Troubleshooting Centerless Grinders Overcoming Common Challenges
Centerless grinding has become a cornerstone manufacturing process, particularly in the production of cylindrical and cylindrical-shaped components. This method provides a high level of precision and efficiency, making it an invaluable tool in industries ranging from automotive to aerospace. However, like any machine, centerless grinders can encounter various operational challenges. Troubleshooting these issues promptly and effectively is crucial to minimizing downtime and ensuring consistent output quality. This article will explore common problems associated with centerless grinders and general solutions for maintaining optimal performance.
Understanding the Basics
Before delving into troubleshooting, it's essential to understand how a centerless grinder operates. Unlike traditional grinders, centerless grinders are designed to grind parts without the need for a fixture. The workpiece is supported by a rotating platform and positioned between a grinding wheel and a regulating wheel. This setup allows for efficient material removal from the workpiece as it passes through the grinder.
Common Problems and Solutions
1. Inconsistent Part Dimensions One of the most frequent challenges encountered in centerless grinding is inconsistent part dimensions. This inconsistency can be attributed to several factors, including incorrect wheel alignment, inadequate wheel dressing, or worn grinding wheels. - Solution Regularly check the alignment of both grinding and regulating wheels. Ensure that they are properly dressed and that the wheels are not excessively worn. Aligning the wheels according to manufacturer specifications can significantly improve dimension consistency.
2. Overheating Overheating is another prevalent issue that can lead to damage to both the workpiece and the machine itself. Factors contributing to overheating include excessive feed rates, inadequate coolant application, or dull grinding wheels. - Solution Adjust feed rates according to the material being processed and the specifications provided by the grinder manufacturer. Ensure an adequate flow of coolant to minimize heat buildup and consider replacing grinding wheels that have become dull.
centerless grinder troubleshooting companies
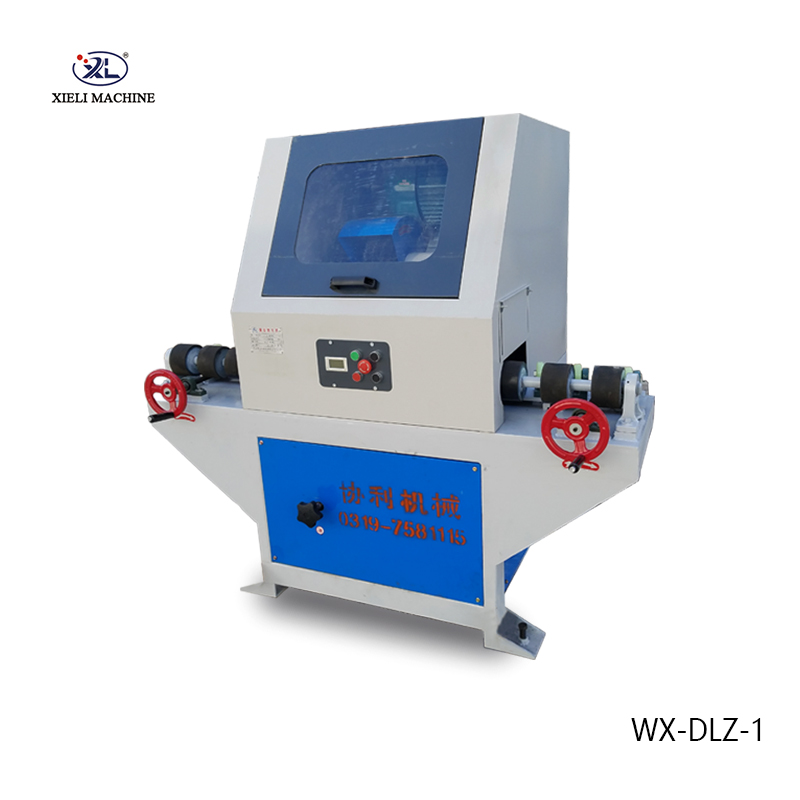
3. Chatter Marks Chatter marks or oscillations on finished parts may indicate vibrations within the grinding setup. These vibrations could stem from improper setup, tool wear, or machine stability issues. - Solution Inspect the grinding machine for stability and ensure that it is bolted securely to the floor. Replace worn components and assess the grinding fluid’s viscosity and flow, as improper coolant conditions can exacerbate vibration issues.
4. Part Slippage Slippage refers to the workpiece moving out of alignment during the grinding process, resulting in uneven grinding. - Solution Ensure that the regulating wheel is properly adjusted to maintain a firm grip on the workpiece. Examine the wheel’s condition, as a worn-out regulating wheel may contribute to slippage.
5. Excessive Wear of Regulating Wheel The regulating wheel plays a crucial role in controlling the speed and positioning of the workpiece. Excessive wear can affect part accuracy and lead to unproductive grinding. - Solution Regular maintenance is crucial. This includes routine dressing of the regulating wheel as well as periodic inspection to determine its wear rate. Replacement cycles should be established based on usage and wear patterns.
Preventive Maintenance
To mitigate many of these issues, implementing a preventive maintenance program is critical. Regular inspections, scheduled maintenance, and detailed logs of machine performance can help identify and address potential problems before they escalate. Training operators in best practices can result in better machine handling, ultimately improving the quality of the finished product.
Conclusion
Centerless grinding is an efficient and effective method for producing high-quality cylindrical parts. However, operational challenges can arise that may disrupt manufacturing processes. By understanding common problems and their potential solutions, companies can maintain productivity levels, optimize their grinding operations, and ensure that they meet quality standards consistently. With diligent troubleshooting and a commitment to preventive maintenance, manufacturers can overcome the obstacles associated with centerless grinding and enhance their overall competitiveness in the market.