The Best Surface Grinder and Centerless Grinding An Overview
In the realm of precision machining and metalworking, surface grinding and centerless grinding are two pivotal processes that ensure high-quality finishes and tight tolerances on various components. Understanding their differences and applications can help manufacturers choose the best equipment for their specific needs. This article explores the best surface grinders and the importance of centerless grinding in modern manufacturing.
Surface Grinders Key Features and Functions
Surface grinders are essential machines used in manufacturing for producing flat surfaces on workpieces. They operate by using a rotating grinding wheel to remove material from the workpiece's surface, allowing for the attainment of precise dimensions and finishes. The best surface grinders are characterized by their rigidity, precision, and versatility. Features that stand out include
1. Precision Control High-end surface grinders come equipped with advanced CNC controls, enabling operators to set exact profiles and dimensions for consistent results.
2. Versatile Wheel Options The ability to use different types of grinding wheels, such as coarse or fine grit, enhances the surface grinder's functionality, allowing it to handle various materials and finishes.
3. Robust Construction A durable build ensures longevity and reliability, minimizing vibrations that can affect the grinding process.
Centerless Grinding An Essential Manufacturing Process
best surface grinder centerless grinding
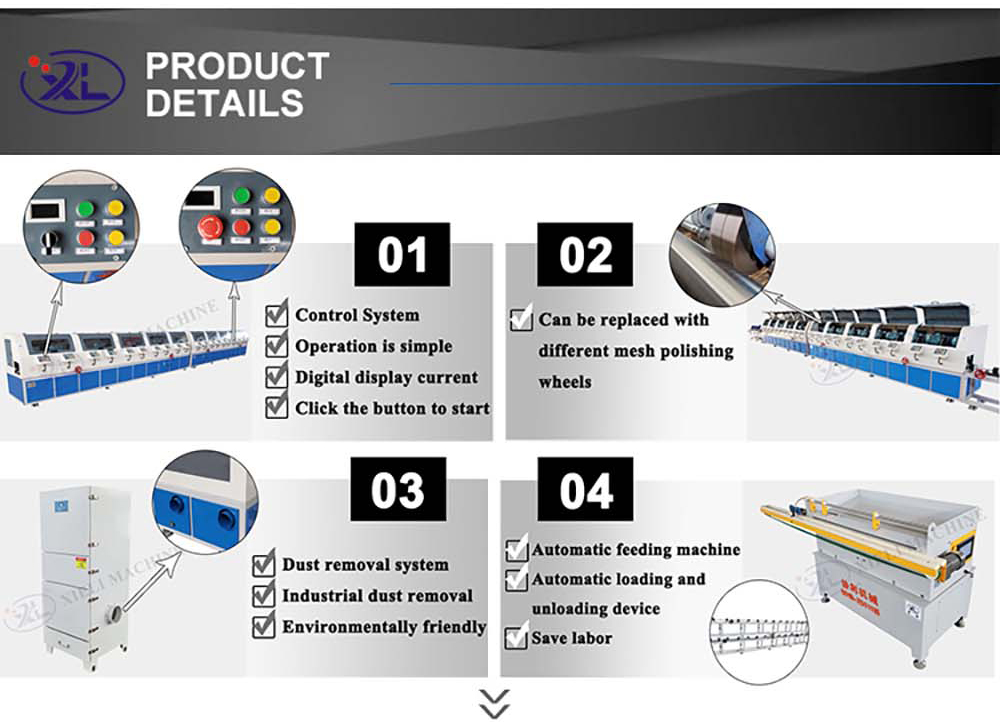
Centerless grinding is a process used to grind cylindrical parts that do not require the workpiece to be mounted between centers. This method is particularly beneficial for high-volume production runs, as it allows for continuous grinding without the need for manual setup. The key advantages of centerless grinding include
1. High Efficiency Centerless grinding can process cylindrical parts at high speed, significantly reducing cycle times compared to traditional grinding methods.
2. Consistent Finish and Precision The machine's design ensures that the workpiece is held in place during the grinding process, leading to enhanced precision and surface finish uniformity.
3. Minimal Setup Requirements Unlike conventional grinding, centerless grinding does not require complex setups, as parts can be fed continuously into the machine, making it ideal for mass production.
4. Flexibility Centerless grinding machines can accommodate various workpiece sizes and shapes, making them versatile for different applications.
Choosing the Right Equipment
When considering the best surface grinder or centerless grinding machine for your operations, several factors must be taken into account. These include the types of materials you will be working with, the volume of production required, and the specific tolerances and finishes you need to achieve. Researching reputable manufacturers and reviewing user feedback can also help in making an informed decision.
Conclusion
Both surface grinders and centerless grinding machines play crucial roles in the manufacturing process. While surface grinders excel in providing precise flat surfaces, centerless grinders offer unmatched efficiency and consistency for cylindrical components. Understanding the capabilities and features of each type of machine is essential for manufacturers looking to invest in the best equipment for their machining needs. By doing so, they can enhance production quality, reduce lead times, and ultimately meet the demands of a competitive market. Whether for a small workshop or a large manufacturing facility, selecting the right grinding technology will drive success in the precision machining landscape.