The Evolution of Centerless Cylindrical Grinding Machines A Key Player in Precision Manufacturing
In the world of precision manufacturing, few processes are as critical as cylindrical grinding. Among the various types of grinding machines, centerless cylindrical grinding machines hold a prominent position. These sophisticated machines are designed to provide exceptional efficiency and accuracy in shaping cylindrical workpieces without requiring a central axis for support. They have become essential tools for industries ranging from automotive to aerospace, and their evolution continues to shape the manufacturing landscape.
Centerless cylindrical grinding machines operate on a unique principle that allows for the continuous production of parts without the need for clamping fixtures. Unlike traditional cylindrical grinders that require the workpiece to be mounted between centers, centerless grinders use a combination of wheels—namely, a grinding wheel and a regulating wheel—to hold and rotate the workpiece. This configuration allows for high-speed removal of material and offers a multitude of advantages over conventional methods.
One of the primary benefits of centerless cylindrical grinding is its ability to handle long and short workpieces alike. This versatility makes it an ideal choice for manufacturers producing items like shafts, pins, and bearings. With the growing demand for precision-engineered components, a company specializing in centerless cylindrical grinding machines can cater to a wide range of industries by providing solutions tailored to unique specifications.
Moreover, the design of centerless grinders contributes significantly to their operational efficiency. With no need for complex set-ups associated with traditional grinding methods, manufacturers can achieve quicker turnaround times and higher throughput. The continuous operation minimizes the need for extensive cycle times, empowering organizations to meet strict deadlines while maintaining high-quality standards.
centerless cylindrical grinding machine company
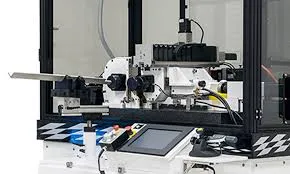
As technology continues to advance, so too does the functionality of centerless cylindrical grinding machines. The integration of computer numerical control (CNC) technology has revolutionized the manufacturing process, allowing for precise control over grinding parameters. This enhancement not only improves accuracy but also enables manufacturers to produce complex geometries that were once difficult or impossible to achieve. The adaptability of CNC centerless grinders means that companies can expand their offerings and tackle more intricate projects with confidence.
In addition to technological advancements, the material selection for grinding wheels has improved. High-performance abrasives can deliver superior grinding efficiency, reducing the overall wear on machinery and increasing the lifespan of the tools. Companies that focus on innovation in grinding technology are consistently researching and developing new materials that elevate the performance of centerless cylindrical grinding machines. This research ensures that manufacturers can keep pace with the ever-evolving demands of their industries.
Environmental considerations have also become a driving force in the evolution of centerless cylindrical grinding machines. With a growing emphasis on sustainability, manufacturers are developing machines that minimize waste and energy consumption. Enhanced coolant systems not only improve the longevity of the grinding wheels but also reduce the environmental impact by ensuring effective recycling of coolant fluids.
Furthermore, the rise of Industry 4.0 and the Internet of Things (IoT) has initiated a new chapter for centerless cylindrical grinding machines. With smart technology, manufacturers can monitor the performance of their machines in real-time, anticipate maintenance needs, and optimize production schedules. This connectivity fosters a more agile manufacturing environment and contributes to the overall efficiency of operations.
In conclusion, centerless cylindrical grinding machines represent a crucial element in the realm of precision manufacturing. Their unique operating principles, coupled with ongoing advancements in technology and materials, have solidified their status as a vital asset for various industries. As manufacturers continue to pursue greater efficiency and precision, the role of centerless cylindrical grinding will only expand. Companies that specialize in this domain will undoubtedly play a key role in shaping the future of manufacturing, ensuring that quality and innovation remain at the forefront of production processes. Whether through the adoption of cutting-edge technologies or sustainable practices, the journey of centerless cylindrical grinding machines is one of continuous evolution, reflecting the ever-changing landscape of the manufacturing world.