Understanding Centerless Cylindrical Grinding Machine Factories
Centerless cylindrical grinding is a machining process that is widely used in various industries, particularly in the manufacturing of precision components. This method is essential for producing parts with tight tolerances and smooth finishes, making it a preferred choice for components like shafts, rods, and bearings. Centerless grinding machines have become indispensable in factories specializing in high-volume production, as they streamline the grinding process and significantly boost productivity.
At the heart of a centerless grinding machine’s functionality is the principle of centerless grinding. Unlike traditional cylindrical grinding, where the workpiece is held between two centers, centerless grinding utilizes a different approach. The workpiece is positioned between a grinding wheel and a regulating wheel. The grinding wheel performs the cutting action, while the regulating wheel controls the rotational speed and can also contribute to the workpiece's axial positioning. This design eliminates the need for additional fixtures or tooling, allowing for rapid setup and easy adjustments.
Several factories specialize in manufacturing centerless cylindrical grinding machines. These facilities are often equipped with advanced technologies that enhance the precision and efficiency of the grinding process. Such factories typically focus on the following critical aspects
1. Engineering Excellence Factories that produce centerless grinding machines emphasize the importance of engineering design. The precision of these machines is a direct reflection of the engineering principles applied during their design and manufacturing. By employing skilled engineers and utilizing sophisticated design software, these factories can create machines that meet the specific needs of their customers.
2. High-Quality Materials The durability and performance of centerless grinding machines depend significantly on the quality of materials used in their construction. Factories ensure that high-grade steel and other robust materials are employed to withstand the rigors of grinding operations while providing longevity and reliability.
centerless cylindrical grinding machine factories
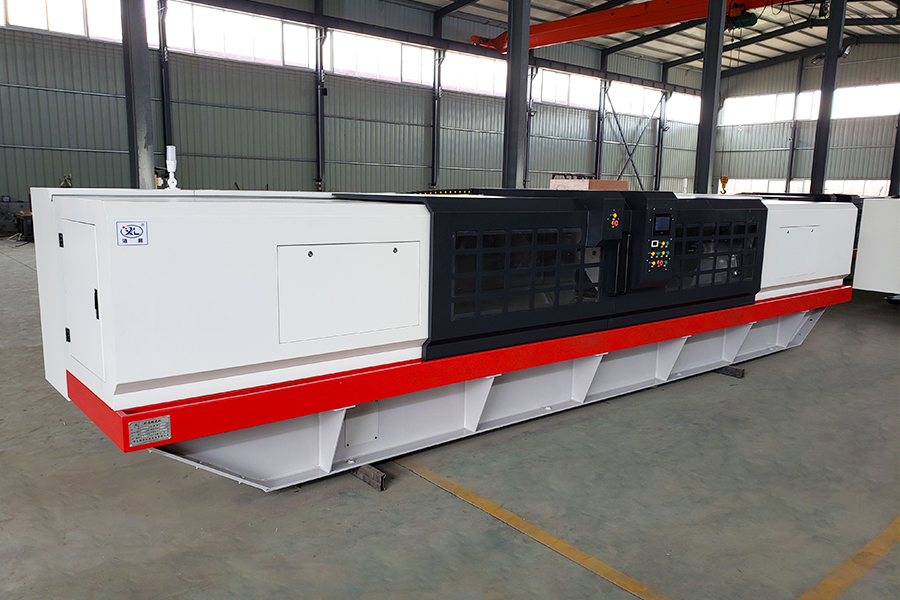
3. Cutting-Edge Technology Automation and computerization have revolutionized the manufacturing of centerless grinding machines. Incorporating CNC (Computer Numerical Control) technology allows for precise control of grinding parameters, resulting in better consistency and accuracy. Factories invest in the latest technology to offer advanced machines that can handle complex grinding tasks.
4. Customization Due to the diverse needs of various industries, many factories offer customization options. Depending on the specifications of the components being manufactured, businesses can request tailored solutions, ensuring that the grinding machine fits seamlessly into their production line.
5. Focus on Sustainability In today’s eco-conscious climate, many factories also prioritize sustainable practices in their operations. This includes reducing waste during manufacturing, recycling materials, and designing machines to consume less energy.
The demand for precision-engineered components is on the rise, especially in sectors like automotive, aerospace, and medical. Therefore, the role of factory-produced centerless cylindrical grinding machines is increasingly significant. They not only help in achieving high production rates but also ensure that the manufactured parts meet stringent quality standards.
In conclusion, centerless cylindrical grinding machine factories play a vital role in the manufacturing landscape. By focusing on engineering excellence, high-quality materials, cutting-edge technology, customization, and sustainability, these factories are well-equipped to meet the evolving needs of industry. As the demand for precision components continues to grow, centerless grinding machines will remain a cornerstone of modern manufacturing, enabling businesses to forge ahead in an increasingly competitive market.