The Role of AS9100 Certified Centerless Grinders in Aerospace Manufacturing
In the aerospace industry, precision and reliability are paramount. Every component used in aircraft and spacecraft must meet stringent quality standards to ensure safety and performance. One of the key processes in manufacturing these components is grinding, specifically centerless grinding. The integration of AS9100 certified centerless grinders elevates this process, ensuring that manufacturers deliver top-quality products that adhere to industry standards.
Understanding Centerless Grinding
Centerless grinding is a process that allows for the precise machining of cylindrical parts. Unlike traditional grinding methods, which rely on centers to hold the workpiece, centerless grinding supports the workpiece between a grinding wheel and a regulating wheel. This setup enables continuous and efficient production, making it a preferred choice in the manufacturing of aerospace components. The process is highly versatile and can accommodate a range of materials, allowing manufacturers to produce intricate designs with minimal tolerances.
The Importance of AS9100 Certification
AS9100 is a widely recognized quality management standard specifically tailored for the aerospace industry. It emphasizes the importance of risk management, continuous improvement, and stakeholder engagement in the manufacturing process. An AS9100 certification ensures that a company adheres to these essential guidelines, enhancing their credibility and the quality of their products.
When it comes to centerless grinding, having AS9100 certified equipment signifies that the machines meet stringent international quality standards. This certification involves rigorous assessments and audits to verify that the manufacturing processes are consistently monitored and controlled, resulting in reliable and high-quality outputs.
Benefits of Using AS9100 Certified Centerless Grinders
as9100 centerless grinder exporter
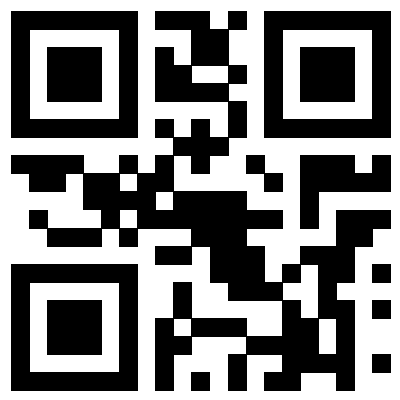
1. Enhanced Quality Assurance AS9100 certified centerless grinders integrate advanced quality control measures, ensuring that every part produced meets the exacting standards of the aerospace industry. This leads to fewer defects and rejections in the production process.
2. Increased Efficiency The centerless grinding process is designed for high-volume production. When combined with AS9100 certification, it maximizes operational efficiency while minimizing waste and production costs, making it a cost-effective solution for manufacturers.
3. Compliance with Industry Standards Aerospace manufacturers are required to comply with numerous regulations and specifications. Utilizing AS9100 certified equipment helps ensure compliance with various industry standards, which is critical for maintaining contracts and certifications with regulatory bodies.
4. Continuous Improvement AS9100 promotes a culture of continuous improvement within organizations. This mindset encourages manufacturers to constantly seek ways to optimize their grinding processes, leading to innovations that benefit product quality and overall operational efficiency.
5. Customer Satisfaction With every component meeting the high standards set forth by AS9100, customer trust is enhanced. Aerospace companies are more likely to forge long-term relationships with suppliers who can guarantee quality and reliability, which ultimately drives business growth.
Conclusion
The integration of AS9100 certified centerless grinders in aerospace manufacturing is a strategic investment towards achieving the highest quality standards. As the demand for precise and reliable components continues to rise, manufacturers equipped with these certified machines are well-positioned to meet the challenges of the industry. The combination of advanced grinding technology and robust quality management systems not only ensures the production of superior parts but also fosters innovation and customer satisfaction in the highly competitive aerospace sector. Manufacturers aiming for success must recognize the importance of quality certifications such as AS9100 and the role of centerless grinding in delivering the reliability and performance that the aerospace industry demands.