Troubleshooting Centerless Grinder Issues A Guide for Manufacturers
Centerless grinding is an essential process in many manufacturing sectors, renowned for its efficiency and ability to produce high-precision components. However, like any industrial equipment, centerless grinders can encounter issues that disrupt operations. Understanding how to troubleshoot these problems can save time, costs, and ensure optimal performance. This article outlines common issues faced by manufacturers and offers solutions.
1. Misalignment of Components
One of the most common problems in centerless grinding is the misalignment of the workpiece, regulating wheel, or grinding wheel. Misalignment can lead to uneven grinding, resulting in parts that don’t meet specifications.
Solution Regularly check and adjust the alignment of the wheels and workpiece. Use an alignment gauge to ensure that both the grinding wheel and regulating wheel are parallel to each other and properly positioned. This may require realigning the machine setup before each batch of operations.
2. Wheel Wear and Deterioration
Grinding wheels are subject to wear and tear over time, which affects their performance and can lead to reduced productivity. Dull wheels can create excessive heat, affecting the material properties of the workpiece.
Solution Keep an eye on the condition of the grinding wheels. Implement a routine inspection schedule and replace or re-dress the wheels as necessary. Using a proper coolant can also reduce wear on the wheels and enhance their cutting capabilities.
3. Vibration Issues
Vibration can result from several factors, including an imbalance in the machine setup, worn bearings, or even improper tool sharpening
. Excessive vibration impacts surface finish and may damage both the workpiece and the machine.centerless grinder troubleshooting manufacturers
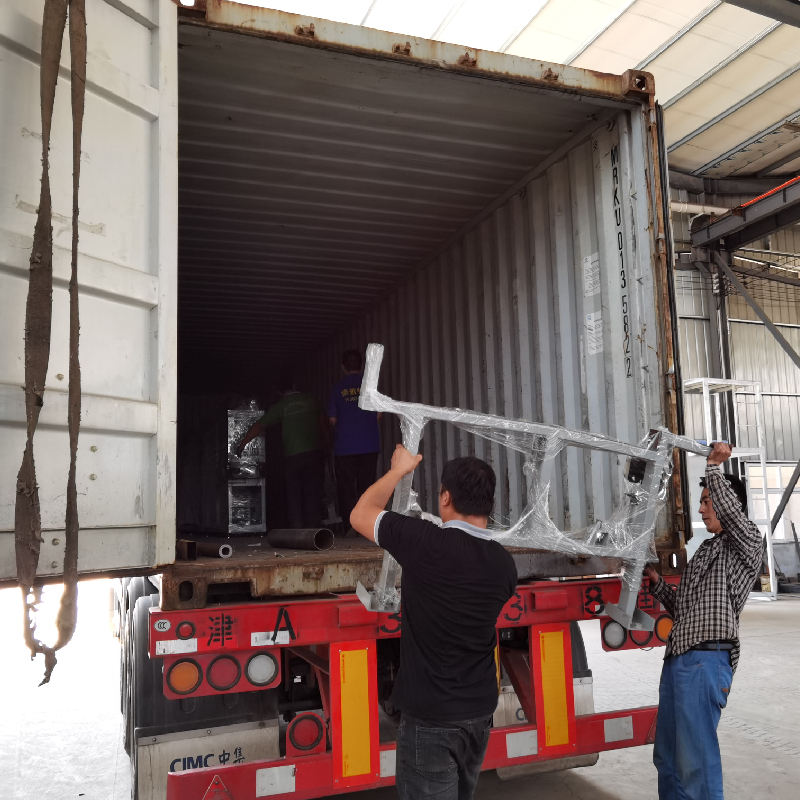
Solution To mitigate vibration, ensure that the machine is installed on a stable, level surface. Check for any loose components and secure them properly. It may also be necessary to replace worn bearings or adjust the balance of the setup to reduce vibrational impacts.
4. Cooling Problems
Inadequate cooling during the grinding process can lead to overheating, impacting both the grinder's performance and the quality of the finished product. Insufficient coolant can cause excessive wear on the grinding wheel and thermal distortion of the workpiece.
Solution Ensure that the coolant system is functioning effectively. Regularly check coolant levels and quality, and review the coolant flow rate to ensure optimal circulation. Employing the right type of coolant for the materials being processed can also significantly enhance grinding efficiency.
5. Electrical Issues
Electrical faults, such as blown fuses, erratic power supply, or faulty control systems, can hamper operations and lead to sudden stoppages.
Solution Regularly inspect electrical connections and components for wear or damage. Keeping a maintenance log for potential electrical issues can help foresee problems before they escalate. It's also a good practice to have a qualified technician review the electrical system periodically.
Conclusion
Efficient centerless grinding relies on meticulous maintenance and troubleshooting practices. By addressing common issues like misalignment, wheel wear, vibration, cooling problems, and electrical faults, manufacturers can enhance their operational efficiency and product quality. Regular training for staff on troubleshooting techniques and a commitment to preventive maintenance can ensure the longevity of centerless grinders in any manufacturing environment.