Understanding the Importance of Coolant in Centerless Grinding
Centerless grinding is a machining process that utilizes a rotating grinding wheel to remove material from a workpiece. Unlike traditional grinding, where the workpiece is supported by fixtures on either side, centerless grinding allows for the workpiece to be fed through the grinding wheel without any direct mechanical support. This unique process requires careful control of several variables, one of the most crucial being the coolant used during machining.
The Role of Coolant in Centerless Grinding
Coolants in centerless grinding serve multiple purposes, primarily to reduce heat buildup, enhance surface finish, and prolong the lifespan of the grinding wheel. The grinding process generates a significant amount of heat due to the friction between the grinding wheel and the workpiece. Without effective cooling, this heat can damage both the workpiece and the grinding wheel, leading to inefficient grinding and compromising the quality of the finished product.
Types of Coolants for Centerless Grinding
There are various types of coolants that can be utilized in centerless grinding. These include water-based coolants, oil-based coolants, and synthetic coolants. Each type has its advantages and disadvantages
1. Water-Based Coolants These are generally the most commonly used due to their effective cooling properties and cost efficiency. They often contain additives to improve lubricity and prevent rust. However, water-based coolants can lead to corrosion if not properly managed.
2. Oil-Based Coolants Offering excellent lubrication, oil-based coolants can significantly enhance surface finish. However, they tend to be more expensive than water-based options and may pose environmental and health risks due to increased volatility.
buy centerless grinder coolant
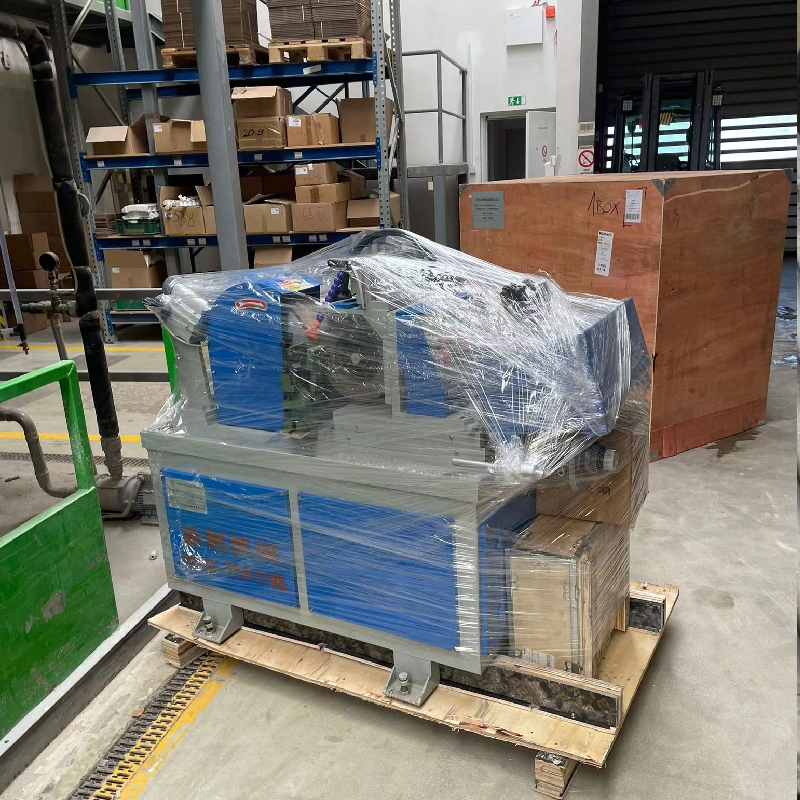
3. Synthetic Coolants These coolants combine the benefits of both water-based and oil-based coolants. They are formulated to provide cooling without the environmental impact of traditional oils, making them a popular choice for modern machining operations. Synthetic coolants can also offer extended tool life and resist bacteria growth, which is an important consideration for maintaining a clean machining environment.
Choosing the Right Coolant
When selecting a coolant for centerless grinding, several factors must be taken into account, including the material being machined, the type of grinding wheel, and the specific operational requirements of the machine. It's essential to conduct thorough research and possibly run trials to determine which coolant provides the best results for a particular application.
Maintenance and Management
The performance of the chosen coolant can significantly impact the efficiency of the grinding process. Regular monitoring and maintenance of coolant concentration and cleanliness are vital to ensure optimal performance. This includes
- Regularly checking coolant concentration using refractometers to maintain the correct dilution. - Filtering coolants to remove chips and residues, thus extending its life and effectiveness. - Periodic replacement of coolant to avoid contamination and degradation, which can adversely affect machining quality.
Conclusion
In summary, the selection and management of the right coolant in centerless grinding is crucial for achieving superior machining results. It affects not only the quality of the finished product but also the efficiency of the grinding process and the longevity of the equipment. By understanding the various types of coolants available, their respective benefits, and the importance of proper maintenance, manufacturers can optimize their centerless grinding operations and achieve better productivity and quality. Investing time and resources into coolant selection and management is a strategic move for any business involved in precision machining.