Centerless Grinder with a Surface Grinder A Comprehensive Overview
In the world of precision machining, the demand for accurate and efficient tools is paramount. Among the various machines employed in manufacturing environments, centerless grinders, often used in conjunction with surface grinders, stand out for their ability to produce high-quality components with minimal operator intervention. This article delves into the significance of centerless grinders paired with surface grinders, exploring their functions, advantages, and the role of suppliers in delivering these essential machines.
Understanding Centerless Grinding
Centerless grinding is a machining process that involves the grinding of a workpiece without the need for a center or fixture. Unlike traditional grinding methods, where the workpiece is held between centers, centerless grinding employs a unique setup whereby the workpiece is supported by a work blade and rotated by a regulating wheel. This allows for continuous and high-speed production of cylindrical parts with tight tolerances.
One of the key benefits of centerless grinding is its ability to process a wide range of materials, including metals and plastics. This versatility is essential for manufacturers that require parts made from different materials without significant changes in setup. Moreover, centerless grinding enhances productivity, as it can achieve high throughputs and rapidly process multiple parts simultaneously.
The Role of Surface Grinders
Surface grinders complement centerless grinders by focusing on the flat surfaces of workpieces. They employ a rotating abrasive wheel to remove material from the surface of a part, achieving a smooth finish and precise dimensions. Surface grinders are best suited for applications where flatness and surface quality are crucial, making them indispensable in industries such as automotive, aerospace, and mold manufacturing.
centerless grinder with a surface grinder suppliers
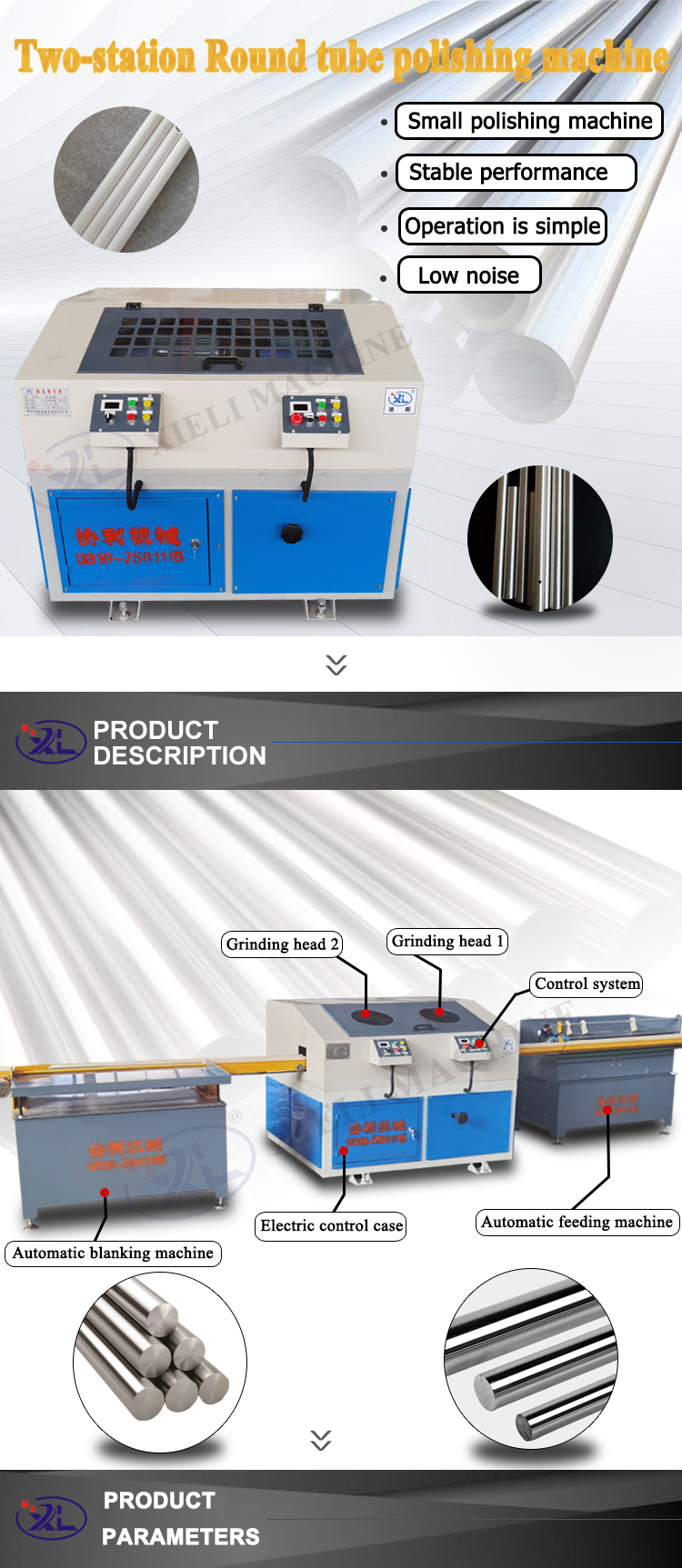
When centerless grinders and surface grinders are used together in a manufacturing process, they create a powerful duo. The centerless grinder can efficiently shape and size the raw material into cylindrical forms, while the surface grinder can be employed to finish those components to the desired flatness and smoothness. This synergy not only enhances productivity but also increases the overall quality of the finished products.
Supplier Selection
As the demand for precision grinding machines continues to rise, selecting the right supplier for centerless and surface grinders becomes critical. An effective supplier should not only provide high-quality machines but also offer support services, including maintenance, training, and spare parts availability.
Companies looking to integrate centerless and surface grinding into their operations should consider suppliers with a proven track record in the industry. This includes evaluating the supplier’s range of machines, customer reviews, and their ability to provide customized solutions tailored to specific manufacturing needs. Additionally, suppliers who offer advanced technology, such as CNC-controlled grinders, can significantly improve the efficiency and accuracy of the grinding process.
Conclusion
The integration of centerless grinders with surface grinders is a strategic move for manufacturers seeking to enhance productivity and quality. By understanding the advantages of each machining process and the critical role suppliers play in this ecosystem, businesses can optimize their operations and meet the demands of modern manufacturing. Choosing the right equipment and supplier ensures that manufacturers can produce high-quality parts that meet stringent industry standards, ultimately driving success in a competitive market.