Understanding Centerless Grinder Rebuild and Its Export Potential
Centerless grinding is a crucial manufacturing process that allows for the precise and efficient machining of cylindrical parts. This method is favored in various industries, including automotive, aerospace, and manufacturing, due to its ability to handle high-volume production while ensuring tight tolerances. In recent years, there has been an increasing demand for centerless grinder rebuilds, leading to a noteworthy trend in exporting these machines and their components.
What is Centerless Grinding?
Centerless grinding is different from traditional grinding methods. In this technique, the workpiece is held between two rotating blades without any central support. One wheel is the grinding wheel that removes material from the surface, while the second is the regulating wheel that controls the speed and direction of the part. This enables the machining of parts to the desired diameter with minimal human intervention.
Importance of Rebuilding Centerless Grinders
Over time, even the most robust centerless grinders will show signs of wear and tear due to continuous operation. This can lead to decreased productivity, increased defect rates, and ultimately, higher operational costs. Rebuilding centerless grinders restores these machines to like-new condition. The process can involve replacing worn-out components, upgrading technology, and enhancing the overall performance of the machine.
One of the primary benefits of rebuilding rather than purchasing new machinery is cost-effectiveness. Purchasing new machinery can involve significant capital outlay, whereas a rebuild can reinvigorate a company's existing assets. Moreover, rebuilt machines can incorporate the latest technological advancements, which increases operational efficiency and the ability to meet production demands.
Market Potential for Rebuild Services
centerless grinder rebuild exporter
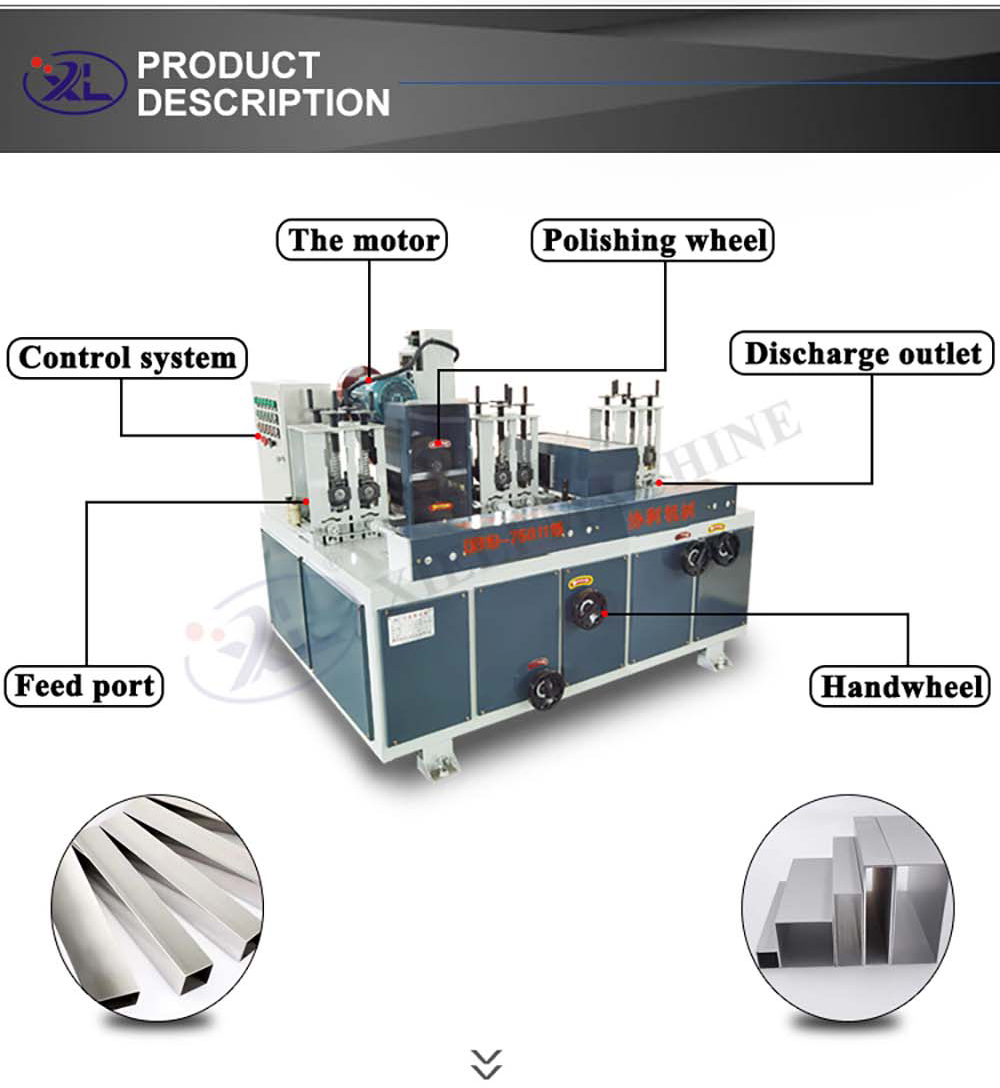
The global manufacturing landscape has seen a growing trend towards sustainability and efficiency. Companies are striving to minimize waste and extend the lifecycle of their equipment, making rebuild services increasingly attractive. As industries continue to optimize their operations, the export market for rebuilt centerless grinders is expanding. Many manufacturers in developing countries seek high-quality rebuilt equipment, which provides a cost-effective solution compared to new machinery.
Additionally, the practice of rebuilding centerless grinders aligns with the principles of the circular economy by extending the life of products and reducing waste. This eco-friendly approach resonates well with the current global emphasis on sustainability, offering rebuilt machines an edge in international markets.
Exporting Rebuilt Centerless Grinders
For exporters, the opportunity to supply rebuilt centerless grinders presents a lucrative market. Practical considerations involve ensuring compliance with international standards and regulations. Quality assurance processes must be in place to guarantee that rebuilt machines meet the demands of foreign clients. This may include acquiring certifications and implementing strict quality control measures throughout the rebuilding process.
Moreover, establishing strong relationships with overseas distributors can facilitate entry into new markets. Understanding the specific needs and preferences of target markets can further enhance the competitiveness of rebuilt machines. Tailoring services and offerings to meet local demands will enhance customer satisfaction and help secure long-term partnerships.
Conclusion
The rebuild of centerless grinders presents an exciting opportunity for manufacturers and exporters alike. As industries continue to evolve toward more sustainable and efficient practices, rebuilt machinery becomes an essential component of this transformation. By prioritizing quality, compliance, and collaboration, businesses can successfully tap into the growing demand for centerless grinder rebuilds on the global stage. With the right strategies in place, the future of exporting rebuilt centerless grinders looks promising, paving the way for enhanced productivity and sustainable manufacturing practices.