Centerless Grinder Safety in Factories
Centerless grinding is an essential machining process used in various industries for producing cylindrical parts with high precision. While it is a highly effective manufacturing technique, the operation of centerless grinders poses inherent risks that can result in accidents if proper safety measures are not implemented. This article outlines the safety protocols and best practices that factories should adopt to ensure a safe working environment when operating centerless grinders.
Understanding the Risks
Centerless grinders operate at high speeds and involve sharp cutting tools, which can be hazardous if handled improperly. The primary risks associated with centerless grinding include
1. Contact with Moving Parts Operators can easily get caught in rotating components, leading to severe injuries. 2. Noise Exposure Prolonged exposure to high noise levels can cause hearing loss. 3. Dust and Particulate Matter Grinding operations can produce fine dust that is harmful to respiratory health. 4. Slips and Falls Oil spills and debris on the shop floor can lead to slips and falls, contributing to workplace injuries. To mitigate these risks, factories must prioritize safety and ensure that all personnel are well-trained and aware of the hazards associated with centerless grinding.
Safety Training and Awareness
Employee training plays a crucial role in promoting safety in any manufacturing environment
. Workers must undergo comprehensive training that includes1. Understanding Equipment Operators should be familiar with the machine's components, functions, and the specific dangers related to centerless grinders. 2. Personal Protective Equipment (PPE) Employees should wear appropriate PPE such as safety goggles, hearing protection, gloves, and steel-toed shoes to protect against potential hazards. 3. Emergency Procedures Workers should know how to respond in case of an emergency, including how to use emergency shut-off switches and where to find first-aid supplies.
Employers should conduct regular safety drills and refreshers to keep safety protocols at the forefront of their workers’ minds.
centerless grinder safety factories
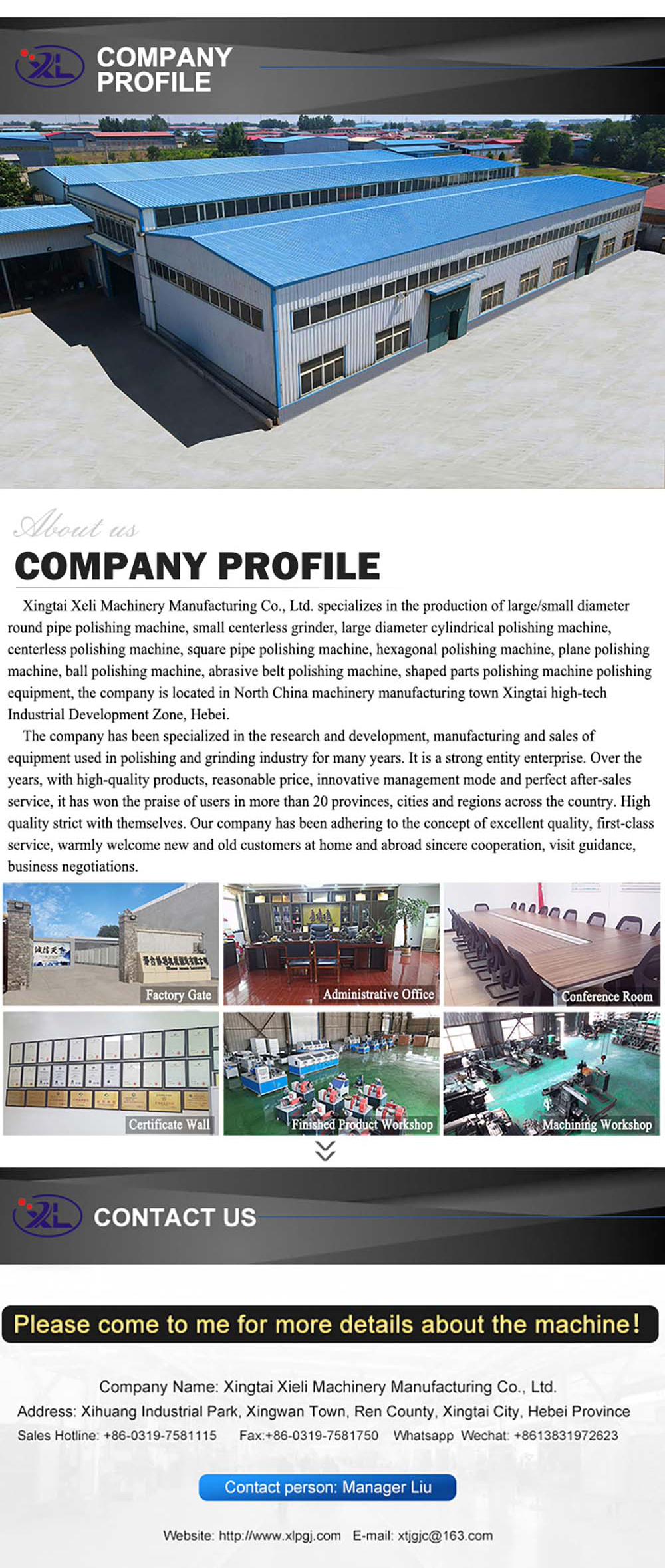
Machine Maintenance and Safety Features
Maintaining the centerless grinder is imperative for safe operation. Regular inspections must be conducted to ensure that all components, such as guards, belts, and wheels, are in good condition. Key practices include
1. Routine Checks Operators should perform daily checks on the machine before use, looking for loose parts, unusual vibrations, and any signs of wear and tear. 2. Preventive Maintenance Establish a preventive maintenance schedule that includes cleaning, lubrication, and replacement of worn-out parts. 3. Safety Guards Ensure that all safety guards are in place and functioning correctly. These guards are designed to protect the operator from debris and moving parts.
Creating a Safe Work Environment
A clean and organized workspace is vital for safety in the factory. Factories should implement the following measures
1. Housekeeping Maintain a clean work area by regularly cleaning up spills and removing debris. This minimizes the risk of slips and ensures operators can work efficiently. 2. Proper Storage Keep tools, materials, and equipment stored properly to avoid clutter and obstruction in high-traffic areas. 3. Signage Clearly mark hazardous areas with appropriate signage to remind employees of the risks and necessary protective measures.
Conclusion
Safety is paramount in the operation of centerless grinders in factories. By investing in comprehensive training, adhering to maintenance protocols, and fostering a culture of awareness and preparedness, employers can significantly reduce the risk of accidents. A proactive approach to safety not only protects workers but also enhances overall productivity, ensuring that the factory remains a safe and efficient environment for all. Implementing these safety measures is not just a regulatory requirement; it is a crucial aspect of responsible manufacturing that benefits both employees and the company in the long run.