Understanding Abbreviations for Centerless Grinder Products
Centerless grinding is a manufacturing process that has gained significant importance in various industries due to its efficiency and precision in producing cylindrical parts. As technology advances, so too does the terminology associated with the machines and products involved. This article aims to elucidate the various abbreviations commonly used in the realm of centerless grinding products, ensuring that both newcomers and seasoned professionals can navigate this specialized field with confidence.
The Basics of Centerless Grinding
Before delving into abbreviations, it's essential to understand what centerless grinding entails. Unlike traditional grinding methods, centerless grinding does not require the part to be fixed in a chuck or fixture. Instead, the workpiece is positioned between two wheels the grinding wheel and the regulating wheel. This setup allows for a continuous process that can produce tightly tolerance parts with minimal operator intervention.
Common Abbreviations in Centerless Grinding
1. CNC (Computer Numerical Control) CNC technology has revolutionized manufacturing and is increasingly applied in centerless grinding. CNC enables precise control over the grinding process, facilitating automation and improving consistency. CNC centerless grinders can produce complex shapes and handle multiple setups without manual adjustments.
2. OD (Outside Diameter) OD refers to the measurement of the outer diameter of a cylindrical part. In centerless grinding, maintaining the correct OD is crucial for achieving the desired tolerances. CNC centerless grinders allow for automatic adjustments to ensure that the OD remains within specified limits.
3. ID (Inside Diameter) Although primarily associated with different manufacturing processes, ID is often relevant in the context of centerless grinding when dealing with parts that have internal features. While traditional centerless grinders are not designed for internal diameter grinding, hybrid machines that combine centerless and internal grinding capabilities are increasingly available.
4. RPM (Revolutions Per Minute) RPM is a critical factor in grinding operations, as it directly influences the speed of the grinding wheel. Higher RPMs can improve productivity, but they also require careful monitoring to prevent overheating and wear on the wheel.
abbr for centerless grinder products
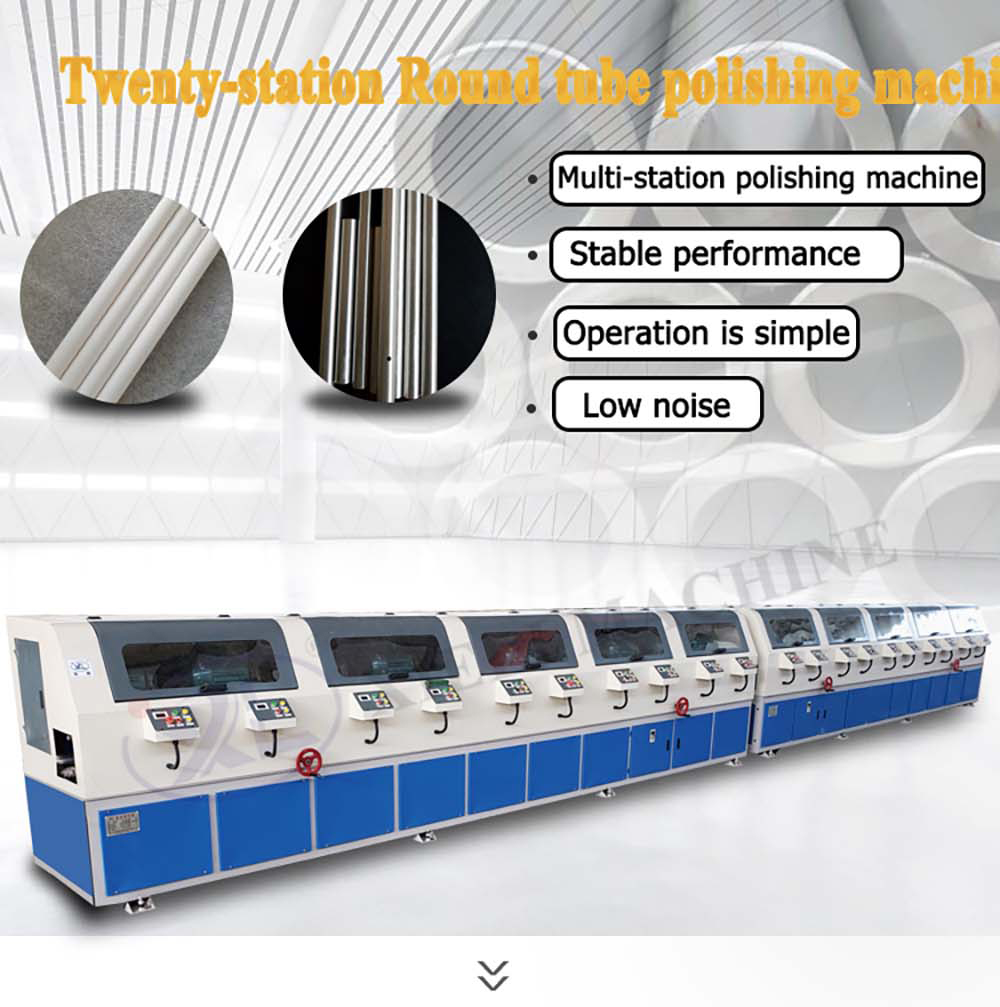
5. TIR (Total Indicator Reading) TIR is used to measure the roundness and accuracy of a part produced through centerless grinding. It is an essential metric for quality control, ensuring that components meet the required specifications before they are sent out for assembly or distribution.
6. GDT (Geometric Dimensioning and Tolerancing) GDT is a system for defining engineering tolerances and allowances. This approach helps in designing parts that can be consistently manufactured with high precision, ensuring that components can integrate seamlessly into larger assemblies.
7. SFM (Surface Feet per Minute) SFM measures the speed at which the surface of the grinding wheel moves against the workpiece. It is an essential factor in determining the efficiency of the grinding process. Adjusting the SFM can help in optimizing the grinding operations for different materials.
8. GRR (Grinding Repetition Rate) GRR is a measurement of the efficiency of a grinding machine. It denotes how many parts can be produced in a specific time frame. A higher GRR indicates better productivity, making it a critical parameter for manufacturers looking to improve throughput.
The Importance of Understanding Abbreviations
Knowledge of these abbreviations is crucial for effective communication among engineers, operators, and quality control personnel in the manufacturing environment. Understanding the terminology helps streamline processes, improves documentation, and ensures clarity during machine setups and quality checks. Additionally, as the industry evolves, new terms and abbreviations will continue to emerge, making ongoing education critical for those involved in centerless grinding.
Conclusion
In the realm of manufacturing, understanding the intricacies of centerless grinding and the terminology associated with it is fundamental to improving efficiency and ensuring high-quality production. By familiarizing oneself with common abbreviations, professionals can communicate effectively, make informed decisions, and contribute to the success of their operations. Whether you are an experienced machinist, an engineer, or a newcomer to the field, grasping these essential terms will empower you to navigate the complexities of centerless grinding with confidence and skill.