Centerless Grinder Troubleshooting and Service
Centerless grinding is an essential manufacturing process, playing a crucial role in producing precision components with tight tolerances. However, like any other machinery, centerless grinders can encounter issues that may hinder their performance. Understanding how to troubleshoot common problems can significantly reduce downtime and improve the efficiency of your operations.
Common Issues in Centerless Grinders
1. Inconsistent Part Dimensions One of the most prevalent issues encountered during centerless grinding is inconsistency in the dimensions of the finished parts. This problem can be attributed to several factors, including incorrect wheel alignment, improper roller positioning, or worn-out grinding wheels. It's essential to check the alignment of the grinding wheel and the regulating wheel regularly. Adjusting these components can often resolve dimensional inconsistencies.
2. Excessive Wheel Wear Over time, grinding wheels wear down, which can affect the quality of the finished product. Excessive wheel wear can be caused by improper feed rates, incorrect wheel selection, or insufficient coolant application. Regular inspections of the grinding wheel and timely replacements are vital. Ensuring the correct selection of materials for both the wheel and the workpiece can help mitigate wear.
3. Vibration and Noise A well-functioning centerless grinder should operate smoothly and quietly. If you notice excessive vibration or noise, it could signify misalignment or issues with the motor or bearings. Regularly check the structural integrity of the machine and its components. Tightening loose parts and replacing worn bearings can help rectify these issues and restore smooth operation.
4. Overheating Overheating can significantly impact the life of both the grinding wheel and the workpiece. Several factors can contribute to overheating, including high feed rates, insufficient coolant, and improper wheel selection. It’s critical to monitor the grinding process closely and adjust the feed rates as necessary. Ensuring adequate coolant application not only helps prevent overheating but also prolongs the life of the grinding wheel.
5. Poor Finish Quality A poor surface finish can result from various factors such as incorrect wheel grit size, improper dressing of the wheel, or insufficient coolant. To achieve the desired surface quality, select the right grit size for the material being processed and ensure the grinding wheel is dressed correctly. Regular wheel maintenance, including dressing and balancing, is essential for optimal surface finish.
centerless grinder troubleshooting service
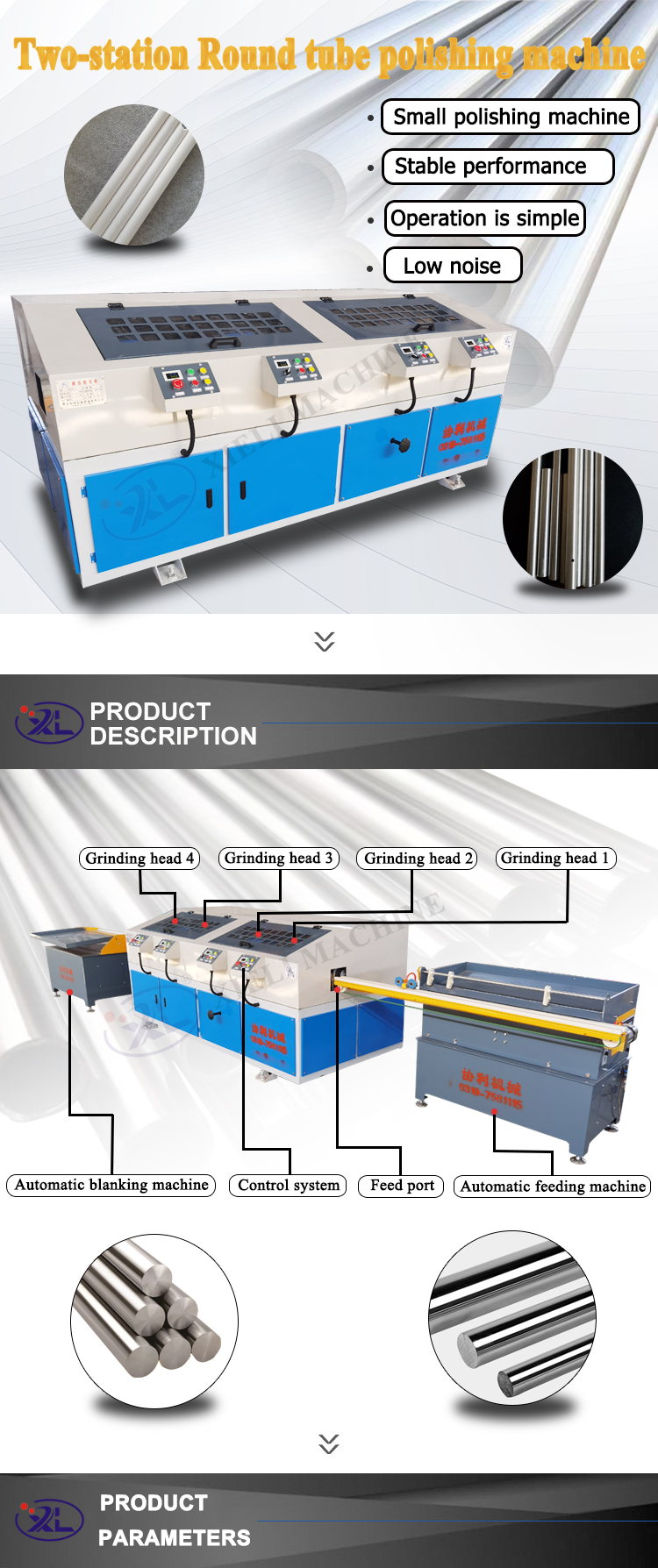
Routine Maintenance and Care
Preventive maintenance is key to minimizing troubleshooting issues in a centerless grinder. Establishing a regular maintenance schedule that includes the following practices will help ensure smooth operations
- Daily Inspections Check the grinder for loose bolts, leaks, and wear on belts and bearings. Address any issues immediately to avoid exacerbating problems.
- Coolant Maintenance Regularly check and replace coolant to ensure it remains effective. This helps in cooling the grinding process and prolongs the life of the grinding wheel.
- Wheel Dressing Regularly dress the grinding wheels to maintain their shape and effectiveness. This process ensures a consistent surface finish and optimal grinding performance.
- Training and Operation Ensure that all operators are adequately trained in the operation and troubleshooting of the centerless grinder. They should be familiar with the common issues and how to address them effectively.
In conclusion, troubleshooting a centerless grinder requires a combination of knowledge, experience, and routine maintenance. By understanding common problems and implementing preventive measures, manufacturers can optimize their grinding processes, reduce downtime, and achieve high-quality finished products. Regular maintenance and operator training are foundational elements in maintaining the efficiency and effectiveness of centerless grinders in any production environment.