Centerless Grinder Machines The Backbone of Precision Manufacturing
In the world of precision manufacturing, the importance of efficient and accurate machinery cannot be overstated. Among the various types of equipment available, centerless grinder machines stand out as indispensable tools for achieving high precision in the production of cylindrical parts. These machines are not only time-efficient but also capable of delivering exceptional tolerances, making them an attractive choice for a variety of industries.
How Centerless Grinding Works
Unlike traditional grinding machines that utilize a fixed spindle, centerless grinders do not require the workpiece to be centered between two grinding wheels. Instead, the workpiece is supported by a work rest blade and is held in place by the grinding wheels, which are set at specific angles. This unique arrangement allows for continuous feeding of parts, leading to significantly higher productivity compared to other grinding methods.
The two main types of centerless grinding are through-feed and in-feed grinding. In through-feed grinding, the part is fed through the machine and exits out the other end after being ground. This is ideal for long, cylindrical pieces. In contrast, in-feed grinding is used for shorter and more complex shapes that require a more precise approach. Each system has its advantages, depending on the specific needs of the project.
Advantages of Centerless Grinding
One of the primary advantages of centerless grinding is its ability to produce highly uniform and precise parts quickly. Tolerances as tight as ±0.0001 inches can be achieved, making it suitable for industries where accuracy is paramount, such as aerospace, automotive, and medical manufacturing.
centerless grinder machines quotes
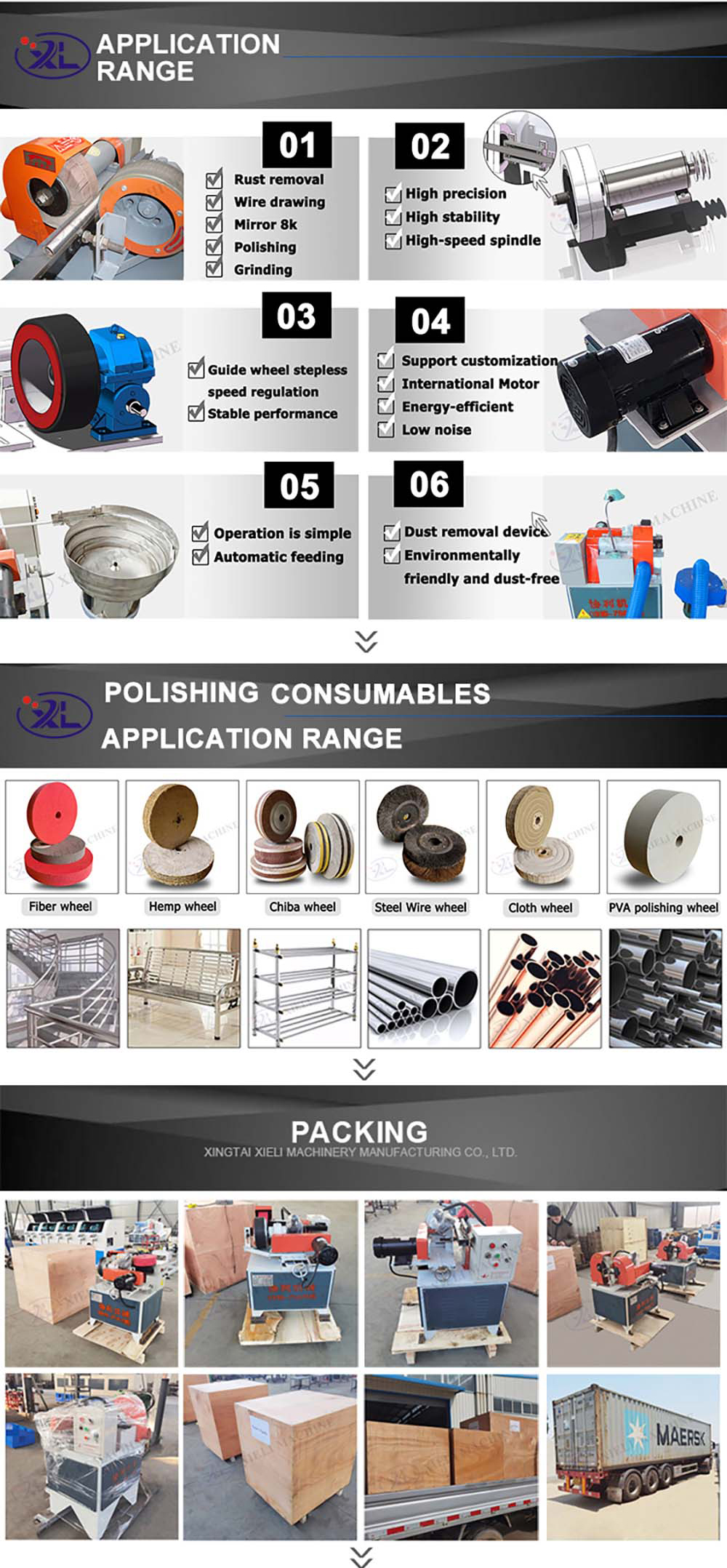
Moreover, centerless grinding machines can process a wide range of materials, including metals, plastics, and composites. This versatility is crucial, as manufacturers often require different materials for different applications. Additionally, the setup time for centerless grinding machines is relatively short, allowing for quick transitions between job types.
Economic Benefits
Investing in centerless grinding technology can yield substantial economic benefits. The high throughput and reduced cycle times result in lower labor costs, while the precision of the parts produced minimizes waste and rework. Over time, these factors contribute to a significant return on investment, making centerless grinders a financially sound choice for manufacturers.
Choosing the Right Centerless Grinder
When considering the purchase of a centerless grinder, it is essential to evaluate your specific manufacturing needs. Factors such as the type of material being processed, the size and shape of the parts, and the desired tolerances should all influence your decision. Additionally, it's crucial to select a reputable supplier that offers robust customer support and maintenance services.
Conclusion
Centerless grinder machines play a vital role in modern manufacturing by providing efficient, accurate, and cost-effective grinding solutions. Their ability to produce high-precision cylindrical parts makes them an essential asset in various industries. As manufacturers continue to seek efficiency and quality, understanding the benefits and applications of centerless grinding will undoubtedly play a crucial role in driving innovation and success in the manufacturing sector. With the right machinery and expertise, businesses can harness the full potential of centerless grinders to stay competitive in the ever-evolving market landscape.