, silicon carbide, and ceramic, to cater to different grinding requirements. The choice of wheel material can greatly influence the performance and finish of the machined part.
1. Grinding Wheel This wheel is usually larger and is made from abrasive materials that are suitable for the material of the workpiece. The grit size can vary depending on the desired finish and removal rate. Coarser grits are used for material removal, while finer grits are employed for achieving a smooth surface finish.
2. Regulating Wheel Typically made of softer materials than the grinding wheel, the regulating wheel helps in holding the workpiece in place and controlling its rotation and advancement. The surface of this wheel can also be modified (e.g., rubberized) to enhance friction and provide better control over the workpiece feed rate.
Advantages of Centerless Grinding
Centerless grinding offers numerous benefits compared to traditional grinding methods
. Some of these include- Increased Efficiency Because the workpiece does not need to be held in a chuck or fixture, centerless grinding allows for a continuous process and increases throughput. This can be especially advantageous in high-volume production environments.
centerless grinder wheels
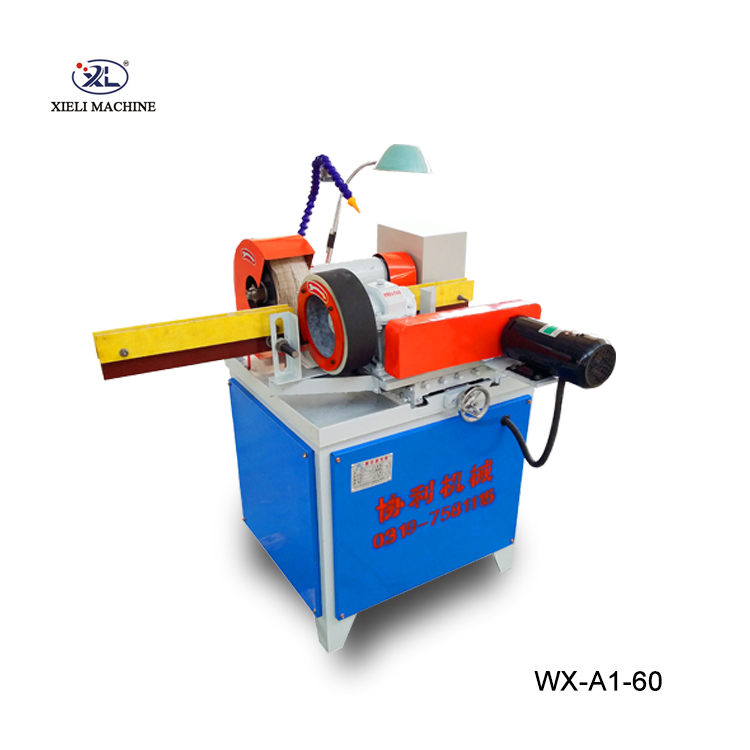
- Precision Centerless grinding can achieve tight tolerances and excellent surface finishes, which are vital in industries such as aerospace, automotive, and medical device manufacturing. The ability to grind parts without the constraints of clamping enables higher precision and reduces runout.
- Versatility This method can accommodate various shapes and sizes of parts, from small pins to large shafts, making it incredibly versatile. Additionally, it can be used for various materials, including metals and plastics.
Challenges and Considerations
While centerless grinding offers several advantages, it also presents unique challenges that operators must be aware of
- Setup Complexity Proper alignment of the wheels and workpiece is critical for successful centerless grinding. An incorrect setup can lead to poor performance, excessive wear on the wheels, and suboptimal finish.
- Wear and Tear Over time, grinding wheels will wear down and require replacement. The wear characteristics depend on the material being ground and the specifics of the grinding operation. Regular monitoring and maintenance of wheel condition are essential to maintain quality output.
- Temperature Control The grinding process generates heat, which can lead to thermal distortion of the workpiece if not managed properly. Operators must implement cooling techniques, such as using coolant or incorporating periodic pauses in the grinding process, to mitigate this issue.
Conclusion
Centerless grinder wheels are an integral part of modern machining processes, providing efficiency, precision, and adaptability. The choice of grinding and regulating wheels can significantly impact the overall performance of centerless grinding operations. By understanding the types of wheels and the factors that influence their effectiveness, manufacturers can optimize their machining processes, reduce production costs, and ensure high-quality output. For industries that prioritize precision, the centerless grinding process remains a preferred choice, securing its place in the future of machining technologies.