Centerless Grinder Precision Grinding A Gateway to Enhanced Productivity and Quality
In the realms of manufacturing, precision is paramount. Products that require exact dimensions and flawless finishes demand the best grinding technology available. Enter the centerless grinder, a sophisticated machine designed for both high precision and efficiency in grinding operations. This technology has revolutionized the way industries approach the grinding of cylindrical parts, making it essential for any modern manufacturing process.
Centerless grinding involves the process of removing material from a workpiece without the need for a spindle or fixture. Instead, the part is supported by a rotating wheel and a blade, allowing for continuous and uninterrupted operation. This unique setup offers several advantages, leading to its widespread adoption in various sectors, including automotive, aerospace, and medical manufacturing.
One of the key benefits of centerless grinding is its ability to handle larger production volumes with remarkable consistency. Unlike traditional grinding methods, which may require more setup time and adjustments, centerless grinding can process multiple pieces simultaneously. This not only increases throughput but also minimizes the risk of human error, enhancing the overall quality of the products being produced.
Precision is another hallmark of centerless grinding. The absence of a spindle means that the parts can be ground to incredibly tight tolerances, often within a few microns. This level of precision is critical for components that need to fit together perfectly in assemblies or for parts that will undergo further machining processes. The grinding wheels can be tailored to meet specific requirements, ensuring that the desired surface finish and dimensions are achieved consistently.
centerless grinder precision grinding products
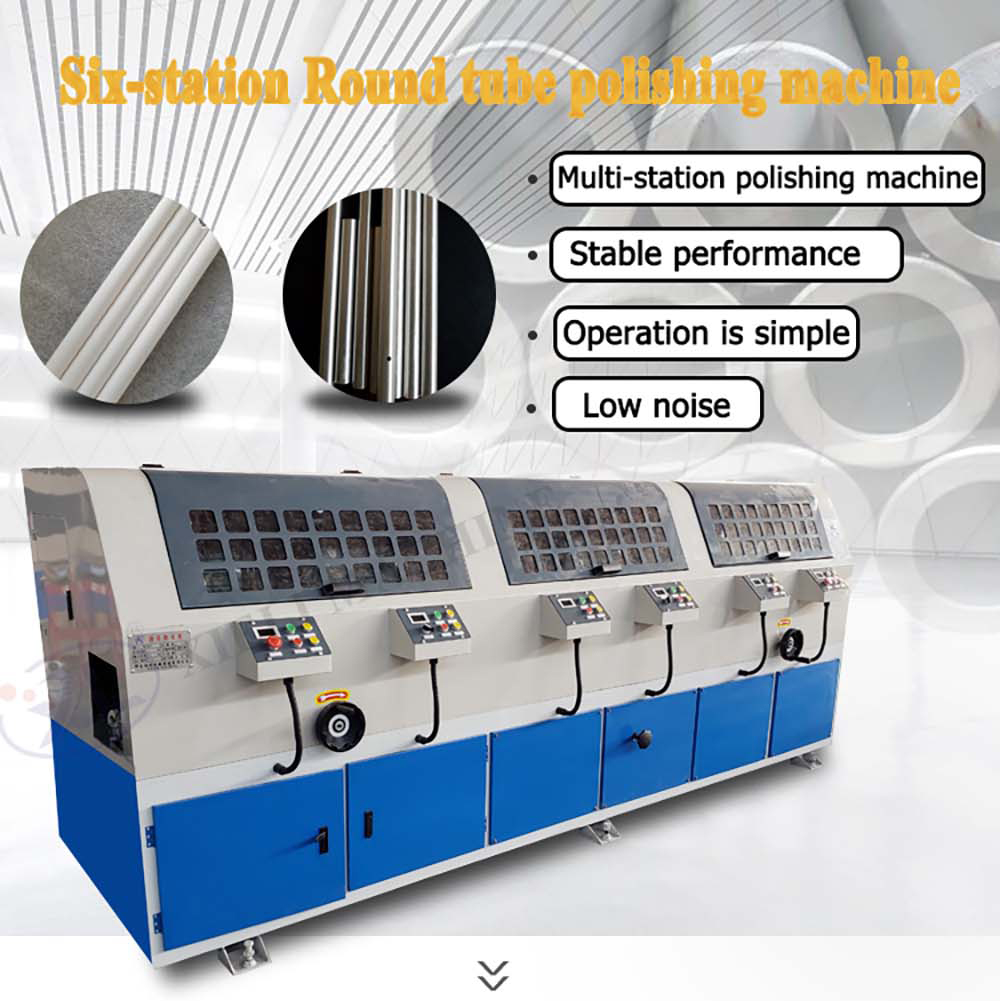
Furthermore, the design of centerless grinders allows for a versatile range of applications. Whether grinding small or large parts, soft or hard materials, these machines can be adapted to various manufacturing needs. From fuel injectors to medical instruments, the ability to grind different shapes and sizes is a testament to the flexibility of centerless grinding processes.
Efficiency is not solely confined to production rates; it also extends to cost-effectiveness. With the enhanced speed and reduced setup times, manufacturers can save on both labor and operational costs. Additionally, the precise nature of centerless grinding can lead to less material waste, as the focus on accuracy helps in utilizing raw materials more effectively. Over time, these savings can substantially benefit the bottom line of an organization.
As industries continue to evolve and demand greater precision, the role of centerless grinders becomes increasingly vital. Manufacturers that invest in advanced centerless grinding technologies position themselves to meet growing market demands while maintaining high standards of quality and efficiency. Through continual innovation and improvements in grinding processes, companies can harness the power of precision grinding to enhance their competitive edge.
In conclusion, centerless grinder precision grinding is a hallmark of modern manufacturing, enabling high-speed, high-accuracy production of cylindrical parts. Its advantages make it an invaluable asset across numerous industries, shaping the future of precision engineering and manufacturing efficiency.