Understanding Centerless Grinder Regulating Wheels and Their Suppliers
Centerless grinding is a critical manufacturing process that enables precision machining of various materials, including metals and plastics. At the heart of this process lies the regulating wheel, which plays a vital role in controlling the speed and positioning of the workpiece. As industries increasingly turn to automated manufacturing processes, the demand for high-quality centerless grinder regulating wheels has surged. This article explores the significance of these wheels, the factors to consider in selecting suppliers, and a few key players in the market.
The Role of Regulating Wheels in Centerless Grinding
Centerless grinding is unique in that it does not require the workpiece to be mounted between centers. Instead, the workpiece is held in place by a combination of the grinding wheel and the regulating wheel. The grinding wheel removes material from the workpiece, while the regulating wheel, typically positioned at an angle, controls the rotational speed and ensures consistent application of pressure.
The regulating wheel's design, including factors such as hardness, grit size, and material composition, directly affects the grinding process's efficiency and the smoothness of the finished product. Consequently, selecting the right regulating wheel is paramount for achieving optimal results in terms of precision and surface finish.
Factors to Consider When Choosing Suppliers
When sourcing regulating wheels for centerless grinders, several considerations are essential to ensure quality and reliability
1. Product Quality The supplier should provide products that meet industry standards and regulations. High-quality regulating wheels are typically manufactured from durable materials that ensure longevity and consistent performance.
2. Material Variety Different applications may require specific types of regulating wheels. Suppliers should offer a diverse range of wheels made from various materials, such as rubber, urethane, or resin-bonded materials, tailored to specific grinding tasks.
3. Custom Solutions Not all grinding applications are the same. A reputable supplier should be able to offer customized solutions based on the unique requirements of the client's operations, including custom sizes, shapes, and compositions.
4. Technical Support A good supplier provides technical assistance to help manufacturers select the right wheel for their application. This support can be crucial for troubleshooting or optimizing the grinding process.
centerless grinder regulating wheels suppliers
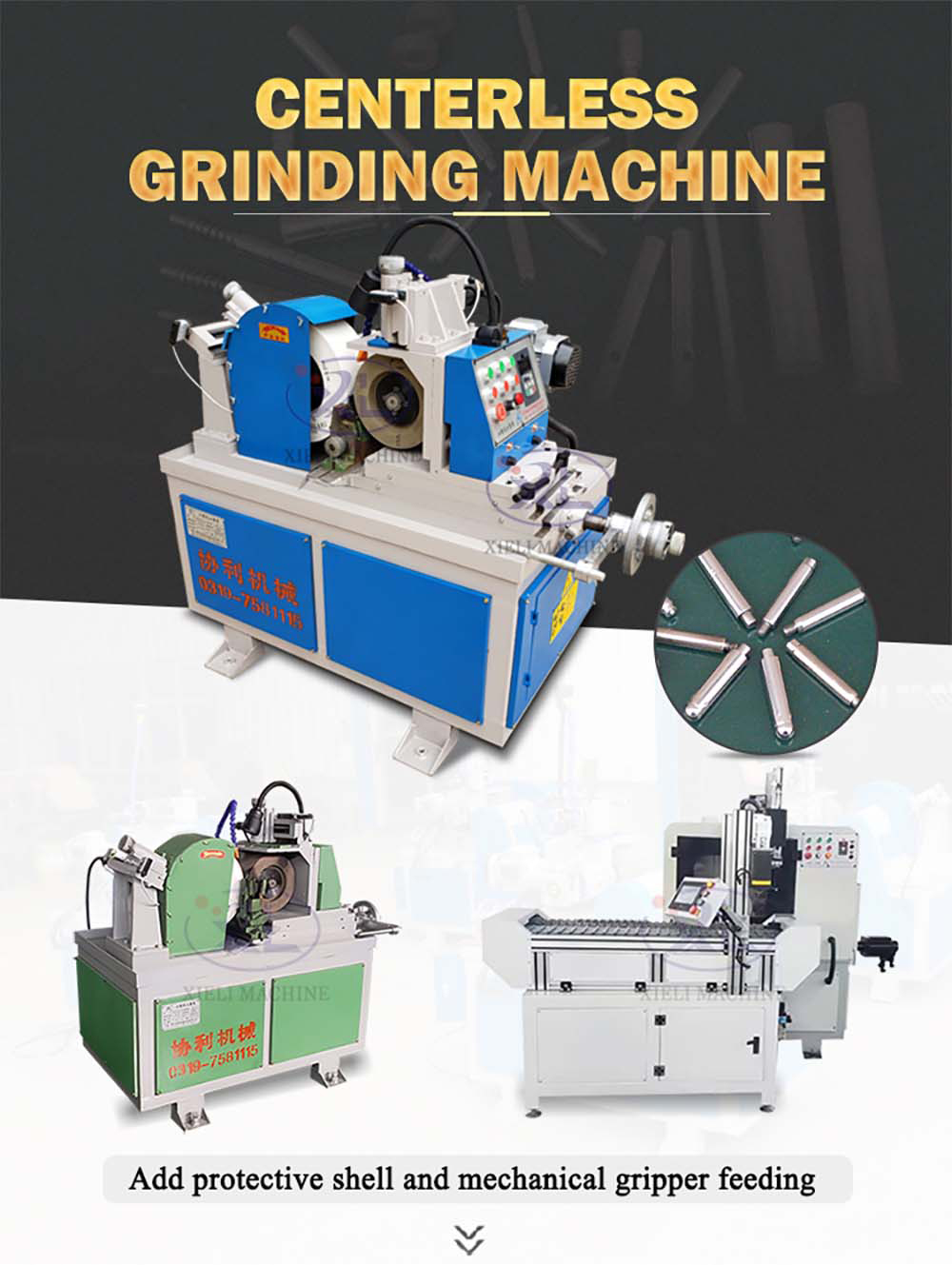
5. Delivery and Lead Times Timeliness is critical in manufacturing. Suppliers should have a reliable delivery schedule and the ability to respond quickly to urgent needs.
6. Pricing and Terms Competitive pricing is important, but it should not compromise quality. Evaluating suppliers based on total cost of ownership, including the durability and lifespan of the wheels, is vital.
Leading Suppliers in the Market
Several established suppliers are recognized for their quality centerless grinder regulating wheels. Here are a few noteworthy names
1. 3M Known for its advanced technology in abrasives and grinding solutions, 3M offers a comprehensive range of regulating wheels designed to improve performance and efficiency in centerless grinding.
2. Norton Abrasives Part of the Saint-Gobain Group, Norton is one of the most recognized brands in the abrasives market. They provide a wide variety of regulating wheels suitable for different applications, ensuring precise and consistent results.
3. Carborundum Universal Limited This company specializes in manufacturing a variety of grinding wheels and related products. With a strong emphasis on quality and innovative designs, Carborundum is a preferred supplier for many manufacturers.
4. Radiac Abrasives A leader in the field of coated and bonded abrasives, Radiac Abrasives offers tailored solutions for centerless grinding applications, ensuring high performance and durability.
5. Abrasive Resource As a dedicated supplier of abrasive products, Abrasive Resource provides a selection of regulating wheels suitable for various grinding operations, along with exemplary customer service and support.
Conclusion
In conclusion, the significance of centerless grinder regulating wheels cannot be overstated, as they are essential for achieving the precision and efficiency required in modern manufacturing. By understanding the key criteria for selecting suppliers and recognizing reputable industry players, manufacturers can ensure they are equipped with the best tools for their operations. As advancements in manufacturing continue to evolve, the importance of high-quality regulating wheels will remain a fundamental aspect of centerless grinding processes.