Understanding Centerless Grinder Regulating Wheels
Centerless grinding is a machining process that produces smooth and precise cylindrical parts. One of the critical elements in this process is the regulating wheel, which plays a pivotal role in controlling the speed and movement of the workpiece as it passes through the grinding system. In this article, we’ll delve into the importance of regulating wheels, their characteristics, and how proper selection can enhance grinding efficiency.
What are Regulating Wheels?
In a centerless grinding setup, there are typically three main components the grinding wheel, the regulating wheel, and the workpiece support. The grinding wheel is responsible for removing material from the workpiece, while the regulating wheel controls the speed and infeed of the workpiece as it moves through the grinding zone. This unique configuration allows the workpiece to be machined without any need for proper clamping, providing a significant advantage in terms of productivity and efficiency.
Key Characteristics
Regulating wheels are characterized by their diameter, hardness, and surface texture
. These characteristics can significantly affect the grinding process1. Diameter The diameter of the regulating wheel typically influences the speed at which the workpiece is fed into the grinding wheel. Smaller diameters will result in slower feed rates, while larger diameters can facilitate faster feeding.
centerless grinder regulating wheels quotes
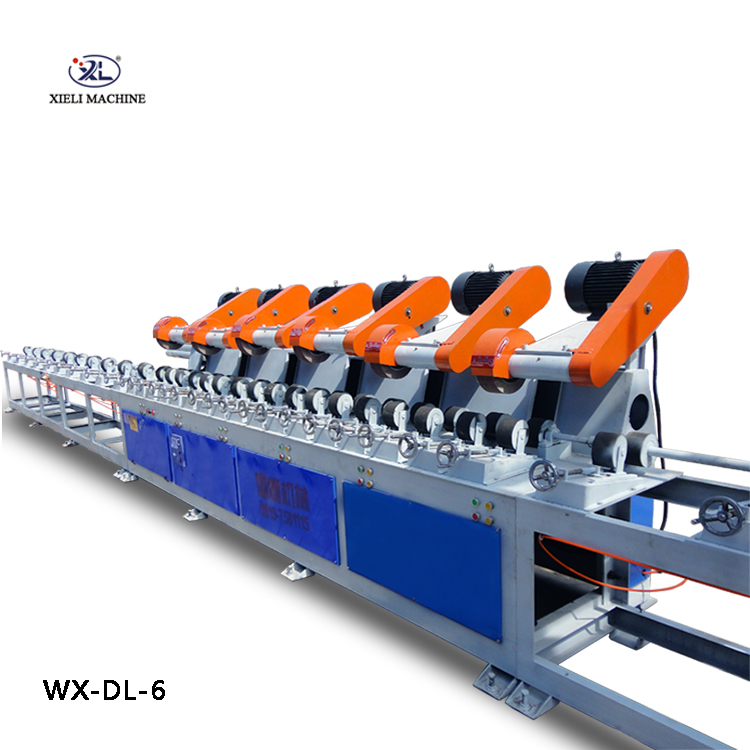
2. Hardness The hardness of a regulating wheel is critical for its longevity and effectiveness. A harder wheel may wear less quickly but may not provide sufficient friction if not matched appropriately with the workpiece material.
3. Surface Texture The surface texture of the regulating wheel also plays a significant role in the grinding process. A rougher surface can provide better grip on the workpiece, offering stability during the grinding operation.
The Importance of Proper Selection
Choosing the right regulating wheel is essential for optimizing the grinding operation. Incorrect selection can lead to issues such as a decreased material removal rate, increased wear on the grinding wheel and workpiece, and poor surface finish quality. Factors to consider when selecting a regulating wheel include the type of material being ground, the desired surface finish, and the specific application requirements.
For example, in applications where tight tolerances and high surface quality are paramount, a harder, finer-textured regulating wheel may be preferred, while in high-volume production scenarios, a more robust wheel might be necessary to handle the demands of repetitive cycles.
Conclusion
In summary, regulating wheels are an integral part of the centerless grinding process, affecting not only the efficiency of machining operations but also the quality of the final product. By understanding their characteristics and the significance of selecting the appropriate wheel for specific applications, manufacturers can enhance their grinding processes, improve product quality, and ultimately achieve better operational efficiency. Whether you are in a high-precision manufacturing environment or dealing with larger production runs, the right choice in regulating wheels can make all the difference in optimizing your machining performance.