Troubleshooting Centerless Grinders A Guide for Suppliers
Centerless grinding is a highly efficient manufacturing process used for creating precision parts. However, like any machinery, centerless grinders can encounter various issues that may affect their performance and productivity. As suppliers, understanding these common problems and their troubleshooting methods can help you assist your clients effectively, ensuring their machinery operates smoothly and efficiently.
Common Issues in Centerless Grinders
1. Misalignment One of the most frequent issues faced by users of centerless grinders is misalignment. This can result in uneven grinding and poor surface finishes. Misalignment can occur due to regular wear and tear or incorrect setup.
2. Inconsistent Grinding Variability in grinding results can arise from several factors, including wheel wear, inconsistent feed rates, and improper wheel dressing. These inconsistencies can lead to defects in the finished product.
3. Overheating Excessive heat generation during grinding can lead to changes in material properties, affecting the dimensions and surface quality of the workpieces. Overheating may be due to inadequate cooling or excessive grinding pressure.
4. Vibration Unwanted vibrations can significantly affect the precision of a centerless grinder. These vibrations can stem from an unbalanced wheel, improper setup, or mechanical failures.
5. Dressing Issues Wheel dressing is crucial for maintaining the grinding wheel’s shape and sharpness. Problems with dressing can lead to suboptimal performance and increased production costs.
Troubleshooting Steps
Although troubleshooting can vary based on the specific model of the centerless grinder, here are some general steps suppliers can recommend
centerless grinder troubleshooting suppliers
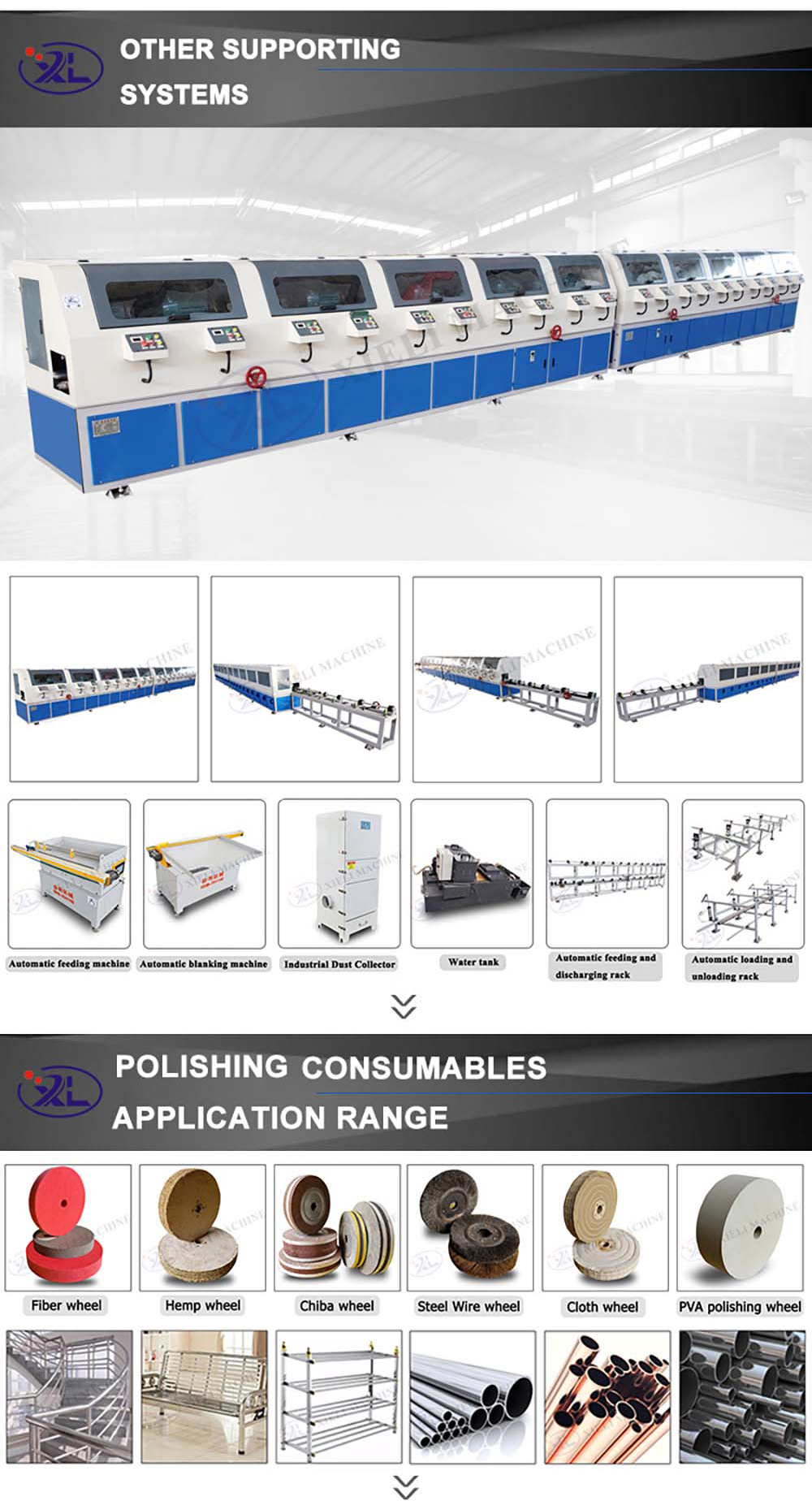
1. Check for Alignment Start by examining the setup of the machine. Ensure that the workpiece support, regulating wheel, and grinding wheel are correctly aligned. Adjust the height and angle of the regulating wheel and the grinding wheel to achieve proper alignment.
2. Inspect Components Encourage clients to conduct a thorough inspection of the components, including wear and tear on the grinding wheel and regulating wheel. Replace any worn parts as needed to maintain efficiency.
3. Wheel Dressing Ensure that the grinding wheel is adequately dressed before operation. Recommend using appropriate dressing tools and techniques to maintain the wheel’s shape and sharpness.
4. Monitor Cooling Systems Check the coolant levels and the cooling system’s efficiency. Inadequate cooling can lead to overheating, which can adversely affect the grinding process. Promote the use of high-quality coolant to enhance performance.
5. Vibration Analysis For vibration issues, suggest performing a vibration analysis to identify the source of the problem. It may be necessary to rebalance the grinding wheel or inspect machine components for wear or damage.
6. Adjust Feed Rates Inconsistent grinding may require clients to adjust feed rates. Too fast a feed rate can lead to increased wear, while too slow can affect productivity. Finding the optimal feed rate is essential for achieving consistent results.
7. Train Operators Provide training sessions for operators to enhance their understanding of the machine and troubleshoot minor issues independently. Well-trained operators are vital for maintaining machine performance and reducing downtime.
Conclusion
By equipping your clients with knowledge about common centerless grinder issues and their solutions, you position yourself as a valuable supplier who understands the intricacies of the machinery they rely on. Regular maintenance and prompt troubleshooting can significantly reduce downtime and enhance productivity in manufacturing operations. Creating strong relationships with clients through support and guidance can lead to long-term partnerships.
At the end of the day, being a supplier goes beyond just selling products; it’s about providing solutions and ensuring your clients can achieve the highest standards of quality and efficiency in their operations. Through proper troubleshooting and ongoing support, you can contribute significantly to their success.