Troubleshooting Centerless Grinders Tips and Insights
Centerless grinders are essential tools in precision machining, used primarily for cylindrical parts. Like any machinery, they can encounter issues that hinder performance and productivity. Effective troubleshooting is crucial to keep these machines operating efficiently. Below, we’ll explore common problems encountered with centerless grinders and provide insights into their solutions.
Understanding the Centerless Grinder
Before diving into troubleshooting, it’s important to understand how a centerless grinder operates. Unlike traditional grinding machines, where the part is held within fixed jaws, a centerless grinder utilizes two wheels—a grinding wheel and a regulating wheel—to hold and move the part. The workpiece is positioned between these wheels, allowing for continuous grinding without the need for additional clamping.
Common Problems and Solutions
1. Inconsistent Part Dimensions
One of the most common issues with centerless grinders is the production of parts that do not meet dimensional specifications. This can arise from several factors
- Wheel alignment Misalignment of the grinding and regulating wheels can lead to uneven grinding. Regularly check the alignment using a dial indicator and adjust as necessary. - Worn wheels Over time, grinding wheels and regulating wheels can wear down, leading to inconsistencies. Replace worn wheels to ensure uniformity in part dimensions. - Improper workpiece feed The feeding mechanism may lead to improper handling of the part. Confirm that the feed rate settings are appropriate for the material and size of the workpiece.
2. Grinding Marks or Improper Finish
A poor surface finish or visible grinding marks can detract from the quality of finished parts. Here are some common causes
- Dirty wheels and coolant Contaminants on the grinding wheel or coolant can lead to unwanted marks on workpieces. Ensure the wheels are clean and that the coolant system is functioning correctly. - Incorrect wheel selection Using the wrong grit size or bond type can also cause surface issues. Verify that the wheels are suitable for the material you're working with. - Excessive pressure Excessive pressure from the regulating wheel can cause heat buildup and surface damage. Adjust the pressure to maintain a balance between efficiency and surface integrity.
centerless grinder troubleshooting quotes
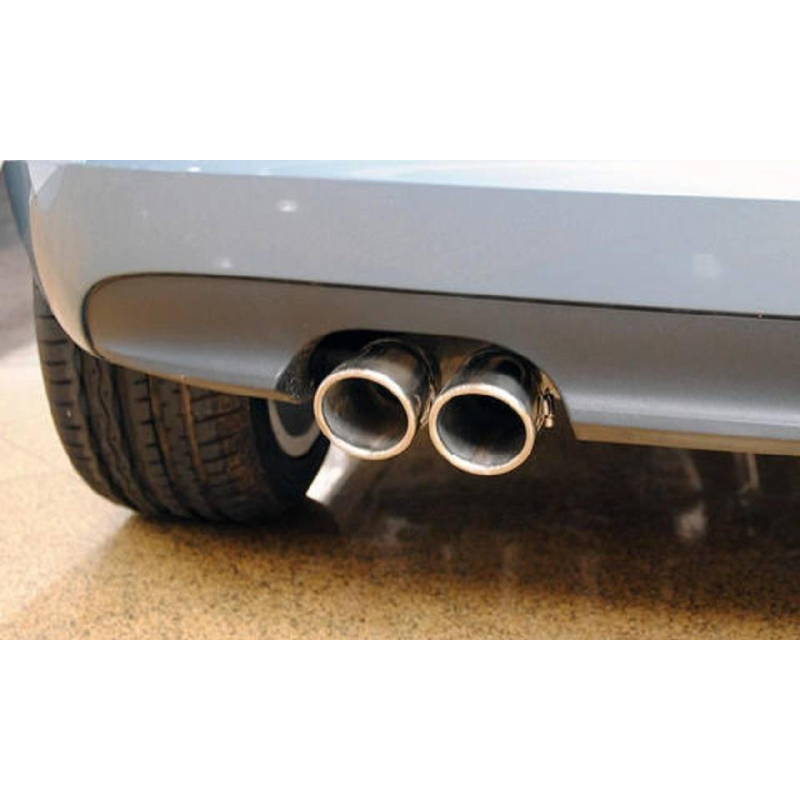
3. Overheating
Overheating in centerless grinders can lead to thermal damage of both the machine and the workpiece. Addressing this problem involves
- Coolant flow issues Insufficient coolant flow can lead to excessive heat. Ensure that the coolant system is operational and that the coolant levels are adequate. - Incorrect speed settings Running the machine at inappropriate speeds can increase friction and heat. Check and adjust the speed settings according to the specifications for the material being ground.
4. Vibration and Stability Problems
Vibrations can cause issues with part quality, leading to dimensional inaccuracies and surface defects. Key factors to consider include
- Machine foundation A stable and level foundation is crucial for minimizing vibrations. Check and adjust the leveling of the machine on the floor. - Worn bearings Worn or damaged bearings can exacerbate vibration problems. Inspect the bearings and replace them if necessary. - Tooling and fixturing Ensure that all tooling and fixtures are secure and in good condition, as loose components can contribute to vibration.
Best Practices for Preventive Maintenance
To minimize downtime and maintain optimal performance, it's essential to establish a routine preventive maintenance schedule. Here are some best practices
- Regular inspections Frequent checks on the alignment, wear of components, and fluid levels can identify issues before they escalate. - Cleaning Maintain cleanliness in and around the machine to prevent contamination and ensure safe operation. - Operator training Properly trained operators are less likely to make errors that lead to machine or part failures. Invest in training to enhance troubleshooting skills.
Conclusion
Troubleshooting centerless grinders can be daunting, but understanding common problems and their solutions can streamline repair processes and improve productivity. By implementing regular maintenance and fostering an environment of continuous learning, manufacturers can enhance the longevity and efficiency of their centerless grinding operations. Remember, proactive measures are always better than reactive fixes in the world of precision machining.