The Centerless Grinder Revolutionizing the Precision Grinding Process
In the realm of manufacturing, precision is paramount. Engineers and manufacturers continually seek methods to produce components that meet stringent tolerances while maximizing efficiency and reducing waste. One machine that plays a pivotal role in achieving this goal is the centerless grinder. This innovative machining tool has transformed the way we approach grinding, providing a solution that enhances accuracy and streamlines production processes.
Understanding Centerless Grinding
Centerless grinding differs markedly from traditional cylindrical grinding. In a conventional setup, the workpiece is held between two centers, which necessitates precise alignment and setup that can be time-consuming. Conversely, centerless grinding utilizes two wheels a grinding wheel and a regulating wheel. The workpiece is placed between these wheels, which means it does not need to be held in place by centers. This design allows for continuous operation and improved throughput, as multiple parts can be fed into the grinder without the need for complex positioning.
Key Components and Operation
At the heart of the centerless grinder are the grinding wheel, which removes material from the workpiece, and the regulating wheel, which controls the speed and feed of the workpiece as it passes through the machine. The workpiece sits on a horizontal plane, supported by a blade or a support column. As the grinding wheel revolves, it grinds the outer diameter of the workpiece while the regulating wheel guides it smoothly along its path.
This configuration eliminates many of the inherent challenges seen in other grinding methods. For instance, the centerless process can accommodate various shapes, sizes, and materials, making it an incredibly versatile option for manufacturers. Whether producing small precision components for the automotive industry or larger parts for machinery, the centerless grinder adapts to deliver the required finish and dimensional accuracy.
Advantages of Centerless Grinding
One of the most significant advantages of centerless grinding is its efficiency. Because the parts do not require initial positioning, the setup time is significantly reduced, allowing for quick transitions between different tasks. This not only speeds up production but also minimizes downtime, making it an ideal choice for high-volume manufacturing.
centerless grinder
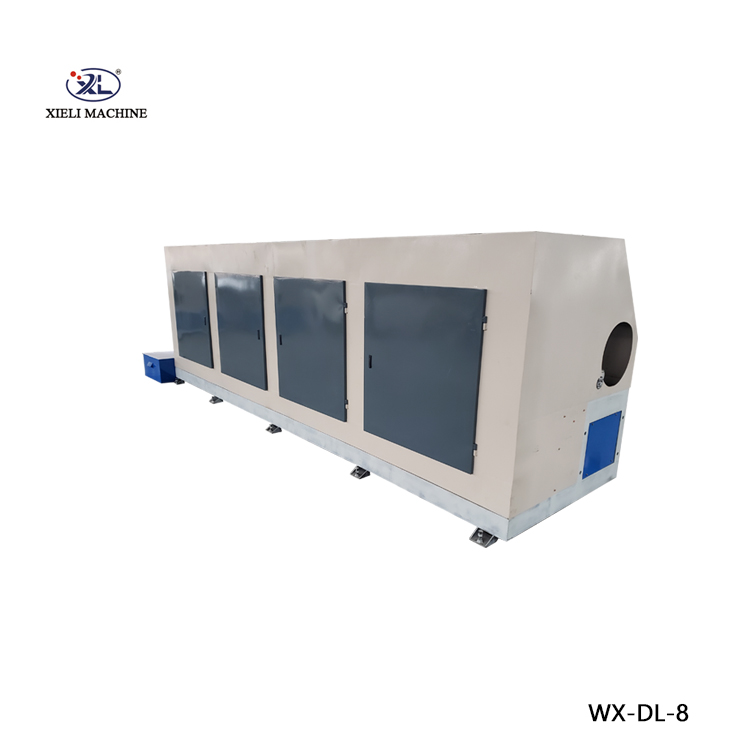
Moreover, centerless grinders produce a superior surface finish compared to other grinding methods. The continuous contact between the workpiece and the grinding wheel ensures consistent material removal, resulting in smoother surfaces and tighter tolerances. This precision is vital in industries such as aerospace, automotive, and medical devices, where even the smallest deviation can lead to catastrophic failures.
Additionally, centerless grinding generates less waste due to its ability to remove material more effectively. The process can often recycle scrap material, reducing costs and promoting sustainability in manufacturing.
Applications and Industries
The applications of centerless grinders are vast and varied. In the automotive industry, they are essential for producing components such as fuel injector bodies, camshafts, and roller bearings. In the aerospace sector, centerless grinding is used for manufacturing turbine shafts and landing gear components, where strength and precision are critical.
Moreover, the medical field benefits greatly from centerless grinding technology. Surgical instruments, implants, and other critical devices require impeccable surface finishes and precise dimensions—attributes that centerless grinders easily deliver.
Conclusion
As industries continue to evolve and demand for precision manufacturing increases, the centerless grinder stands out as a quintessential machine at the forefront of technological advancement. By providing unmatched efficiency, versatility, and precision, centerless grinding has revolutionized the manufacturing landscape, paving the way for innovations in various sectors.
Investing in centerless grinding technology is not merely an operational decision; it is a strategic move towards achieving excellence in production processes. As manufacturers look to the future, centerless grinders are poised to play an increasingly pivotal role in shaping the manufacturing techniques of tomorrow, ensuring that the highest standards of quality and efficiency are met.